前言
液压技术是一门相对发展较晚的技术,主要应用在反应快、动作准确的自动控制系统中。随着原子能、空间技术、计算机技术的发展,液压技术以渗透到各个工业领域中,并开始向高压、高速、大功率、高效率、低噪声、低能耗、经久耐用、高度集成化等方向发展。与此同时,电液控制系统控制策略也在不断发展。多年来,从传统的PID控制、自适应控制到变结构控制、鲁棒控制、智能控制等诸多新颖的控制手段中得到不断发展和完善。
目前,国外已经研制和生产了各种不同的标准组件,而中国作为未来工业机器人的主要生产国,标准化的过程是发展趋势。中国制造业面临着向高端转变,承接国际先进制造、参与国际分工的巨大挑战。加快工业机器人技术的研究开发与生产是中国抓住这个历史机遇的主要途径。因此我国工业机器人产业发展要进一步落实:第一,工业机器人技术是我国由制造大国向制造强国转变的主要手段和途径,政府要对国产工业机器人有更多的政策与经济支持,参考国外先进经验,加大技术投入与改造;第二,在国家的科技发展计划中,应该继续对智能机器人研究开发与应用给予大力支持,形成产品和自动化制造装备同步协调的新局面;第三,部分国产工业机器人质量已经与国外相当,企业采购工业机器人时不要盲目进口,应该综合评估,立足国产。智能化、仿生化是工业机器人的最高阶段,随着材料、控制等技术不断发展,实验室产品越来越多的产品化,逐步应用於各个场合。伴随移动互联网、物联网的发展,多传感器、分布式控制的精密型工业机器人将会越来越多,逐步渗透制造业的方方面面,并且由制造实施型向服务型转化。
随着大规模集成电路和微处理机技术的发展和应用。上述控制技术也发生了根本变化。在70年代出现了用软件手段来实现各种控制功能,以微处理器为核心的新兴工业控制器——可编程程序控制器(PLC)。这种期间完全能够适应恶劣的工业环境,由于它兼备了计算机控制和继电器-接触器控制两方面的优点,故目前世界各国将其作为一种标准化通用设备普遍应用于工业控制。
1.剪切机功能结构
本液压剪切机主要用于板料的剪切加工。其主机由送料机构4、料架5、压块1和剪刀2等组成。物料的压紧和剪切由液压缸驱动。各工作机构行程上布置有电气行程开关csoi~sos),用来发信并与PLC共同实现自动控制。
剪切机在初始位置时,压紧板料的压块1在上部位置,行程开关SQ2被顶开。剪刀2也在上面,行程开关SQ4被顶开。行程开关soi和SQ5均为常开。
剪切机进入工作状态前,物料放在送料带上,然后启动液压系统并升压到工作压力后,开动送料机构,向前输送物料,当物料送至规定的剪切长度时压下行程开关SQI发信,使送料机构停止,压块由液压缸带动下落,从而接通行程开关SQ2。当压块下落到压紧物料位置触动s03时,剪刀由另一液压缸带动下降,行程开关s04接通。剪刀切断物料后,物料下落,行程开关SQI复位断开。每落一块板料到料架上,sos接通一次,计一次数。与此同时,压块和剪刀分别回程复位,即完成一次自动工作循环。然后自动重复上述过程,实现剪切机的工作过程自动控制。
2.液压系统设计
2.1液压回路的选择
确定液压执行元件以后,根据设备的共组特点和工作要求确定对主要性能起决定性影响的主要回路,机械手液压系统主要有针对伸缩运动,升降运动和回转运动的三个主要运动回路。
2.2液压元件和液压回路综合
液压回路的综合就是把选择的液压回路放在一起,进行归并整理,增加必要的液压元件和辅助回路,确定完整的液压传动系统。同时注意:a.尽量简化系统机构,减少不必要的液压元件使用;b.保证整个液压系统运动动作的可靠,安全,没有元件与机构之间的相互干涉问题的存在;c.尽可能的去提高系统的工作效率,减少不必要的功耗的浪费;d.尽可能采用标准通用的液压元件。
2.3驱动设计要求
1)满足工业机械手动作顺序要求。动作顺序的各个动作均由电控系统发讯号控制相应的电磁铁,按程序依次步进动作而实现。
2)机械手伸缩臂安装在升降大臂上,前端安装夹持器,按控制系统的指令,完成工件的自动换位工作。伸缩要平稳灵活,动作快捷,定位准确,工作协调;
3)控制系统设计要满足伸缩臂动作逻辑要求,液压缸及其控制元件的选择要满足伸缩臂动力要求和运动时间要求。
本次设计采用液压传动的控制方式,相比其他传动方式有以下几点优点:
1)液压传动能在运行中实行无极调速,调速方便且调速范围比较大;
2)在同等功率条件下,液压传动装置的体积小,重量轻,惯性小,结构紧凑,而且能传递较大的力或转矩
3)液压传动工作比较平稳,反应快,冲击小,能高速启动、制动和换向。液压传动装置的换向,回转运动每分可达500次
4)液压传动装置的控制、调节比较简单,操纵比较方便、省力,易于实现自动化,与电气控制配合使用,能实现复杂的顺序动作和远程控制
5)液压传动装置易于实现过载保护,系统超负荷,油液经溢流阀回油箱。由于采用油液作工作介质,能自行润滑,所以寿命比较长
