随着科学技术水平不断的提高,磨削加工已广泛应用于金属及其他材料的粗、精加工,是非常重要的切削加工方式。目前,磨削加工已经成为现代机械制造领域中实现精密与超精密加工最有效、应用最广泛的基本工艺技术,为人们提供高精度、高质量、高度自动化的技术装备的开发和研制。
精密磨削中超硬磨料砂轮
精密磨削技术
磨削是指用磨料或磨具去除材料的加工工艺方法,一般来讲,按照砂轮线速度的高低可将其进行分类,把砂轮速度低于45 m/s的磨削称为普通磨削,把砂轮速度高于45 m/s的磨削称为高速磨削,把砂轮速度高于150m/s的磨削称为超高速磨削。
按磨削效率将磨削分为普通磨削、高效磨削(高速磨削、超高速磨削、缓进给磨削、高效深切磨削、砂带磨削、快速短行程磨削和高速重负荷磨削)。
磨削加工能达到的磨削精度在生产发展的不同时期有不同的精度范围,当前,按磨削精度将磨削分为普通磨削(加工精度>1μm、表面粗糙度R a0.16~1.25μm)、精密磨削(加工精度1~0.5μm、表面粗糙度R a0.04~1.25μm)、超精密磨削(加工精度≤0.01μm、表面粗糙度R a≤0.01μm)。
精密加工是指在一定发展时期中,加工精度和表面质量达到较高程度的加工工艺,当前是指被加工零件的加工精度为l~0.1µm,表面粗糙度值Ra0.2~0.01µm的加工技术。
精密磨削是目前对钢铁等黑色金属和半导体等脆硬材料进行精密加工的主要方法之一,在现代化的机械和电子设备制造技术中占有十分重要的地位。
精密磨削一般使用金刚石和立方氮化硼等高硬度磨料砂轮,主要靠对砂轮的精细修整,使用金刚石修整工具以极小而又均匀的微进给(10~15mm /min)。获得众多的等高微刃,加工表面磨削痕迹微细,最后采用无火花光磨。
由于微切削、滑移和摩擦等综合作用,达到低表面粗糙度值和高精度要求。高精密磨削的切屑很薄,砂轮磨粒承受很高的应力,磨粒表面受高温、高压作用,一般使用金刚石和立方氮化硼等高硬度磨料砂轮磨削。
精密与超精密磨削的机理与普通磨削有一些不同之处:
1)超微量切除。应用较小的修整导程和修整深度精细修整砂轮,使磨粒细微破碎而产生微刃。一颗磨粒变成多颗磨粒,相当于砂轮粒度变细,微刃的微切削作用就形成了低粗糙度。
2)微刃的等高切削作用。微刃是砂轮精细修整而成的,分布在砂轮表层同一深度上的微刃数量多,等高性好,从而加工表面的残留高度极小。
3)单颗粒磨削加工过程。磨粒是一颗具有弹性支承和大负前角切削刃的弹性体,单颗磨粒磨削时在与工件接触过程中,开始是弹性区,继而是塑性区、切削区、塑性区,最后是弹性区,这与切屑形成形状相符合。
4)连续磨削加工过程。工件连续转动,砂轮持续切入,开始磨削系统整个部分都产生弹性变形,磨削切入量(磨削深度)和实际工件尺寸的减少量之间产生差值即弹性让刀量。此后,磨削切入量逐渐变得与实际工件尺寸减少量相等,磨削系统处于稳定状态。最后,磨削切入量到达给定值,但磨削系统弹性变形逐渐恢复为无切深磨削状态。
精密磨削技术的历史与发展
磨削加工是利用磨料去除材料的加工方法,也是人类最早使用的生产技艺方法。
18 世纪中期世界上第一台外圆磨床问世,由石英石、石榴石等天然磨料敲凿成为磨具,用天然磨料和粘土烧结成砂轮,随后又研制出平面磨床。
20 世纪40 年代末,人造金刚石出现;1957 年立方氮化硼研制成功;随着磨削技术的发展,特别是超硬磨料人造金刚石砂轮与立方氮化硼砂轮的应用,磨削加工应用范围日益增大,磨削加工精度及加工效率也不断提高。
磨削技术得到快速发展,磨床在加工机床中也占有相当大比例。据1997 年欧洲机床展览会(EMO)调查数据表明,25% 企业认为磨削是他们应用最主要加工技术,车削只占23% ,钻削占22% ,其它占8% ;而磨床在企业中占机床比例高达42% ,车床占23% ,铣床占22% ,钻床占14% 。
