引言
随着机械工业的发展和科研水平的不断提高,对机械传动产品的实验与检测手段不断提出了更高的要求。长期以来,我国的传动试验台的研制基本上还停留在传统的人工方式水平上,主要类型为以机械力或液压力的机械功率流封闭式试验台和用发电机作负载的电功率封闭试验台。这些试验台或由于节能或由于加载方面而各具特色,都存在一个共同的缺点,但自动化程度低,很难按事先设计的试验过程进行试验,无法模拟实际工况对各种机械传动产品的影响,因此试验结果与实际情况总难免有相当距离,这在很大程度上影响了试验数据对机械传动产品的设计、生产的直接指导作用。传动试验平台大多采用人工操纵方式,试验过程的监控及试验数据的采集和处理都较麻烦且准确性低,不易实现多参数自动控制和失效判定。
为了弥补以上不足,我们提出了一种新的方案—以一机械封闭式机械传动实验台为基础,由交流电动机驱动,采用交流变频调速系统实现无级调速,数字液压加载控制系统实现无级加载和载荷谱的模拟。控制系统采用面向对象程序设计技术和分层的设计思想,将多种控制算法和数据处理算法集成于一体,提供友好的人机交互界面,对计算机采集的数据进行可视化处理。
1.多功能试验台的组成及工作原理
根据试验台的功率传递原理和加载方法的不同,试验台可分为开放式功率流式、封闭功率流式和电功率流闭式三大类。机械封闭功率流式试验台(如图1),由于可用小功率原动机与低的功耗进行大的功率试验,具有不需要安置耗能装置,节能等优点,而运用很广泛。在封闭系统中,功率一端流出,又从另一端流人,形成循环封闭流,因此只要从外界输入不多的能量便可保持系统运转。电动机供给的能量,主要是补偿封闭系统中各零部件在运转时的摩擦功率损失,其值约为封闭功率值的10%~15%左右。
2 系统方案
试验台控制装置应能够在线实时控制转速、载负的变化,响应速度快,抗干扰能力强;数据的采集与处理应满足采样范围宽,能实现不同频率下的采样,自动处理分析数据,得出分析结果,操作界面方便,易于控制。
2.1 硬件方案
采用硬件的方法主要是采用专用集成电路和专门设计的硬件线路板来完成转矩转速信号的采集、转换、求平均值和放大、计数、滤波等。硬件线路复杂,仅电源就要提供正负24V、10V、5V等各种不同的稳压电源,结构复杂,可靠性低且功能单一,只能瞬时得到各种指标值,不能存储、显示和打印等。
2.2 软件方案
本系统建立在Windows2000平台上,用VC++语言编制而成。将变频器、电机、载器、加传感器、数据采集卡等抽象为类,设备模块化,对系统可针对试验台试件和设备的更换,对类进行扩充、修改、添加、组合,实现多种不同的实验,大大提高了试验台及其控制系统的适用性。
2.3设计方案
试验台以一台高档工业控制计算机作为核心,配以单片机系统,分别对电机调速系统和液压加载系统进行控制。工控机不但是控制器,同时还具有记录仪、示波仪、动态信号分析仪等功能,还能方便地根据不同实验的需要设置不同的转速、转矩、温度等报警参数和失效判定指标。其总体设计方案见图2。
3 计算机数据采集、测试及控制
3.1计算机数据采集、测试
在对CB2000卡式转矩仪和PCL-812PG多功能数据采集卡的参数进行配置后,性能参数测试是通过用JC2B转矩转速传感器(如图3所示)和配套CB2000卡式转矩仪,由计算机来完成数据采集、处理和控制任务。采用人机对话形式操作,根据不同的任务,可按标准的或非标准的试验方法进行试验,其试验结果均可实现以数字或曲线形式显示在屏幕上,或输出到打印机上,还可保存在数据库中。
3.2负载和转速控制
通过PC812-PG的模拟量输出口分别对变频器和数字阀发出电压信号,实现对转速和载荷的控制。
4 试验台的设计特色及用途
该设计方案将传统的机械传动实验台与新兴的计算机技术有机地结合起来,计算机实现对转速、载荷的数字控制,使转速和载荷反应灵敏,能够较好地模拟实际工况,实现对实验台转矩、转速信号准确、在线、实时、高速采集和处理。采用变频器可实现恒转矩调速和恒功率调速,省去以往用控制柜的不便。该试验台还具有很强的开发潜力,通过软件版本的不断升级和少量的硬件改进,可以使试验台的适用范围不断增加。
适用的机械传动装置有,圆柱齿轮减速箱、变速器、锥齿轮、汽车驱动桥,蜗杆减速器、行星齿轮减速器、链带传动、传动等装置。
下面是采集负载恒为M=130N?m,减数器输入端N=1000r/min的转速信号的1k数据(如图4和图5),进行傅立叶变换或小波变换(略),可对系统进行分析和故障诊断。图6为在不同转速、不同负载下传动效率曲线图,图中曲线由上至下的输入转速分别为600r/min、800r/min、1000r/min、1200r/min、1600r/min。
实验台转动时,要消耗电动机一部分功率,其只随传动轴转速的变化而变化。引起该功率损失的主要因素有传动件在转动时的摩擦、由于加工和装配误差而加大的摩擦以及搅油、空气阻力和其它动载荷等。随着转速的增加,由于功率损失增加,在相同负载下传动效率会有所降低。从图6可以看到,相同负载下,转速越高,效率越低,也表明实验台的测试结果与理论是相符合的。实验台是9级精度闭式圆柱齿轮传动,其传动效率的理论值应在96%左右,由于电机、加载器、传动器、轴承等的摩擦,油损失、搅装配误差以及测量值的误差,使得计算出的传动效率低于理论值。
结论
该新型多功能机械传动试验台以机械功率流封闭式机械传动试验台为基础,以计算机为核心,采用变频器和交流电动机作为调速系统,以液压泵站和加载器构成加载系统模拟实际工况,使用转矩转速传感器获取转矩和转速数据,与圆柱齿轮减速箱一起构成了功率流封闭的机械传动试验台。整个试验台以计算机作为控制与处理中心,该设计方案充分体现计算机资源和数字化技术的灵活运用。本文研制的试验台已成功地用于系统传动功率、机械产品承受载荷的测试。多次试验表明,该试验台与现有的其它同类试验台相比,自动化程度大大提高,模拟实际工况的能力明显增强。
-
变频器
+关注
关注
251文章
6542浏览量
144502 -
电机
+关注
关注
142文章
8996浏览量
145331 -
实验台
+关注
关注
0文章
6浏览量
6186
发布评论请先 登录
相关推荐
轮胎动态试验台在线测控系统的研制
步进电机扭矩测量试验台系统的设计
振动试验台的安装步骤
齿轮传动是机械传动中应用最广的一种传动形式
采用虚拟仪器技术的汽车转鼓实验台测控系统
气动实验台与气动与PLC实训装置
DB-PS01机械传动方案创意组合及参数分析
机电系统教学实验台
螺栓拧紧试验台的研制
PLC在水泵综合试验台控制系统中的应用
液压变压器恒压网络实验台的设计
多功能网络型传感器检测技术实验台
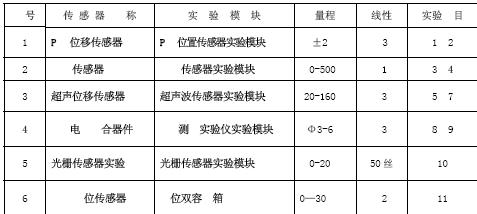
评论