作者简介:张发林,从事嵌入式系统软硬件研发工作超过20年,目前在上海未来伙伴机器人有限公司担任电子总工程师。深入理解从产品需求分析、方案论证设计、技术研发、产品化、测试认证、批量量产等各环节的难点、痛点,解决过大量研发、产品化和生产难题,参与或领导开发的多款工业自动化设备、通信设备、监控系统、物联网及机器人产品等均已投入大规模量产销售。
一块新设计的电路板经过SMT、波峰焊或手工焊接后变成了PCBA,算是万里长征第一步。然而从PCBA到最后定型交付工厂量产,中间还需要经过一系列的测试和验证工作。很多年轻的电子工程师对于PCBA和电子产品系统调试步骤和各阶段具体要求不清楚,常常导致开发调试效率低下,甚至损毁待测电路板。更可怕的是将有功能或性能缺陷的设计转到量产阶段,给公司造成巨额损失。笔者根据多年亲身实践,总结出从PCBA到产品定型的九个步骤,高效完成了多款电子产品的研发工作。
第一步 目视检查
刚刚贴装好交付到电子工程师手上的PCBA如图一所示,有经验的工程师通过目视检查就能快速发现很多设计、物料和工艺问题,可节省大量后续调试时间。
1.1. 仔细对照电路图,检查确认原理图、PCB图和BOM的版本和拿到手的实物是否吻合,确认PCBA实际焊接的重要元器件和电路图是否吻合等。
1.2 检查板子上是否有锡珠锡渣,连焊虚焊,是否有明显的掉件漏焊;轻轻拔一拔个头比较大的元器件,特别是电解电容、大功率电感以及手插件,仔细观察还接位置是否居中准确,焊点是否牢固。
1.3 注意检查电源线排列,重要IC贴装方向、二极管AK方向、极性电容的极性,接插件的缺口方向。
图1 PCBA实物图
第二步 阻抗测试
本步骤相对简单,但是却极其重要,很多严重问题都是忽略了本步导致的。请务必反复核实所需要加载的的电源极性和电压,通过万用表检查各路输入输出电源与地之间是否有短路,是否有明显的阻抗异常,如有任何异常务必排除之,万不可心存侥幸。
图二 数字式万用表
第三步 上电检查
怀着惴惴不安的心情,估计你已经迫不及待的想给你的电路板通电工作了。好吧,可以上电,但要抱着随时壮烈牺牲的准备正确加电。将电源线负极接到实验电源的负极,确认实验电源的输出电压无误后,将电源线正极轻轻搭接在实验电源接线端子的正极,不要急于用仪器观测波形和数据,只关心PCBA通电瞬间是否有异常现象,如冒烟、起火、电火花、异常气味、器件爆裂等,具体惨象如图三所示。如果有异常立即移开电源线,返回到第一步排查问题,待问题查明处理后方可重新进行本步骤。确认无异常后方可正式上电,观察一段时间未发现异常或存在明显发烫的IC后即可进入下一步。
图三 冒烟的电路板
第四步 静态测试
PCBA正式上电后,对照硬件设计说明书,按照以下步骤进行静态测试。
4.1 工作电压和工作电流测量
直流电压的测试非常方便,可直接测量。而电流的测量就不太方便,通常采用两种方法来测量。若电路在印制电路板上留有测试点,可串入电流表直接测量出电流的数值,然后再用焊锡连接好。若没有测试孔,则可测量直流电压,再根据电阻值大小计算出直流电流。对于存在多种电源的电路,还要测试各路电源的上电时序,如图四所示。
图四 电源上电时序图
4.2 处理器最小系统缺省状态测试
需要确认处理器复位电平的极性和波形、晶振电路的频率、输入配置引脚的状态、输出控制引脚的初始状态。单片机晶振电路波形图如图五所示。
图五 单片机晶振电路波形图
4.3 逻辑电路初始状态测试
重点关注芯片的片选信号、使能信号以及配置管脚的缺省状态是否满足要求。如图六所示的DIR_485引脚的缺省状态为低。
4.4 模拟电路工作点测试
需要测试并优化放大器、三极管、MOS管等直流静态工作点。如图七中R1和R2的阻值需要根据MOS管的参数进行计算并根据实测结果调整。
图七: MOS管工作点调试示意图
第五步 功能调试