我国从1949~2007 年,开发生产通用磨床有1800 多种,专用磨床有几百种,磨床拥有量占金属切削机床总拥有量15% 左右。可见,磨削技术及磨床在机械制造业中占有极其重要位置。
近年来,国外对精密和超精密磨削技术的开发研究获得了不少成果,主要体现在ELID镜面磨削新工艺的研究和加工硅片以及非球面零件的应用上。
日本国家理化学研究所的大森整教授于1987年研制成功了在线修整砂轮的ELID镜面磨削新工艺。
ELID镜面磨削技术是利用在线电解修整作用连续修整砂轮来获得恒定的出刃高度和良好的容屑空间,同时,在砂轮表面逐渐形成一层钝化膜,当砂轮表面的磨粒磨损后,钝化膜被工件表面磨屑刮擦去除,电解过程继续进行,对砂轮表面进行修整,加工表面粗糙度Ra达到0.02~0.01µm,表面光泽如镜。
美国在应用ELID磨削技术加工电子计算机半导体微处理器方面已取得突破性进展,在国防、航空航天及核工业等领域的应用研究也在进行,PeiZJ等人对自旋转磨削法精密磨削硅片的加工过程以及加工参数、砂轮粒度、冷却液供给等加工条件对磨削力、硅片面型精度、表面磨削纹路、表面粗糙度的影响进行了系统的试验研究。
德国是最早研究ELID磨削技术的几个国家之一。在1991年就有德国的机床厂家进行了系列ELID专用机床的设计。此外,英、法等国对ELID磨削技术也进行了深入的研究。
我国对精密磨削的研究尚处于初级阶段,主要集中在高校。哈尔滨工业大学以袁哲俊教授为首的ELID课题组研制成功了ELID磨削专用的脉冲电源、磨削液和砂轮,在国产机床上开发出平面、外圆和内圆ELID磨削装置,实现了多种难加工材料的精密镜面磨削。目前正积极推广普及该技术,实现其产品化。东华大学机械学院的研究者利用固结磨粒低频振动(频率f为0.5~20Hz、振幅为0.5~3mm)压力进给的精整加工,研究了适宜的经济加工条件及有关参数,并验证了经过磨削加工后的陶瓷工件,再经过超精加工可以进一步降低其表面粗糙度,可降低2~4个等级。清华大学在集成电路超精密加工设备、磁盘加工及超精密砂带磨削和研抛、金刚石微粉砂轮超精密磨削等方面进行了深入研究,并有相应产品问世。
ELID磨削技术
ELID磨削技术是应用电化学反应的非传统材料去除技术来解决金属基超硬磨料砂轮的修整问题的超精密镜面加工技术,以其效率高、精度高、表面质量好、加工装置简单及适应性广等特点,已较广泛用于电子、机械、光学、仪表、汽车等领域。
ELID磨削的基本原理
ELID(Electrolytic In-process Dressing)磨削是在磨削过程中,利用非线性电解修整作用使金属结合剂超硬磨料砂轮表层氧化层的连续修整用与钝化膜抑制电解的作用达到动态平衡。从而获得稳定厚度的氧化层,使砂轮磨粒获得恒定的出刃高度和良好的容屑空间,实现稳定、可控、最佳的磨削过程,它适用于硬脆材料进行超精密镜面磨削。
ELID磨削的必备装置主要有磨床、电源、电解装置、电解液和砂轮五个要素。
其工作原理是:金属结合剂超硬磨料砂轮的转轴与电刷的接触而接通电源正极作为阳极,铜电极(工具电极)与电源负极相接作为阴极。砂轮与负极之间存在100~500μm的间隙(间距可调),利用喷嘴喷出具有电解功能的磨削液使之充满间隙。在高电压(60~120v)和高脉冲频率电源的作用下,使磨削液电解产生阳极溶解效应,将砂轮表层的金属基体电解去除,与此同时,在砂轮表面会产生一层绝缘的钝化膜能有效抑制金属基体的过度电解,以减少砂轮基体的过分电解损耗。因为氧化膜极易磨损,从而容易使新的磨粒露出锋利的棱角以达到修锐效果。整个加工过程中电解作用与钝化膜的抑制作用达到动态平衡,保证了磨粒的恒定的突出量,使砂轮在加工过程中始终保持有磨粒突出的最佳磨削状态。该技术将砂轮的在线修整与磨削过程结合在一起,从而实现对工件的连续超精密镜面磨削。
