第一次拿到Find X手机时候,这种颠覆式的设计全面屏,一体无暇的机身,让人印象深刻。而在使用过程中,Find X就如同宝藏一般,被挖掘出更多的巧思和用途。
全面屏的功臣,双轨潜望结构的考验
93.8%的超高屏占比,3.8mm的全球最窄下边框,正面背面“无孔”机身,独家定制的曲面屏幕,这些数据背后,是OPPO设计师带着颠覆性ID的一次改革。
独创的双轨潜望结构把摄像头都藏在了机身里,不仅如此,还塞进了泛光传感器、距离传感器、点阵光投射与接收器、听筒,环境光感应器、高频天线等重要器件,这对空间利用,精加工都提出了很高的要求。
元器件堆放的考验是Find X整个项目组循环进行的验证、设计、打样、开模而最终确定下来的方案,尽量选择体积小的元器件,堆叠时间也是常规机型堆叠时间的3到4倍,只求做到完美。
升降结构的考验比较复杂,首先容易想到的就是升降机的寿命和耐久性,经过验证和权衡,Find X最终选择马达加螺纹丝杆的方案,来保证升降的可靠性和平稳性,而伸缩也可以在0.6s内完成,并且高达30万次的耐久性也让人放心使用;再者就是升降模块的轻薄化,要更好的突出全面屏,必须要保证视觉上的轻薄,0.3mm工艺的拥有热弯处理的盖板玻璃,是Find X给出的答案。
科学技术决定生产力,Find X量产的意义
要实现全面屏技术,所有的要求似乎都是量产的拦路虎。
比如,单是双轨潜望结构的堆叠的时间就远高于常规机型,0.3mm的盖板玻璃的热弯处理,Find X精密内部的产业线的组装,这些都不是简单的可以靠增加劳动力来实现量产的,是需要技术的指导和专业的工匠精神。
