控制系统的第一代产生于1930年到1940年,主要代表是以基地式仪表为代表的机械控制技术。第二代产生于1950年,主要是电气控制技术为主的继电器控制技术和调节器为代表的模拟控制技术。目前所称的控制系统是第三代控制系统,诞生于二十世纪七十年代,主要技术代表是用于流程工业的集散控制系统(DCS)和用于离散工业的可编程控制器(PLC)。 PLC和DCS是第三代控制系统的代表,在冶金、电力、石油、化工、轻工等工业过程控制中应用的很多,PLC和DCS功能相似,但其实使用领域有很大的差别,PLC使用在如绕线机、包装机等,而DCS则使用在航天、大型工业控制,最近几年DCS和PLC公司都转向共同称之为“混合型控制系”的领域,尝试着把DCS系统的强大功能、复杂性和PLC系统的灵活、开放性以及低价位结合起来。为此,DCS公司减少了其系统所占用的空间,而PLC公司则开始集成其组件以制造更完善的系统。
可编程控制器(Programmable Controller)是计算机家族中的一员,是为工业控制应用而设计制造的。早期的可编程控制器称作可编程逻辑控制器(Programmable Logic Controller),简称PLC,它主要用来代替继电器实现逻辑控制。随着技术的发展,这种装置的功能已经大大超过了逻辑控制的范围,因此,今天这种装置称作可编程控制器,简称PC。但是为了避免与个人计算机(Personal Computer)的简称混淆,所以将可编程控制器简称PLC,plc自1966年出现,美国,日本,德国的可编程控制器质量优良,功能强大。
PLC是一种专门为在工业环境下应用而设计的数字运算操作的电子装置。它采用可以编制程序的存储器,用来在其内部存储执行逻辑运算、顺序运算、计时、计数和算术运算等操作的指令,并能通过数字式或模拟式的输入和输出,控制各种类型的机械或生产过程。PLC已经广泛应用于钢铁、石油、化工、电力、建材、机械制造、汽车、轻纺、交通运输、环保及文化娱乐等各个行业,它具有高可靠性、抗干扰能力强、功能强大、灵活,易学易用、体积小,重量轻,价格便宜的特点。
PLC技术发展呈现新的动向:产品规模向大、小两个方向发展 大:I/O点数达14336点、32位为微处理器、多CPU并行工作、大容量存储器、扫描速度高速化。 小:由整体结构向小型模块化结构发展,增加了配置的灵活性,降低了成本。 2:PLC在闭环过程控制中应用日益广泛 3:不断加强通讯功能 4:。新器件和模块不断推出 高档的PLC除了主要采用CPU以提高处理速度外,还有带处理器的EPROM或RAM的智能I/O模块、高速计数模块、远程I/O模块等专用化模块。 5:编程工具丰富多样,功能不断提高,编程语言趋向标准化 有各种简单或复杂的编程器及编程软件,采用梯形图、功能图、语句表等编程语言,亦有高档的PLC指令系统 6:发展容错技术 采用热备用或并行工作、多数表决的工作方式。 7:追求软硬件的标准化。