ELID超精密磨削的过程可分为四个阶段,具体归纳如下图。
如下图ELID镜面磨削基本原理图(a)所示,在砂轮修正前,砂轮由磨粒和金属结合剂组成,磨粒均匀分布。在进行磨削加工前,需单独对砂轮进行电解修整工作(图b),在砂轮表面电离溶解一层金属结合剂,以一定厚度的钝化膜取而代之。一方面能有效减小砂轮的形状误差,另一方面能预先生成具有一定弹性的钝化膜,防止开始磨削时砂轮切入是造成工件的硬质划伤。
在磨削开始后,由于氧化膜极易磨损,固定在氧化膜中的磨粒路出锋利的棱角,其可以视为无数大小型刀具对工件表面进行微切削作用。砂轮在通过与工件的接触区域后,由于工件材料的刮擦作用,磨粒磨损钝化,出刃高度降低,磨削效果变弱。由于钝化膜变薄,导电性恢复,当砂轮转到工具电极位置时,在电解液的作用下,砂轮表面形成新的氧化膜,使磨料出刃高度增加(如图c)。当氧化膜达到磨损前的厚度时,电阻足够大而起到绝缘作用,使电解作用终止。
由此可知,由于这种非线性电解作用的结果,使得修整过程对磨削过程有一定的自适应能力,砂轮在每个旋转周期内都保持以相同厚度的氧化层和相同出刃高度的磨粒进行磨削,即砂轮表层氧化膜的电解生成与磨损达到动态平衡,最终使得砂轮表面结合剂基体不断被电解,新的磨料不断地露出,以保证金属基砂轮在磨削过程中的锐利性。
这种磨削方法即不会由于表层磨料的磨损和脱落而失去切削能力造成切屑堵塞现象,又不会造成砂轮的过快消耗,能充分发挥超硬磨料的磨削能力,非常有利于对硬脆材料实现高精度、高效率的超精密镜面磨削。
精密磨削存在的问题以及发展前景
精密和超精密磨削技术在各方面均取得迅速发展,已成为先进制造技术的关键技术之一.在今后的研究中应着重关注以下几个问题:
1)超精密磨削的基本理论和工艺研究,着重研究多颗粒磨削机理、磨削表面生成及影响因素等;
2)开发高精度、高性能、高自动化的加工机械及测试装置的移动导向机构及轴承;
3)目前ELID镜面磨削技术存在的问题是向高速回转的砂轮供电非常困难,通常采用接触式电刷供电设备,该设备复杂昂贵,影响了ELID镜面磨削技术的推广应用;
4)开发适于超精密加工并能获得超高精度,超高表面质量的新型材料,如超微粉烧结金属、新高分子材料等。
磨削技术发展很快,在机械加工中起着非常重要的作用。目前,磨削技术的发展趋势是:发展超硬磨料磨具,研究精密及超精密磨削、高速高效磨削机理并开发其新的磨削加工技术,研制高精度、高刚性的自动化磨床。
随着机械产品精度、可靠性和寿命的要求不断提高,高硬度、高强度、高耐磨性、高功能性的新型材料的应用增多,磨削加工技术在磨削机理、磨料磨具开发、精密超精密磨削、高速超高速磨削、磨削自动化和智能化、磨削工艺过程监控与检测技术、磨削加工软件技术等方面发展迅速,在机械加工中起着至关重要的作用。因此,我们应深入研究国外先进磨削技术,系统地开展和推广各种先进与实用的磨削技术,积极推进我机械制造工艺技术的进步。
上海康汇研发生产的U-How®容积式旋转活塞流量计,属于精密加工计量器件,经过北京市计量检测科学研究院检测认证,精度达到1.0级。为确保流量计转子达到50万转次以上和腔体容积的稳定性,腔体及转子等主要部件,均用精密磨削工艺加工,保证部件尺寸精度达到1μm以上。
U-How®康汇燃油流量计
U-How®康汇流量计是上海康汇实业发展有限公司,根据旋转活塞式工作原理自主研发生产的,具有测量流速低、量程宽、精度高、结构简单、工作安全可靠等特点的高精度流量传感器。
