一般而言,汽车动力系统采用集中供电的方式,通过多通道变压器将电池中的12 V的直流电进行转化,以为6个隔离式栅级驱动电路供电(图1)。
图1 集中式电力供应模块示意图
设计者在集中式变压器模型方面面临着许多挑战,包括布局过于复杂和产生电磁干扰(EMI)。此外,由于需要更多层来隔离信号/电源线,还会面临电路板占用空间较大和印刷电路板(PCB)成本较高等问题。
然而,有了博通有限公司推出的配备有集成反激式控制器的汽车级智能栅极驱动,例如ACPL-32JT和ACPL-33JT,通过一些独立的组件,以及一些放置在IC旁边的小型高效变压器就可以轻易搭建一个分布式电力供应系统(图2)。这可以减少总的占用空间,并可将绝缘栅双极晶体管(IGBT)通道之间电磁干扰(EMI)和噪声耦合降低到最低。
图2 分布式电力供应模块示意图
设计简单
由于采用分布式电力供应架构,设计人员在规划线路布局的时候更具有灵活性;低电压平面(low voltage plane)和高电压平面(high voltage plane)可以轻易地区分开来。此外,整个印刷电路板( PCB)布线变得更易于管理和更为便利。
图3 采用集中电力供应设计的6通道IGBT栅级驱动器板
图4 采用配有ACPL-32JT的分布式电力供应设计的6声道IGBT栅极驱动板
图3和4比较了基于集中式电力供应和基于分布式电力供应的的六通道IGBT栅极驱动板。很明显,分布式电力供应架构的印刷电路板布局更为简单,布线也更为有效。在低电压和高电压回路之间并没有PCB 走线(PCB trace)和电平(power plane),从而提高了信号的完整性,并避免对信号线造成不利的噪音干扰。
鲁棒性
分布式电力供应系统采用的变压器体积要比集中式变压器体积小14倍。图5显示了位于集中式变压器与单个变压器的大小比较。表1则列出了集中式变压器和单个变压器的实际尺寸大小。
图5 单个变压器与集中式变压器的大小比较
表1 单个变压器与集中式变压器的大小比较
与体积更为笨重、更为高大、且容易受到机械振动影响的集中变压器相比,为每个驱动配备的单个变压器可以提高可靠性和鲁棒性。集中式供电架构使用的电力供应电容器尺寸更大,封装在一个圆筒的 CAN 包里(in a radial CAN package),非常醒目並且占据空間。为此,设计师可为分布式电力供应系统选择尺寸更小的表面贴装器件封装(SMD package)电容器。这些电容器所需的额定电压要比传统的集中式电力供应回路至少低10V~20V。
节省成本
除了设计简单和拥有较好的鲁棒性之外,选择分布式电力供应系统的另一个好处就是可以通过整个电路板尺寸和印刷电路板分层的最小化来节省成本。分布式的驱动器系统和单个的变压器可让它们紧密地放置在一起,从而节省宝贵的电路板空间。图6展示的是一个精心设计的半桥栅极驱动器电路(顶部和底部通道),放置在一个39.7mm(宽) X 52mm(长)的区域,不到标准名片一半大小。在这种情况下,一个六通道栅极驱动电路需要的PCB面积只相当于1.5张标准名片的大小。
图6 半桥栅极驱动电路板可以按照半张标准名片的大小进行紧凑设计
分布式系统也有助于减少印刷电路板的层数,因为低电压线路/平面(low voltage traces/planes)和高电压线路/平面(high voltage traces/planes)之间并没有交叉。这就不需要为传导交叉信号而添加额外的层。图7显示了专为 Fuji M651 IGBT设计的紧凑型6通道栅极驱动板,使用了配备有ACPL-32JT的仅有四层的印刷电路板。
图7 采用分布式电力供应设计且仅使用了四层PCB的紧凑型六通道栅级驱动器
更好的EMI性能
在一个集中式电力系统当中,一个大型六通道变压器通常要比单个的小型变压器发出更多的 EMI 噪声。在分布式电源供应系统当中,每个智能栅极驱动光耦合器接通过一体化的DC / DC控制器驱动单个变压器,以为侧端供电驱动IGBT。
以下测量结果表明:和小型的单个变压器相比,集中式6通道变压器(图8)的 EMI噪音要高很多(图9)。
图8 集中式六通道变压器中的EMI测量
结论
和使用传统集中式电力供应架构的栅级驱动电路板相比,分布式电力供应系统可以简化汽车多通道IGBT栅极驱动器的设计,提高鲁棒性和EMI性能,并降低组件成本。
-
变压器
+关注
关注
160文章
7589浏览量
136946 -
pcb
+关注
关注
4333文章
23223浏览量
401854 -
控制器
+关注
关注
113文章
16562浏览量
180303 -
汽车电子
+关注
关注
3030文章
8068浏览量
168297
发布评论请先 登录
相关推荐
金属带式CVT与动力系统的优化匹配及液压系统控制
分布式能源系统当微型电网技术应用
汽车动力系统技术大盘点
汽车动力系统解决方案集锦
新能源汽车动力系统设计资料精华
汽车动力系统大盘点:助你设计绝佳方案
分布式电源分布式电源装置是指什么?有何特点
常见的分布式供电技术有哪些?
电力系统中通信网络的应用研究
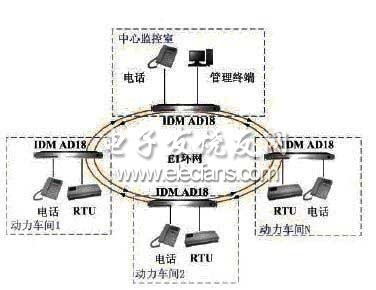
评论