但是,目前市场上的用户并不认为混合控制系统是一种革命性的新产品,也没有将它们看成一个完全不同的产品。而且,目前的国内市场上,既存在如上所述的混合控制系统,也有可通过装备回路控制板实现较多过程控制功能的PLC。但是,混合控制系统的概念切合了生产实际,是控制系统的发展趋势。从理论上讲,当代的DCS与PLC都是混合控制系统,但是作为一种产品,混合控制系统无疑为用户提供了一种新的选择。
随着无线技术进一步为公众所接收,其应用的范围也在日益扩大,尤其在工业过程领域,无线技术对习惯于有线技术的工业过程领域所带来的冲击是巨大的。到目前为止,大多数的无线项目用于开环回路的监测,应该说,现今的无线技术是对有线技术强有力的补充。由于无线技术的应用,解决了有线技术由于投资成本及环境限制未能实现的功能,提升了过程控制精度,为工厂管理带来极大效益。应该认识到,过程控制的无线化是一场静悄悄的革命,是一个逐步渗透的过程,随着人们认知程度的提高,以及无线技术更为可靠、连续、兼容的操作方式将给整个工业界以使用的信心,越来越多的无线设备将用于工厂。然而,安全有效的工厂操作总是放在第一位的,就目前来说控制功能的应用仍然是通过有线电缆来完成的。
DCS是分布式控制系统的英文缩写(Distributed Control System),在国内自控行业又称之为集散控制系统。即所谓的分布式控制系统,或在有些资料中称之为集散系统,是相对于集中式控制系统而言的一种新型计算机控制系统,它是在集中式控制系统的基础上发展、演变而来的。它是一个由过程控制级和过程监控级组成的以通信网络为纽带的多级计算机系统,综合了计算机,通信、显示和控制等4C技术,其基本思想是分散控制、集中操作、分级管理、配置灵活以及组态方便。
首先,DCS的骨架-系统网络,它是DCS的基础和核心。由于网络对于DCS整个系统的实时性、可靠性和扩充性,起着决定性的作用,因此各厂家都在这方面进行了精心的设计。对于DCS的系统网络来说,它必须满足实时性的要求,即在确定的时间限度内完成信息的传送。这里所说的“确定”的时间限度,是指在无论何种情况下,信息传送都能在这个时间限度内完成,而这个时间限度则是根据被控制过程的实时性要求确定的。