马钢第三炼钢厂六机六流方坯连铸机采用高效连铸技术,其生产能力与转炉、LF—VD精炼炉生产相匹配,并可向下游的棒材、高线轧机提供高质量无缺陷铸坯。连铸机的在线设备,包括结晶器、结晶器液面检测与塞棒控制系统、结晶器电磁搅拌系统(含冷却水系统)和液压振动装置,均从奥地利的奥钢联(VAI)引进。
马钢第三炼钢厂高效方坯连铸机采用全弧型渐近矫直机型,连铸半径为8m,铸坯断面为140mm×140mm,定尺长度为16000mm,单炉浇注钢水量为65t,浇注时间为28min/炉,年产合格钢坯量70.93万吨,钢水收得率97%。
连铸机控制系统由基础自动化级和过程控制级组成,其中基础自动化级配备一套公用PLC、6套铸流PLC,分别对连铸机实施顺序和逻辑控制。控制系统采用了西门子S7-400系列PLC,下挂Profibus-DP网,并通过DP/PA链接器将总线仪控设备接入工业控制网络,真正实现了“集中管理,分散控制”的目的。同时,全数字化通信模式的抗干扰能力强、测量控制精确度高,借助数字双向传输的特点和先进的设备管理软件,可实现参数远程设定,采集丰富的仪表信息,有利设备故障诊断,改善管理状况。过程控制级由二级计算机构成,通过工业以太网与基础级的PLC相连,并依靠控制模型和数据库对一级控制系统实施指导、管理和跟踪。人机界面可显示运行图、棒图、趋势图、报警、设定等画面和图表,并进行系统的安全联锁和数据管理。
一 、系统组成
基础级采用7套S7-400 PLC作为连铸机的控制器,其CPU类型是416-2DP,并带有通信功能,可与扩展单元的IM-153、IM-157通信卡以及变频器通过Profibus-DP控制网相联,其中扩展单元采用ET-200M和链接器(DP/PA)作为子站。控制软件为STEP 7,并集成西门子过程设备管理软件PDM。控制级采用西门子工控机作为监控站,与PLC通过快速工业以太网(基于TCP/IP协议)连接,系统运行西门子公司基于Windows NT 4.0的WinCC软件。
1. 硬件构成
系统构成如附图所示(因篇幅限制,图中仅给出了公用系统的配置,铸流部分与之类似)。
图中PC1、PC2、PC3分别为上位机监控站;PLC0至PLC6分别为公用系统控制站和一至六流的主PLC;6个ET200为电控系统的远程站,分别为MCC站、结晶器振动液压站、拉矫液压站、出坯和火切站、两个主控站;大包回转变频器、中间包行走变频器、移钢机变频器、U/V冷床变频器均通过Profibus-DP接口挂在DP总线上。DP/PA链接器为S7-400 PLC的从站之一,同时又是现场总线仪控设备的PA主站,由网络部件耦合器实现所有Profibus-PA总线检测仪表与DP总线的链接,在传输更多检测、控制信息的同时亦可获取总线设备自诊断信息。
2. 软件配置
操作站软件为WinCC (5.0SP1版)软件,网络平台为Windows NT 4.0,WinCC自带数据库,并提供监控画面和PLC组态工具。S7组态软件为STEP7(5.1SP),内嵌西门子过程设备管理软件PDM。
二 、连铸机主要的控制系统
1. 钢水温度测量系统
经转炉炉外精炼处理后的合格钢水到达钢水接收跨,由起重机将钢包吊运到钢包回转台受包侧,回转180°过跨至浇注侧定位。然后由人工使用一次性快速S型热电偶测出钢水温度,并将温度信号同时传至PLC和大屏幕显示器。
工艺工程师根据钢水温度和所要浇注的钢种,通过HMI从二级系统历史数据库中调出相应钢种的浇注参数,并可根据需要进行参数调整。
2. 钢水称量系统
大包和中间包称重装置采用德国Schenck公司产品,其称重梁式传感器DWB具有安装、维护方便的优点,同时其内置的温度检测元件还可给系统提供称重传感器的实时工作温度。大包每侧回转臂和中间包均配置了4个传感器,测量信号经控制器DISOMAT-S处理后,通过控制器自带的Profibus-DP接口,将钢水重量信号由DP总线传输至PLC,PLC则以BCD码的形式将重量信号传输给大屏幕进行显示。称重控制器具有去皮、参数设定、校验等功能。
3. 结晶器液面自动检测及塞棒控制系统
结晶器液面采用全色137(Cs137)液面检测装置,与直流伺服电动机塞棒执行机构组成闭路自动控制系统,根据液面波动情况自动调节塞棒开口度,从而控制流入结晶器内的钢水量,稳定浇注操作。结晶器液压振动装置采用仿弧精确度高、维护量小、使用寿命长的全液压板簧导向振动器,其线性及非线性振动曲线、频率、振幅实时在线可调,以适应高拉速和高铸坯表面质量的要求。控制系统采用西门子C7 633DP的PLC,通过DP总线与主PLC通信。
4. 二冷水动态控制系统
a. 控制原理
连铸机二冷区是连铸坯冷却唯一可控制的区域,二冷区配水数学模型采用铸坯表面温度控制法实施冷却水量分布与动态控制,保证在任一浇注条件下,使冷却水量随拉速连续变化,且水量沿拉速方向按最佳状态分布,以控制铸坯表面温度符合目标温度。
