张仁柏认为,作为一家专业的动力电池系统公司,普莱德也同动力电芯企业一样,面临既要高比能量,又要高安全的矛盾问题。
“我们连续五年独立第三方Pack企业排名第一,去年整个出货量大约是2.3GWh,今年预测4.7GWh。”
近日,北京普莱德新能源电池科技有限公司(下称“普莱德”)副总裁张仁柏在“中国(青海)锂产业与动力电池国际高峰论坛”上自信地表示,普莱德拥有300多项专利,其中发明专利136项,这成为公司产品市场竞争能力的保障。
目前,市场上搭载普莱德动力电池系统的车型数量达到3000辆车,已经运行了三年,体现了市场的接受度和技术可靠性。
▲普莱德副总裁张仁柏
张仁柏认为,作为一家专业的动力电池系统公司,普莱德首先就是要关注安全,但基于国家新能源汽车补贴退坡、双积分等政策的颁布,普莱德也同动力电芯企业一样,面临既要高比能量,又要高安全的矛盾问题。如何平衡两者,成为双方的共性问题。
为此,他以专业的动力电池系统企业角度,从整个电池系统的失效模式、四大电池系统安全、热管理系统设计、电池轻量化技术等多个方面进行了详细阐述。
(一)电池系统失效模式
动力电池系统安全肯定最先分析整个电池系统的失效模式。我列了一下有五项,一是电击,即电能非正常释放,然后是燃烧、爆炸、碰撞、腐蚀。
因为每卖一辆车基本质保条件是八年12万公里,在这种情况下腐蚀也会影响到车辆的可靠性。腐蚀也是关注安全的一个方面。
(二)四大电池系统安全
普莱德开发的创新点,电池系统安全测试至少有四大安全。第一个是化学安全,材料阻燃、电芯安全,包括一些标识。
第二个电气安全是系统上设计的重要关注点,膨胀力、传感、电压采集、温度采集,绝缘耐压、电磁兼容,电磁评比、漏液检测、冗余设计,交叉检验算法。
第三个机械安全。现在行业里面可以做到IP67,后续会做到IP68,这里面还有隔热、耐腐蚀、耐振动。
第四个最重要的是功能安全。基于ISO26262,把电池系统放在汽车里面,功能安全指自动灭火、主动&被动安全、碰撞过程中断开、高压。刚才孚能的王总也介绍了整个电池系统里面的容断等等设计,包括湿度、烟雾、短路、过充。
一个电池包的开发周期一般是24个月,其中光测试要求就要高于国标,或基本跟国际上持平,现在也增加了测试数量。
普莱德的产品安全采用全仿真的分析,有静力、球击、模态、振动,还有冲击、挤压、疲劳和碰撞。从电芯到模组级的仿真模型,这都是必备的设计。很多厂家找我们说三个月开发一个电池包,这确实很难,一般测试都是标准24个月的周期。
(三)安全与能量密度如何平衡
基于新能源汽车补贴退坡和双积分的推动,大家看到我们做电池系统和做电芯一样,也是一个矛盾体,既要高比能量,又要高安全,这要如何平衡呢?这是一个共性问题。
除了电芯温度提高,Pack结构设计也是提升能量密度的重要方面,同时要保障整个动力电池系统安全,这是我们每天都要考虑的问题。
目前,能量密度目标,整个行业的平均成组效率在65%,普莱德项目目标是80%;安全性的目标,我们通过BMS的核心技术、系统控制策略优化、结构优化,还有一些系统设计,希望把电池系统保持零事故,这里面基本涉及七大方面:集成模组设计、系统轻量化、广义BMS的设计、热设计、梯次利用等。
热管理系统设计方面,我们携带的主要产品都是采用液冷方式,因为能量密度提升对热管理、保障安全很重要。
系统轻量化设计方面,从以前的钣金到冲压,现在全面转接到高强度铝和复合材料,我们在模组设计里面再加上一些固定边框,同时加强了温度传感器和电压测试系统,能够保障能量密度达到一定的指标。
BMS方面,除了对产品的检控以外,我们对SOC、SOP、SOH的管理也做了后台大数据,保障每一辆车在运行过程中都有数据记录,实现数据全面可追踪,监督它的健康状况并进行预测。
除从上述三方面着手外,普莱德进一步解释了集成标准模组的设计、系统轻量化设计,并针对全生命周期的广义BMS和热设计做了一些工作。
这是我们的自动化工艺设计里面的部分,包括我们的光学检测、激光连续焊、工装模块化的组装、CMT机器人,还有一拖二双工位焊接工艺,大大提升了制造的效率和可靠性。
其中,重点讲BMS里面的大数据库部分。整个工作原理是,通过电池系统运营、电池系统参数传输、模式算法,最后达到经由云平台传输到数据库里面进行结果的可视化和电池保养的提示。保证我们的产品出去以后除了BMS在车上的重视,也有后台数据库的实时跟踪。
(四)电池轻量化
轻量化方面,普莱德从结构、材料和工艺里面做了一些具体工作。比如结构上,普莱德有一个Pack结构设计。
汇总一下整个对于安全、能量密度和可靠性做的一些工作。这是整个电池包的拓扑图,里面包括模组、电子电气、热管理、电池连接件、辅助材料等等。
这是260km和350km两个电池包的对比,我们是用实施铝合金型材电池壳体技术方案分析,保证强度与可靠性基础上,控制模具投资,实现重量和成本的降低,同时关注电池下壳体选材,对比重量范围、模具投入、生产节拍和成本预估四方面进行分析。
从成本来讲,以前讲铝材一般的成本是钢材的三倍,重量是钢材的1/3,但是现在通过技术提升,成本能够控制在3000元左右,但是开发时间也严重缩短,从6个月缩短到1个月,重量从以前一个电池包60公斤降到40公斤。
这是整个的数据对比,材料强度、抗拉强度、断裂伸长度等。这是结构差异和不同的可靠性的数据分析。
通过这种分析大家可以看到,挤压铝型电池的壳轻量化效果明显,开发周期短,投资最小,并且生产效率高、成本低,所以现在从今年开始全面转换成一个产品设计思路。
-
动力电池
+关注
关注
113文章
4539浏览量
77743 -
电芯
+关注
关注
14文章
731浏览量
25904
原文标题:【派勒智能•洞见】预计出货量4.7GWh 张仁柏谈普莱德安全与能量密度平衡
文章出处:【微信号:weixin-gg-lb,微信公众号:高工锂电】欢迎添加关注!文章转载请注明出处。
发布评论请先 登录
相关推荐
芯和半导体荣获2024上海软件核心竞争力企业
出货量持续称霸全球,联发科天玑芯片强在哪?

江波龙自研SLC NAND Flash累计出货突破1亿颗
隆基绿能强化市场竞争力,引领光伏行业新发展
北京芯片独角兽芯驰科技:出货量破600万片,加速驶向全球舞台
强达电路:持续提升创新能力,增强市场竞争力
强达电路:持续提升创新能力,增强市场竞争力
SK海力士与Amkor携手推进硅中介层合作,强化HBM市场竞争力
英伟达去年数据中心GPU出货量占比约98%
全球车载显示面板出货量预测:大陆地区面板厂领先
EMC测试整改:提升产品合规性和市场竞争力?|深圳比创达电子
2023年中国AR/VR市场业绩概览:AR出货量攀新高,VR销量下滑
GGII:2023年国内储能锂电池出货量超200GWh
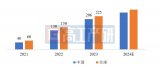
评论