因此,衡量系统网络性能的指标并不是网络的速率,即通常所说的每秒比特数(bps),而是系统网络的实时性,即能在多长的时间内确保所需信息的传输完成。系统网络还必须非常可靠,无论在任何情况下,网络通信都不能中断,因此多数厂家的DCS均采用双总线、环形或双重星形的网络拓扑结构。为了满足系统扩充性的要求,系统网络上可接入的最大节点数量应比实际使用的节点数量大若干倍。这样,一方面可以随时增加新的节点,另一方面也可以使系统网络运行于较轻的通信负荷状态,以确保系统的实时性和可靠性。在系统实际运行过程中,各个节点的上网和下网是随时可能发生的,特别是操作员站,这样,网络重构会经常进行,而这种操作绝对不能影响系统的正常运行,因此,系统网络应该具有很强在线网络重构功能。
其次,这是一种完全对现场I/O处理并实现直接数字控制(DDC)功能的网络节点。一般一套DCS中要设置现场I/O控制站,用以分担整个系统的I/O和控制功能。这样既可以避免由于一个站点失效造成整个系统的失效,提高系统可靠性,也可以使各站点分担数据采集和控制功能,有利于提高整个系统的性能。DCS的操作员站是处理一切与运行操作有关的人机界面(HMI-Human Machine Interface或operator interface)功能的网络节点。
工程师站是对DCS进行离线的配置、组态工作和在线的系统监督、控制、维护的网络节点,其主要功能是提供对DCS进行组态,配置工作的工具软件(即组态软件),并在DCS在线运行时实时地监视DCS网络上各个节点的运行情况,使系统工程师可以通过工程师站及时调整系统配置及一些系统参数的设定,使DCS随时处在最佳的工作状态之下。与集中式控制系统不同,所有的DCS都要求有系统组态功能,可以说,没有系统组态功能的系统就不能称其为DCS。
DCS自1975年问世以来,已经经历了二十多年的发展历程。在这二十多年中,DCS虽然在系统的体系结构上没有发生重大改变,但是经过不断的发展和完善,其功能和性能都得到了巨大的提高。总的来说,DCS正在向着更加开放,更加标准化,更加产品化的方向发展。
作为生产过程自动化领域的计算机控制系统,传统的DCS仅仅是一个狭义的概念。如果以为DCS只是生产过程的自动化系统,那就会引出错误的结论,因为现在的计算机控制系统的含义已被大大扩展了,它不仅包括过去DCS中所包含的各种内容,还向下深入到了现场的每台测量设备、执行机构,向上发展到了生产管理,企业经营的方方面面。传统意义上的DCS现在仅仅是指生产过程控制这一部分的自动化,而工控自动化系统的概念,则应定位到企业全面解决方案,即total solution 的层次。只有从这个角度上提出问题并解决问题,才能使计算机自动化真正起到其应有的作用。