本阶段通常需要软件驱动配合,需要用到各种专业仪器设备如信号发生器、逻辑分析仪、示波器、频谱分析仪、电子模拟负载等。
5.1 打通处理器调试接口,实现软件程序下载运行和状态输出;如图八所示。
图八 Jtag仿真器调试示意图
5.2 验证人机交互功能,信息指示功能正常;
5.3 通过程序控制,驱动数字电路,观测输出信号波形、幅值、脉冲宽度、相位及动态逻辑关系是否符合要求。验证逻辑控制和通信接口功能,输入状态正确和输出状态可控;
5.4 调整模拟电路的交流通路元件,如电容、电感等,使交流信号的波形、幅度、频率等参数达到设计要求;
5.5 输入单阶跃信号测试电路状态变化的逻辑关系是否满足要求;
5.6 验证驱动电路在空载或轻负载条件下工作是否正常。
5.7 所有功能调试完成后应提交功能调试报告如表一所示
表一 功能调试验证报告
第六步 性能测试
电路经动态调试正常之后,便可对要求的技术指标进行测量。如传输速度、误码率、无线传输距离、信噪比等进行测试并记录测试数据,对测试数据进行分析,最后作出测试结论,以确定电路的技术指标是否符合设计要求。如有不符,则应仔细检查问题所在,一般是对某些元件参数或软件配置加以调整和改变。若仍达不到要求,则应对某部分电路或配置进行修改,甚至要对整个电路重新加以修改。因此,要求在设计的全过程中,要认真、细致,考虑问题要更周全。具体测试结果如表二所示。
表二 性能测试分析表
第七步 一致性测试
经过性能测试并确认满足设计要求后,根据实际情况至少需要进行3块以上的功能和性能一致性测评,对于电压、电流、延时、信号波形等进行对比测试,如有明显偏差务必不能掉以轻心,要认真分析可能存在设计、物料、加工工艺或调试测试方案的缺陷不足。如表三所示即可分析存在的是偶发问题还是批次性问题。
表三 47套产品工作电流一致性测试
第八步 系统联调
经过一致性测试通过的PCBA需要安装固定到整机系统中进行系统联调,原则上也要进行系统级别的一致性测试。
系统联调的过程中最常见的问题是PCBA和结构的干涉;无线通信天线位置对通信性能的影响;散热条件恶化导致的性能下降,通信误码率导致的功能或性能下降,音视频部分受箱体的影响;负载能力不足导致的电机堵转或过热保护,系统电源供电能力不足导致的各种异常等。由于电子产品的种类繁多,需要结合系统框图进行仔细排查。某产品的系统框图如图九所示。
图九 某产品系统框图
第九步 型式试验
型式试验是电子产品研发阶段的重要环节,是产品从研发转向生产的关键性节点,也是产品能否定型的重要依据。具体测试的内容和要求根据产品的类型和要求不尽相同。但大致范围和测试项目相差不大,如某产品的型式试验大纲如图十所示。
图十 某产品型式定型试验大纲
结束语
当前电子产品包罗万象,集成芯片和功能电路也层出不穷,再加上嵌入式系统机械、电子和软件的高度相关,PCBA到系统联调难度都在逐渐加大。另外由于市场竞争激烈,电子产品研发周期不断压缩,这就对电子工程师的从PCBA到产品定型全过程调试能力和能力提出较高要求。电子产品的形态和具体应用的电子技术虽有不同,但调试的基本流程、步骤和注意事项高度相通,九步调试法对于各行业的电子工程师都具有一定的参考和借鉴作用。
-
电路图
+关注
关注
10361文章
10726浏览量
533742 -
元器件
+关注
关注
113文章
4754浏览量
92994 -
PCBA
+关注
关注
23文章
1545浏览量
52011
原文标题:掌握这九步调试法,高效实现PCBA样板到量产
文章出处:【微信号:eedesigner,微信公众号:eeDesigner】欢迎添加关注!文章转载请注明出处。
发布评论请先 登录
相关推荐
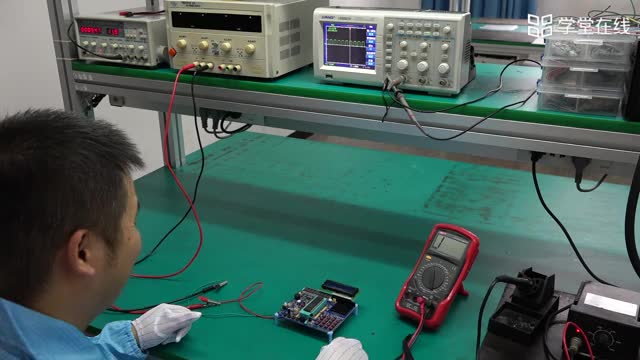
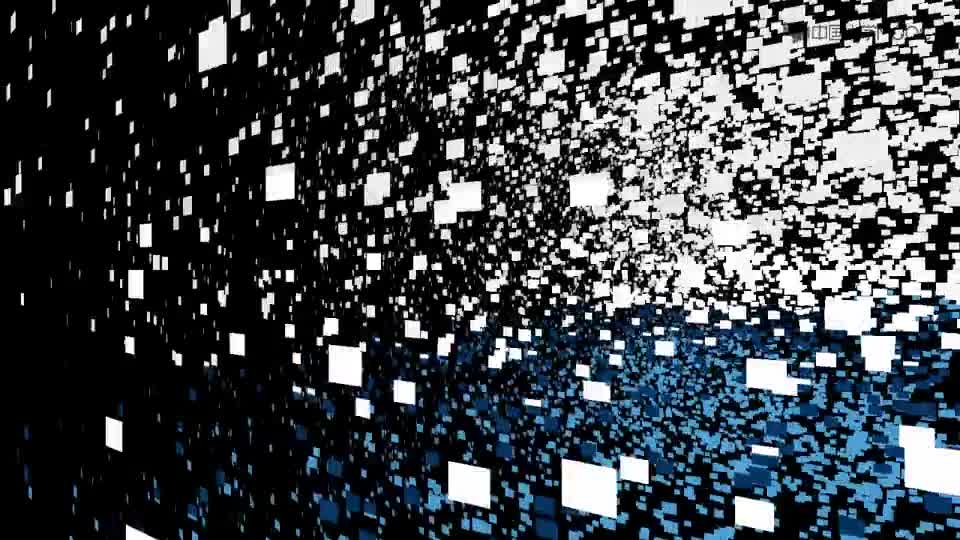
评论