6)液压传动易于实现系列化、标准化、通用化,利于设计,制造和推广使用
7)液压传动易于实现回转、直线运动,且元件排列布置灵活
8)液压传动中,由于功率损失所产生的热量可由流动着的油带走,所以可避免在系统某些局部位置产生过度温升
3.PLC选型
选择合理PLC的型号,对于提高PLC控制系统的技术经济指标起着重要作用。选择机型的基本原则是在功能满足要求的前提下,保证可靠,维护使用方便以及最佳功能价格比。
(1)结构选择
PLC主要有整体式和模块式。
整体式PLC:整体式PLC的每一个点的平均价格比模块式的便宜,且体积相对小,一般用于系统工艺过程较为固定,环境条件较好,维修量较小的小型控制系统中。
模块式PLC:模块式PLC功能扩展灵活方便。在点数上,输入点数,输出点数的比例,模块的种类方面选择余地大,且维修方便,一般用于较复杂的控制系统。
对于组合机床,选用整体式PLC较好。
(2)I/O点选取原则
PLC平均的I/O点价格比较高,因此应该合理选用PLC的I/O点数量,在满足控制要求的前提下力争使用的I/O点最少,但必须留有一定余量。通常I/O点数是根据被控制对象的输入输出信号的实际需要,再加上10%-20%的余量来确定。
由PLC组成的四工位组合机床控制系统有输入信号42个,均为开关量。其中检测元件17个,按钮开关24个,选择开关1个。
电控制系统有输出信号27个,其中电磁阀16个,六台电动机的接触器和5个指示灯。根据I/O点数的选取原则考虑10%-20%的I/O点数余量输入点数可选取46-50个输出点数可选取29-33个。
(3)确定PLC机型及扩展模块。
根据(1)(2)及实际PLC机型点数,选用FX2N-64MR主机和一个16点的输入扩展模块(FX-16EX)这样共有输入点(32+16)。输出点就是主机的32。足够可以满足42个输入,27个输出的要求,而且留有一定余量。
1.1输入输出信号分配
输入输出信号地址表是将输入输出列成表,给出相应的地址和名称,以备软件编程和系统调试时使用的一种表。由本设计可知控制电路中的按钮,行程开关,检测元件等触点都属于PLC的输入设备,PLC的输出控制对象主要是控制电路中的执行元件,本设计主要是接触器,电磁阀,指示灯。根据电控系统的输入输出信号表知:
1输入元件数量
行程开关12个
按钮24个
选择开关1个
检测元件5个
2输出元件数量
电磁阀16个
接触器6个
指示灯5个
根据本设计选用的PLC机型,将输入输出元件分配到PLC的输入输出接口。
4.PLC控制系统软件设计
根据本设计的控制与工艺要求,按液压剪切机的动作顺序及每步所完成的任务,可得工作循环流程。
本液压剪切机的PLC控制设有手动和自动两种工作方式,调试时用手动方式,连续生产时用自动方式。当工作方式开关置于手动时,可通过操作台面板上相应的按钮开关运行某道工序;当工作方式开关设置为自动时,则由PLC软件支持实现自动工作循环并可对意外故障人工干预,紧急停机。
为了节省输入接点,以利根据需要拓展功能,将手动与自动同一操作的发信元件接到PLC的同一输入接点上。在自动工作方式时,通过手/自动转换开关S及软件控制的PLC内部辅助继电器,可使手动操作不起作用。
5.设计PLC控制系统状态转移图与梯形图程序
状态转移图,它是完整地描述控制系统的工作过程,功能和特性的一种图形,是分析和设计电路系统控制程序的重要工具。本设计的状态转移图按下列几步进行的
1按液压剪切机的控制要求与加工工艺画出状态转移图。
2在画出的状态转移图上以PLC输入点或其他元件定义状态转换条件。
3按照电控系统提供的电气执行元件功能表,在状态流程图上对每个状态和动作命令配画上实现该状态或动作命令的控制功能的电气执行元件,并以对应的PLC输出点的编号定义这些电气执行元件。
由状态转移图易的相应的梯形图程序,它们二者是一一对应关系,梯形图程序请见图1
图1PLC控制系统梯形图程序
6.结论
在实际的生产中,为了提高生产率,减少劳动强度,液压装置也就被广泛地用于工业生产中,它可以无疲劳地进行重复的动作。PLC作为新一代的工业控制装置,具有开发柔性好,接线简单,安装方便,抗干扰性强等特点,用它来控制四工位组合机床这样复杂的生产设备,是理想的选择。PLC的采用,降低了机床的故障率,节省了大量的维修费用,提高了整机的可靠性,保证了工件的精度要求
责任编辑:gt
-
控制器
+关注
关注
112文章
16396浏览量
178503 -
控制系统
+关注
关注
41文章
6633浏览量
110680 -
plc
+关注
关注
5013文章
13323浏览量
464009
发布评论请先 登录
相关推荐
PLC控制的自动剪切机系统
可编程序控制器产品详解
可编程序控制器的功能指令在电气系统中的应用技巧
对可编程序控制器控制系统的可靠性探讨
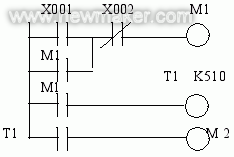
评论