当然不可忽视的还有电气仪表的发展,不论过程系统如何发展,功能如何强大,过程仪表的作用不能被忽视,仪表是在工业生产过程中,对工艺参数进行检测、显示、记录或者控制的基础。随着工业的发展,对仪表控制系统提出了更高的要求,电动仪表逐步向数字化、智能化方向发展,计算机系统向网络化、开放化发展,新一代的仪表主要特点是智能化和数字化。
工厂的生产好坏很大程度上依赖于过程仪表的状况,这些仪表除了流量、液位、压力及温度等参数的传感器和变送器,还包括分析仪及控制阀。用于过程技术的堡盟传感器和测量设备极其精密和稳定,完全能够满足应用要求。尤其是在极端环境条件下,它们也能进行准确的测量。良好的产品质量不仅延长了使用寿命,而且降低了维护周期,提高了过程生产的安全性和效率。
现在,自动化控制系统正在向第四代控制系统发展,第四代控制系统有两个趋势,一是系统的开放性,一是流程工业控制和离散控制的融合,体现在DCS和PLC功能的融合。目前,PC-BASED控制系统、嵌入式控制系统、现场总线控制系统都希望能成为第四代控制系统的主流系统,但是,由于这些系统都有各自的缺点,因此,大家普遍认为第四代控制系统还是会由以目前第三代控制系统的特点,加上开放和融合性的特点组成的柔性控制系统。第四代控制系统的发展依然是在摸索中,自动化专业的靴子必将担当起这个责任。
-
plc
+关注
关注
5021文章
13437浏览量
467024 -
可编程控制器
+关注
关注
6文章
538浏览量
39047 -
DCS
+关注
关注
20文章
616浏览量
50500
发布评论请先 登录
相关推荐
[原创]2010中国现代工业质量控制技术高峰论坛(7月,上海,免费)
现代工业电机驱动如何实现短路保护
现代工业制造中的精密测量技术简单介绍
中国制造2025”与英国“现代工业战略”的区别
英国“现代工业战略”与《中国制造2025》异同分析
工控机在现代工业中的关键作用
脉冲型电阻焊电源技术及其在现代工业焊接中的应用探索
高能点焊电源技术在现代工业制造中的应用与研究进展
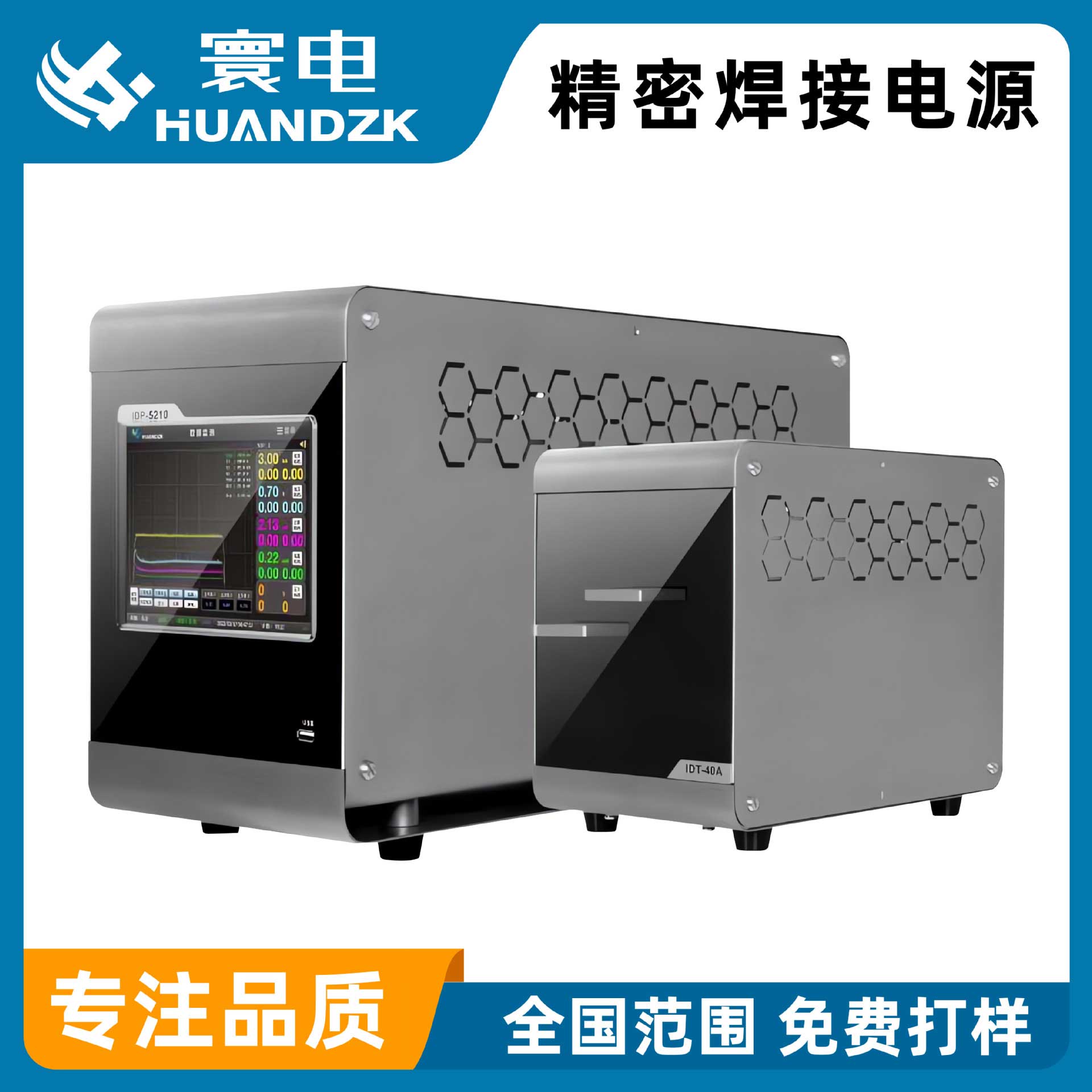
精密自动电焊电源技术在现代工业制造中的应用与探索
无线测温解决方案在现代工业中应用
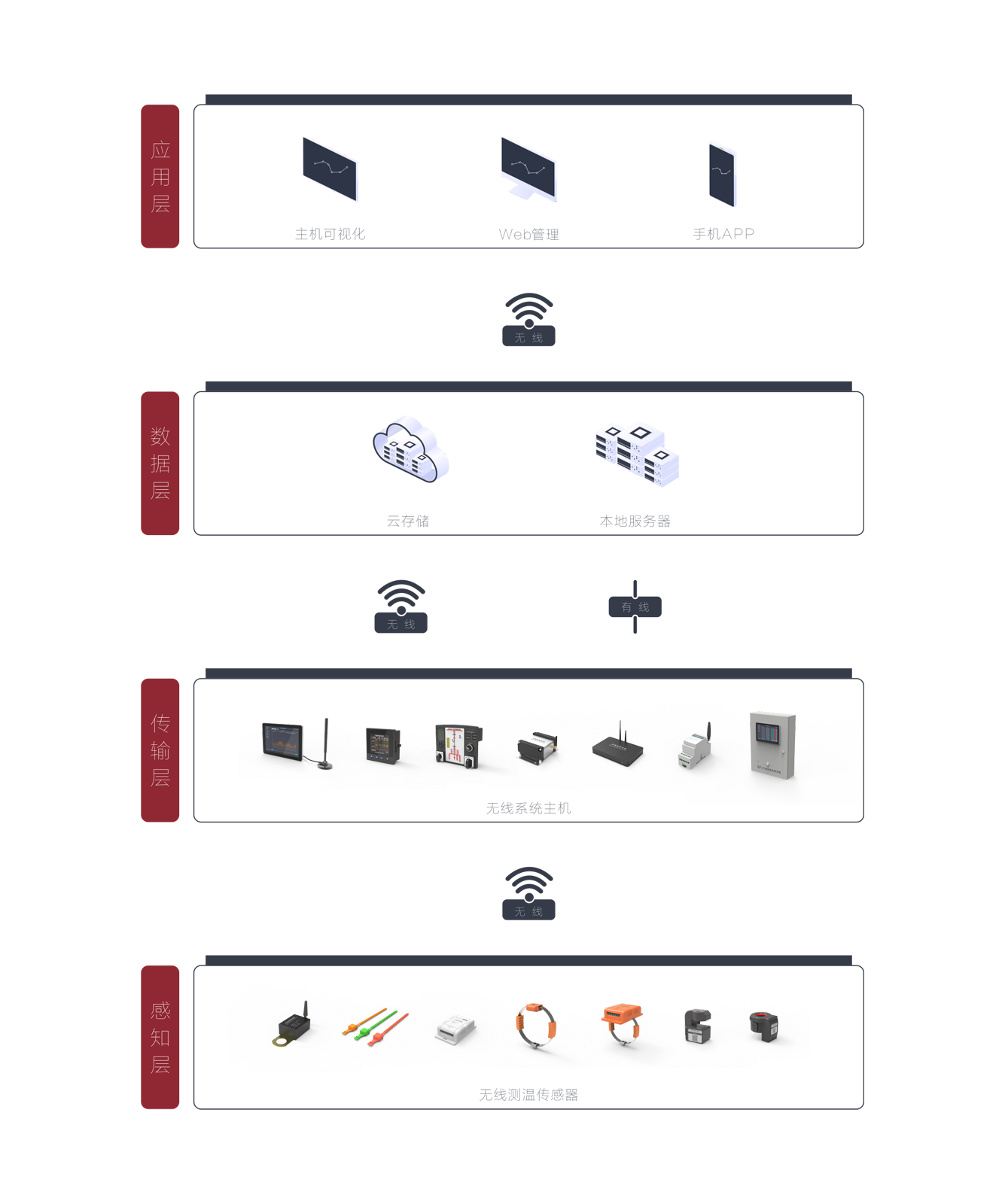
评论