当输入工艺及介质参数、各钢种的热物性参数及计算条件、设备及铸坯参数后,通过计算,可得到各段的水流密度、表面温度、凝固壳厚度、液相穴深度和水量参数。根据铸坯表面目标温度分布和数学模型计算,在其他因素确定的条件下,确定二冷区各段冷却水量Qi与铸坯拉速V的关系为:
Qi=aiV2+biV+Ci (i=1,…, 12)式中, ai、bi、ci——由钢种和铸坯断面尺寸等各项因素所确定的系数,i——冷却回路序号。
二冷配水数学模型设置在上位机里,根据钢种、断面尺寸等输入参数进行计算,经数学模型运算得到的各回路配水参数ai、bi、ci传送至PLC控制器,由PLC通过DP总线将各回路配水参数传至现场总线控制器进行配水的实时动态控制。
b. 过程现场总线配置
仪控系统全部通过Profibus-PA现场总线方式完成检测与控制。Profibus是国际现场总线标准IEC61158的8个子集之一,其通信模型为7层结构,协议包括3种规格:Profibus-FMS、Profibus-DP、Profibus-PA。其中Profibus-FMS属于系统总线,主要应用于车间级网络监控,物理结构为RS485,传输速率为9.6kb/s~12Mb/s。Profibus-DP属于设备总线,主要应用于复杂现场设备和分布式I/O,物理结构为RS-485,传输速率为9.6kb/s~12Mb/s。Profibus-PA也属于设备总线,主要应用于两线制供电和本安的过程控制仪表,传输速率为31.25kb/s,它在保持DP传输协议的同时,增加了对现场仪表的馈电功能,执行标准是IEC61158-2。
如附图所示,公用部分的结晶器进水总管的温度、压力、流量检测仪表,二冷水总管的压力、流量检测仪表,以及结晶器进水总管的流量控制阀,经过DP/PA 链接器与DP总线连接。虽然耦合器可以直接挂在DP总线上,但要占用一个DP地址,且无法扩充,而每个链接器可以扩充5个耦合器,并且在非防爆区每个耦合器最多可挂接30台非防爆现场总线仪表,所以在平衡经济性和系统可扩充性的前提下,铸流部分和公用部分均采用了一个链接器配一个耦合器的硬件配置模式。整个系统采用了Profibus-PA总线型拓扑结构,总共有7个链接器和7个耦合器,分别对应公用系统和六流铸机的每一流。在这种模式下,PA总线上的智能总线仪表的地址编号将不受DP地址编号的限制,可以在相应的耦合器下任意编址,有利于总线设备的扩充和维护。
5. 尾坯优化切割控制系统
二级计算机根据中间罐自动称量信号、定尺优化模型和尾坯优化切割模型,通过DP总线将控制参数下传到出坯和火切远程站,自动对尾坯进行优化切割操作,提高钢水收得率和成坯率。
三、 结束语
马钢第三炼钢厂六机六流高效方坯连铸机控制系统在实现“三电一体化”的基础上,成功地将Profibus总线技术应用于生产全过程,提高了系统的控制水平和可靠性,同时降低了运行成本。由于采用Profibus-PA总线,节省了仪控系统的相关硬件费用,如I/O模块、电源隔离器、控制柜、控制室方面的费用和施工布线的费用,与常规系统相比,仅仪控系统就比原概算节省30%的投资。另外,内嵌的过程设备管理软件PDM,减少了所需其他软件的种类,也降低了相关软件费用。尤为重要的是,由于现场总线仪表具有自诊断功能,因此,可以预先诊断和维护在线设备,提前排除故障,减少停机时间,提高了生产的安全性,同时大大降低了系统运行、维护费用,为整个高效连铸机的安全顺产提供了重要的技术保障。
责任编辑:gt
-
控制系统
+关注
关注
41文章
6639浏览量
110692 -
plc
+关注
关注
5013文章
13329浏览量
464097 -
总线
+关注
关注
10文章
2891浏览量
88176
发布评论请先 登录
相关推荐
基于S7-400的污水处理自动控制系统的设计方案
现场总线Profibus-PA 关键技术研究及产品开发
本安现场总线系统Profibus-PA及其应用
S7-400及PROFIBUS-DP网在电气控制中的应用Th
S7-400在发酵啤酒过程系统中的应用
基于S7-400 PLC的控制系统在污水处理中的应用
SIMATIC S7-400
基于Profibus-DP的PLC与PC现场总线控制系统
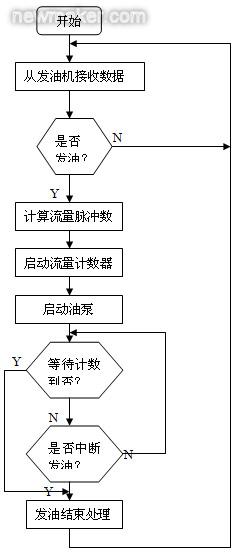
S7-400硬件安装及连接
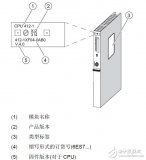
S7-400联网及寻址
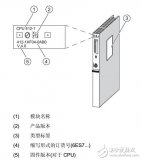
采用Profibus现场总线实现了PLC控制系统之间的通信
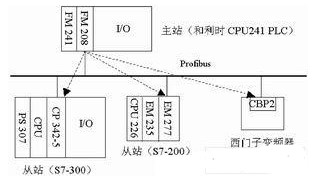
采用现场总线和PLC器件实现板坯连铸机电气自动控制系统的设计
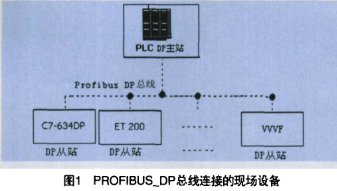
评论