工作原理
旋转活塞式流量计,是属于容积式流量计,它基于活塞与计量室一直保持的相切密封状态。并有一个固定的偏心距计量元件活塞,在压差的作用下,对活塞产生转动力矩,使活塞做偏心旋转运动,活塞的转数正比于流体的流量,通过记数机构记录出活塞转数,即可测得流体总流量。
旋转活塞式流量计进出口由隔板隔开。当被测流体从进口进入计量室,这时进出口形成压差,迫使活塞逆时针旋转如图a所示。流体连续流入,迫使活塞转动如图b所示,形成二个半月牙腔体,在压差作用下迫使活塞转动如图c,V2流体从出口排出,使活塞转动如图d所示,在压差作用下转动,活塞每转一周迸出的流体等于V1+V2的和。
工作原理图
流量计爆炸图:
产品参数
1、机械部分:
型号 |
PDFM 4D |
PDFM 8D |
PDFM 8Db |
液压连接器 |
M14 x1.5 |
M14 x1.5 |
M16/22 x1.5 |
最大工作压力 (MPa) |
2.5 | 2.5 | 2.5 |
测量范围 (l/h) |
1~ 80 |
20~ 200 |
80~ 320 |
精度 (﹪) | ±1 | ±1 | ±1 |
重复率 (﹪) | ±0.2 | ±0.2 | ±0.2 |
测量室体积 (ml) |
5 | 12.44 | 12.44 |
内置滤网尺寸 (mm) |
0.125 | 0.15 | 0.15 |
工作温度 (℃) |
﹣20 ~80 |
﹣20 ~80 |
﹣20 ~80 |
存储温度 (℃) |
﹣40 ~100 |
﹣40 ~100 |
﹣40 ~100 |
2、电子部分:
型号尺寸 | KHDQ |
工作电压 (V) | 9~40 |
输出接口 | RS485/RS232 |
数据线 | 2×0.75 |
工作温度 (℃) | ﹣20~80 |
存储温度 (℃) | ﹣40~100 |
测量介质:
可测量轻质和中质油料,如:汽油、柴油、煤油、石脑油、润滑油
产品资质
1. 发明专利:ZL201020504169.8流量传感器
2. 国家汽车质量监督检验中心车辆检测报告
3. 交通部委托北京计量院精度检测报告
油耗监控解决方案
应用对象
1.发动机:
火车、汽车、工程车、拖拉机、发电机组及内河或近海航行的船舶中测量各类动力机器的燃油消耗量,及各种较重液体的装卸计量和管道过液计量。
2.燃烧器:
车载锅炉、移动锅炉等设备的燃油消耗计量。
数据采集方式
通过采集流量计脉冲数据的方式,以RS485/RS232对接设备单位的系统集成
解决方案
实施案例
某大型石油集团:
吊管机、移动电站、多功能车、弯管机、空压机等
某大型采油厂:
锅炉车、清蜡车、超导车、水泥车、吊车等;
港口:
龙门吊、堆高机、正面吊、装载机等
其它:
轮胎胎压油耗测试;驾驶员驾驶技术比武;发动机性能标定
空压机
锅炉车
-
自动化
+关注
关注
29文章
5585浏览量
79311 -
机械制造
+关注
关注
1文章
105浏览量
15098
原文标题:高端制造的精密磨削技术
文章出处:【微信号:WW_CGQJS,微信公众号:传感器技术】欢迎添加关注!文章转载请注明出处。
发布评论请先 登录
相关推荐
什么电阻才属于精密电阻?精密电阻技术的历史演进
RTOS发展历史
INA轴承影响磨削变质层的因素
嵌入式系统的发展历史
如何延长磨削电主轴的寿命?深圳厂家教你
磨削电主轴保养方法 深圳厂家告诉你
磨削温度场的计算机仿真技术的应用研究

功率放大器超声椭圆无心磨削技术研究中的应用
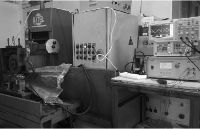
评论