前期准备是漫长而枯燥的,是一次次实验的积累,一次次验证的反省,才能得到解决方案的“珠玉”。
元器件的堆叠是在压缩面积11.2%的情况下的一个挑战,没有捷径,只有一次次的评估验证,本着对用户体验不妥协的中心思想,重新设计Find X各个元器件,并尽可能的缩小体积。让堆叠有更多空间来选择。
热弯玻璃的工艺很复杂,热完成形后还需要做抛光和打磨,在0.3mm的工艺很容易使镜面发生碎裂,要保证能够量产的良品率,要密切关注其中的参数,包括温度和压力。OPPO团队步步跟进和指导供应商,将不可能变成了可能,并达到了量产标准。
由此可见,Find X内部结构相当复杂,这对组装也是挑战和考验。OPPO更新生产流程,另辟蹊径,引进一条单独生产线先行组装生产升降结构,再进行整机生产。
OPPO Find X在充满艺术感外观机身的背后,蕴藏着太多技术生产实力,在升与降之间,那仿佛窥探未来的眼睛开启,塑造者属于Find X的造型之美和技术之力。
-
OPPO
+关注
关注
20文章
5235浏览量
79121 -
全面屏
+关注
关注
5文章
907浏览量
41043
发布评论请先 登录
相关推荐
Find My技术|谷歌Find My Device与苹果Find My的差异
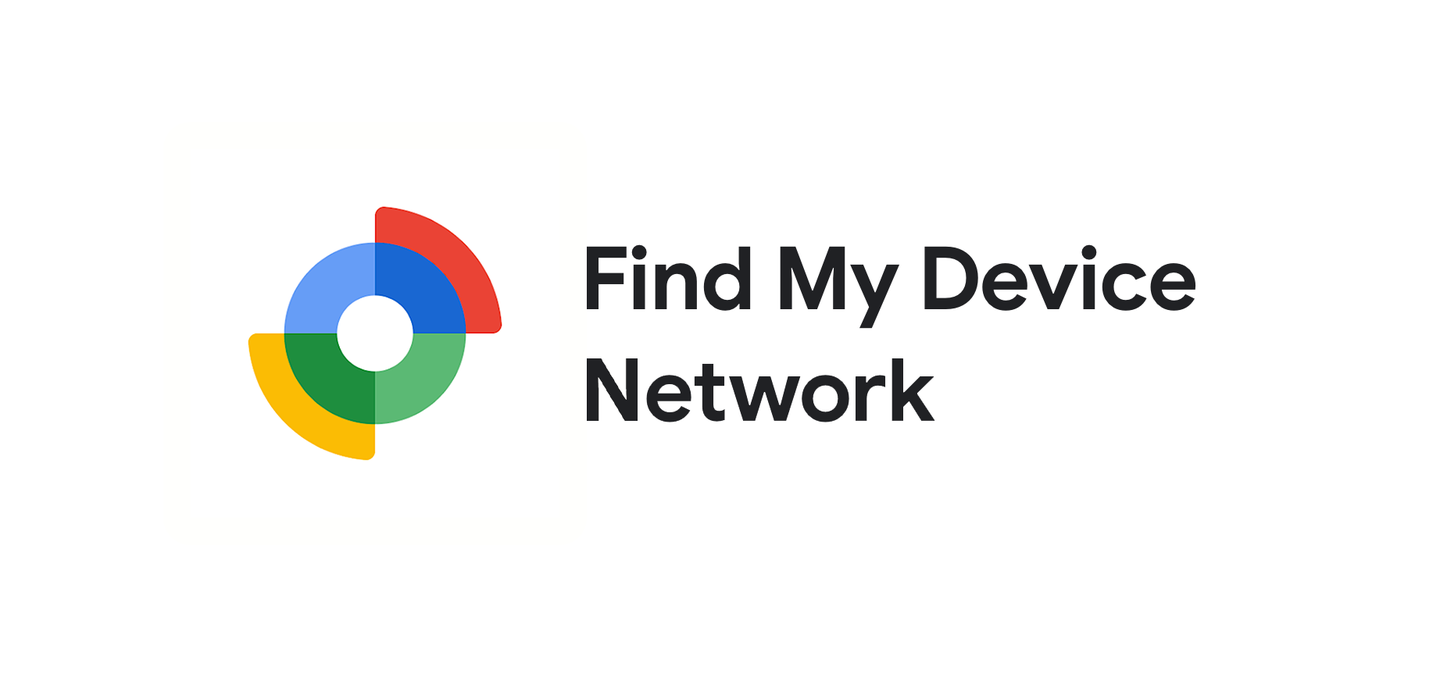
Find X8系列发布,OPPO与联发科强强联手打造AI手机旗舰标杆
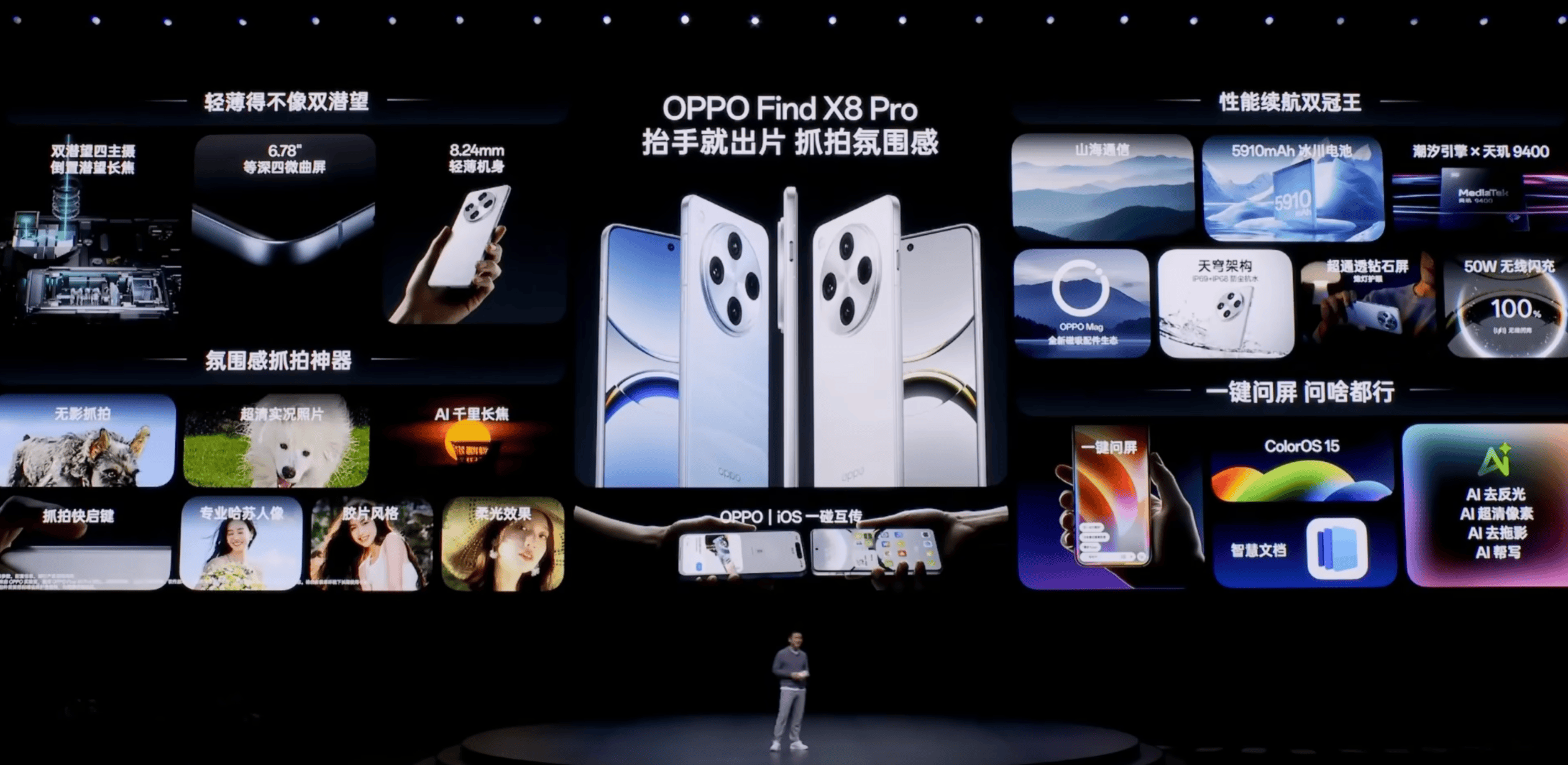
年度影像旗舰Find X8系列重磅登场,全系列新品打造旗舰新标杆
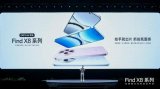
氛围感抓拍神器,OPPO发布年度影像旗舰Find X8系列
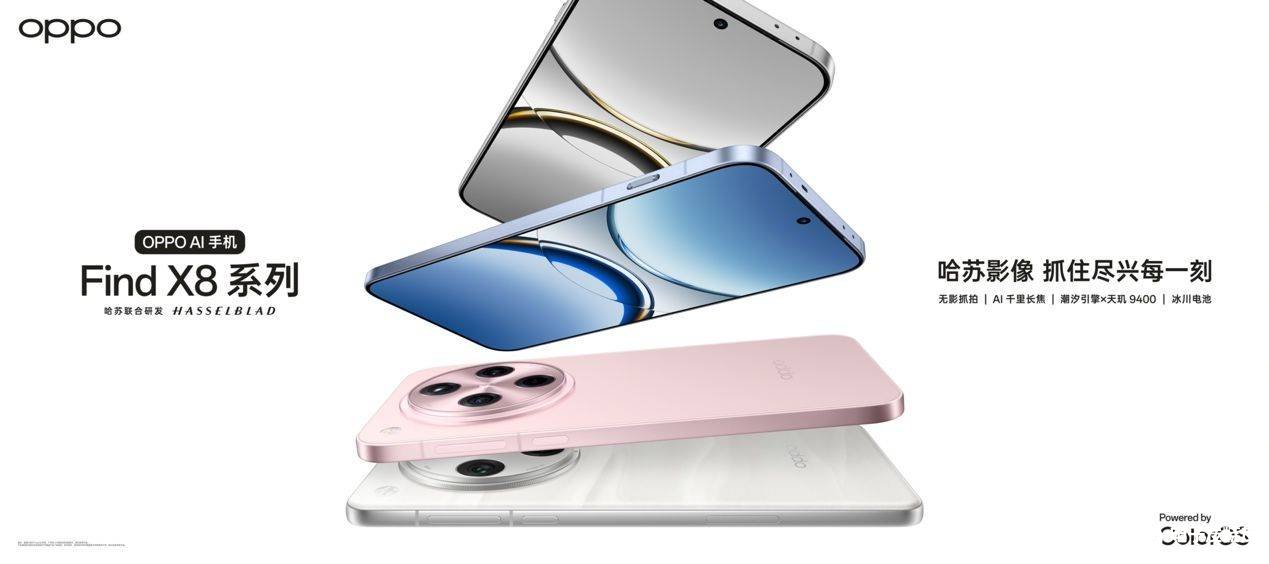
OPPO Find X8 Pro双潜望镜头引领影像新风尚
更简单、更全能的系统级AI,OPPO Find X8首发AI一键问屏
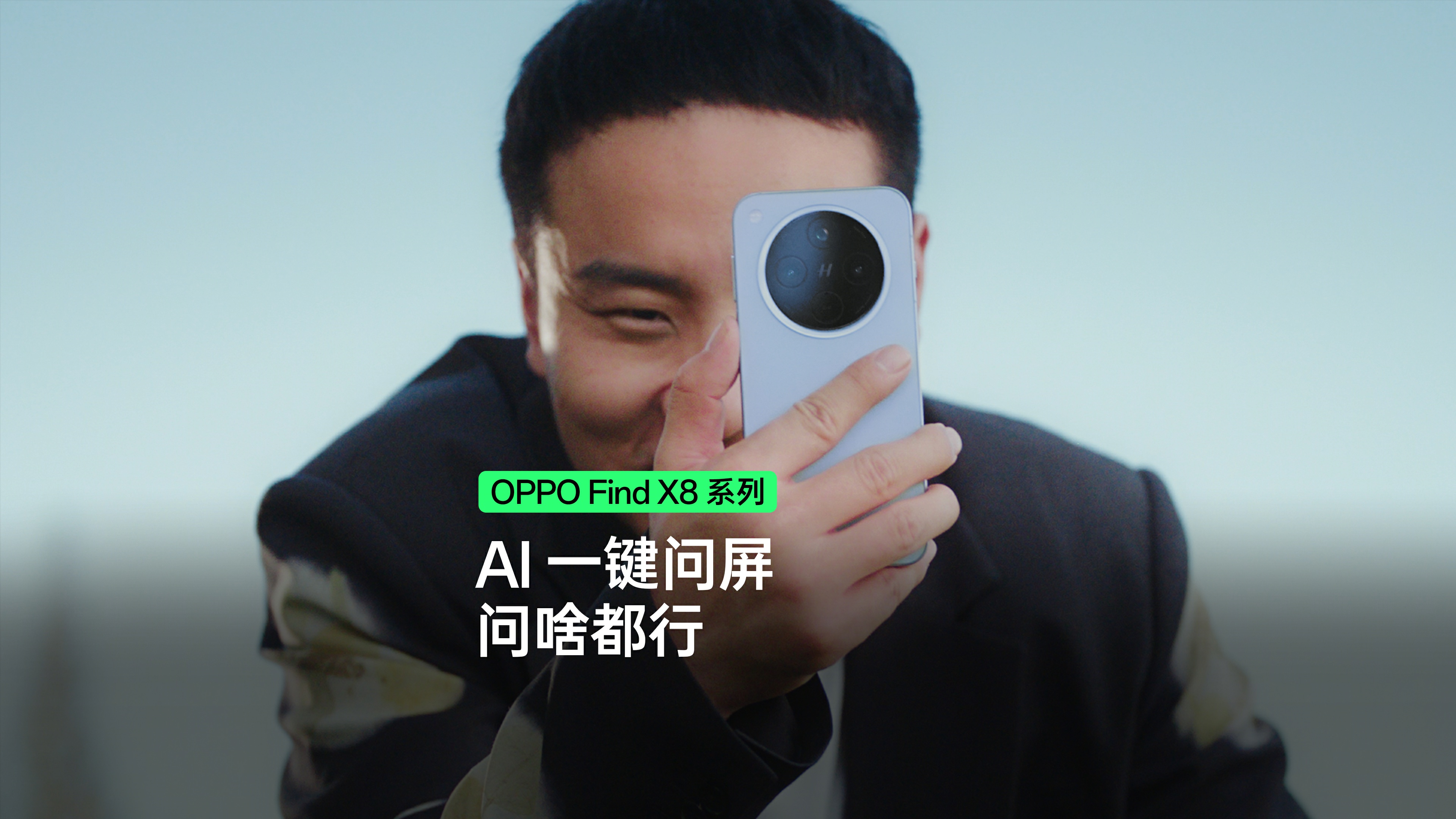
OPPO Find X8 Ultra与Find N5折叠机预计明年初发布上市
OPPO Find X8系列手机10月发布,新形态设计与影像系统令人期待
OPPO Find X8系列Q4初发布,Reno12系列本月下旬亮相
OPPO Find X7 Ultra现支持5.5G移动网络技术
OPPO Find X7系列行业首发5G-A技术
旗舰手机性能排行榜:OPPO Find X7与天玑9300独占鳌头
OPPO Find X7这个功能火了!背后离不开天玑9300强悍AI算力
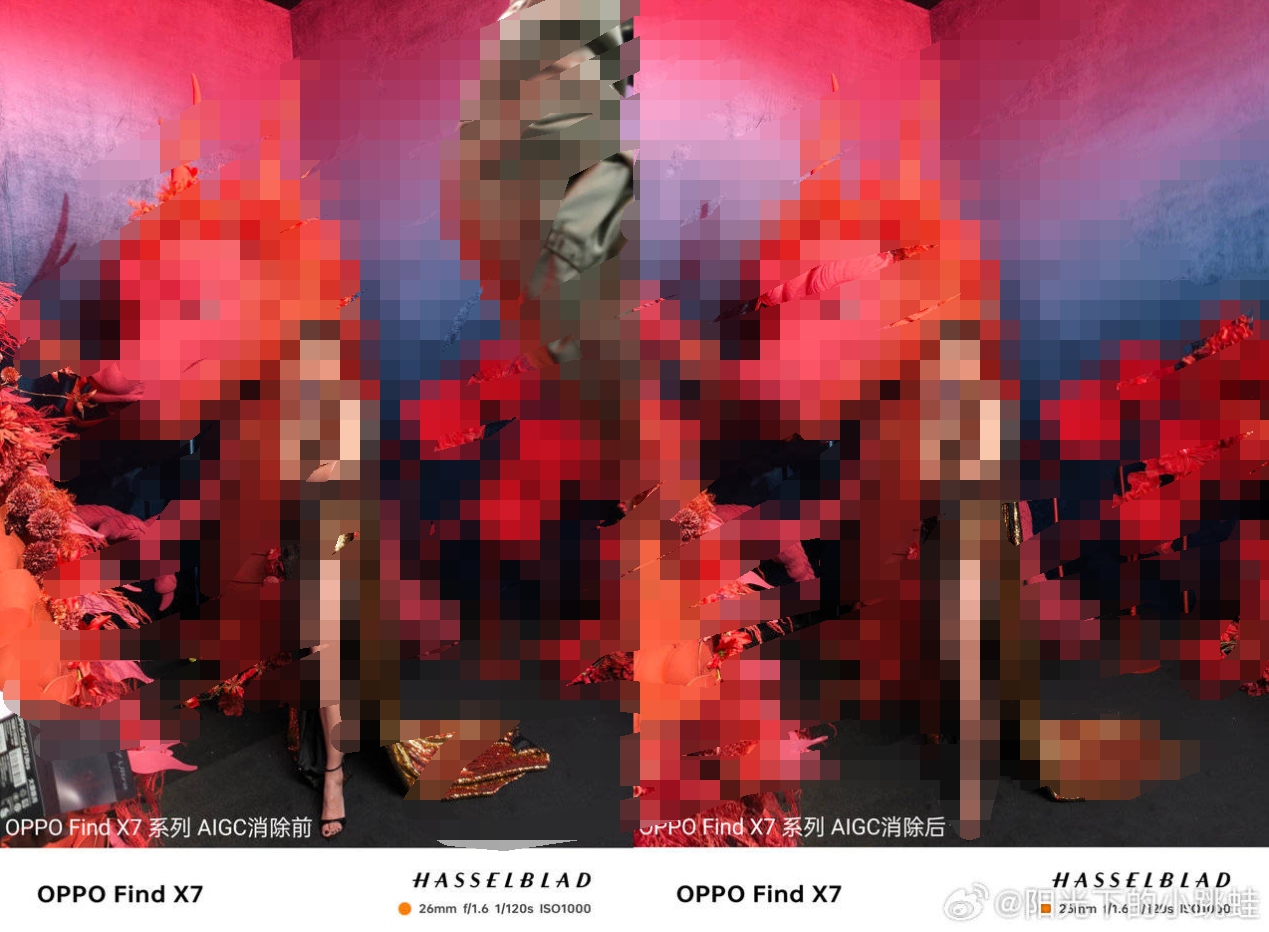
封神旗舰Find X7系列今日火爆开售,销量再创新高
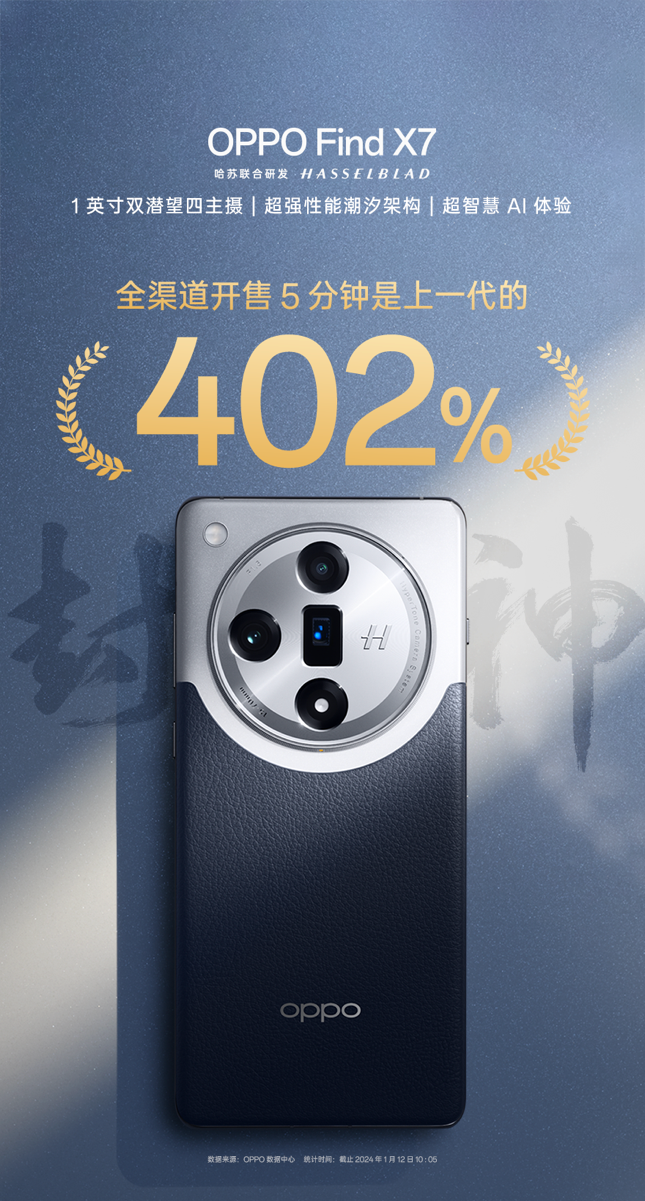
评论