1. 引言:
随着微电子技术、计算机技术、自动控制和精密测量技术的不断发展和迅速应用,在制 造业中,数控技术和数控机床不断更新换代,正向着高速度、多功能、智能化、开放型以及 高可靠性等方面迅速发展。数控机床的生产量和数控技术的应用已成为衡量一个国家工业化 程度和技术水平的重要标志。
开放式、网络化数控系统已成为当前数控技术发展的主要趋势。CAN 总线适用于数据 交换简短而频繁的场合,是解决工业控制设备之间数据通信的有效方式,可以方便有效地构 成分布式实时过程检测与控制系统。由于基于CAN 总线的数据通信具有高可靠性、实时性 和灵活性等特点,特别适合于工业现场自动化设备的互连,在汽车工业等领域得到了广泛的 应用。CAN 总线标准也是现场总线的国际标准之一(ISO11898)。
本文针对一个需要上位机与下位机进行现场通信的数字控制系统,根据数据量和通信速 率的要求,采用基于CAN 总线作为通信平台。整个系统能够在4ms 的控制周期内,完成对 7 个伺服轴和一个主轴的位置和速度控制,系统性能达到了预期的目标。
2. 数控机床的组成
数控机床一般由输入输出设备、CNC 装置(或称CNC 单元)、伺服单元、驱动装置(或 称执行机构)、可编程控制器PLC 及电气控制装置、辅助装置、机床本体及其测量装置组成。 图1 是数控机床组成框图,其中除机床本体之外的部分统称为计算机数控(CNC)系统。
开放式数控系统的关键技术是建立开放的数控体系结构,并确定开放式的标准。在结构上向趋于裁剪、扩展和升级的方向发展;形式上向可灵活组成不同档次、不同类型的方向进行迈进。
3. 系统设计
3.1 硬件平台设计
根据开放式数控系统的可裁减要求,数控系统最大控制能力为七轴五联动。具体的控制 量为:外接数字IO 数量不少于340 个,其中输入不少于200 个,输出不少于140 个,不少 于80 个继电器输出,并且有不少于40 个继电器输出指示灯。
本系统要求能够控制七个伺服轴和一个主轴,设置控制周期为 4ms,因此要在4ms 的 控制周期内完成对8 个轴的控制,其中每个轴的控制字为4 字节,再加上本系统设计时所使 用的外接数字IO 为360 个,则控制字需要360/8=45 个字节,因此通讯速度至少为(4*8+45) /0.004=19.25 Kb/s。在通信距离不超过40m 时,can 总线数据传输速率可高达1Mb/s,我们 系统设计所要求的最大传输距离为30m ,因此完全可以满足要求。为了增强通讯的可靠性, 使用双CAN 通信,其中第2 路can 总线作为系统的冗余。
如果把上位机(PC104+CAN 通信卡)和下位机(PC104+位控卡+IO 卡)插在一起或叠 在一起,会限制数控系统结构安装的灵活性。另外,如果上位机和下位机拥挤安置在操作盒 内,不利于散热;而且运动控制板卡也安装在操作盒内,接口线缆密集,不利于拆装。在此, 希望设计一种通讯结构能够使上位机和下位机分开安装,而且两者之间以较少的通讯线连接 进行长距离通讯,所以此处考虑到采用CAN 总线的串行通信方式。 图 2 为CAN 总线的开放式数控系统架构。
图中,上位机系统为思泰基公司的SB610(PC104)主板,外加2 路can 总线(用 SJA1000+82C250)构成,采取内存影射方式读写数据,经can 总线将数据传送给下位机。 上位机由于外接开关电源不便以及考虑干扰,电源需要从下位机引入24V 电源,经24/5V电源模块输出供电。
上位机的机箱根据整个系统的需求,采用外壳为散热片的铝壳机箱,前面面板有LCD 窗口,以及其他拨码开关等,控制面板镶嵌在前面板中。后面板有电源(24VDC)输入, usb 输入口、CAN 总线通讯口、键鼠接口、CRT 接口(调试需求)和网络接口(考虑升级 需求)、手摇脉冲接口等。
下位机系统是由母板、1 块CPU 板(PC104+2 路CAN 总线)、2 块位控卡、3 块IO 卡 构成。CPU 板、位控卡、IO 卡用双排96 针欧式插座(针)成直角插接在母板(孔)上。本系 统设计的输入点为216 个,输出点为144 个,满足系统I/O 要求。
3.2 CAN 通信链路设计
CAN 数据帧的标准格式如下:
其中,我们只需要设置仲裁段、控制段和数据段。仲裁段用来设置不同类型帧的优先级;控 制段由6个位构成,用来显示数据段使用的字节数;数据段可包含0~8个字节的数据。
CAN 通过“无损的逐位仲裁”方法来使有最高优先权的报文优先发送。在CAN 总线上 发送的每一条报文都具有唯一的一个29 位数字的ID。CAN 总线状态取决于二进制0 而不 是1,所以ID 号越小,则报文拥有越高的优先权。 本通信系统共设置 8 个优先级,CNC 系统与主轴之间交换的数据设置为最高优先级, 即将其数据帧的仲裁段设置为全0。CNC 系统与七个伺服轴之间交换的数据的优先级被分 别依次设置为优先级1~7。
本通信系统所传送的每一帧数据段只用了 8 字节其中的3 字节,后5 字节保留未用,其 中,第一字节表示当前数据帧的类型,接下来的2 个字节是本数据帧需要传输的数据。具体 设置如下:
(1)CNC 系统要向伺服驱动器发送的信息主要包括控制信号和位置/速度增量。 当数据类型为 0x01 时,对应的数据内容为对伺服驱动器的控制信号。该信号在下述3 种情况下发送:开机(或重启动)初始化完成时;当CNC 系统要改变对伺服驱动器的控制 时;发生报警时。
当数据类型为 0x02 时,对应的数据内容为实时控制伺服运动的位置/速度增量值,2 字 节16 位带符号数表示范围是±32767 个增量单位。本数据帧CNC 系统每个控制周期向伺服 驱动器发送一次。
(2)伺服驱动器需要向CNC 系统发送的数据信息主要包括状态信号和实际(编码器) 的位置/速度增量以及其他伺服数据。
当数据类型为 0x01 时,对应的数据内容为伺服状态信号。该信号在以下几种情况下发 送:当CNC 系统请求获得伺服状态信号而此时又没有位置回复帧时;当伺服驱动器出现报 警时;在CNC 位置广播后的位置回复帧中。
当数据类型为 0x02 时,对应的数据内容为伺服驱动器反馈的实际位置/速度增量值,2 字节16 位带符号数表示范围是±32767 个增量单位。本数据帧CNC 系统每个控制周期向伺 服驱动器发送一次。
4. 基于CAN 总线的数控系统的控制性能
通常,数控系统所工作的工业现场环境比较复杂,所以在实际应用中对CAN 总线数据 传输可靠性的要求比较高。在CAN 总线的实际应用中,时钟同步机制在提高系统可靠性方 面发挥着十分重要的作用。
表 1 总结了两种比较常用的有效的CAN 总线时钟同步方法的主要特点。如下,
通过比较这两种同步方法的各项性能指标,本文采用的同步方法为OCS-CAN (orthogonal clock subsystem for CAN)。特别的,该时钟同步方法在容错性方面有许多优点, 容错性的提高将大大提高系统数据传输的可靠性。
该方法在容错性方面主要基于以下三点: 首先,限制各节点的错误语义转化为突发错误语义。这点是可以做到的,例如,采用[3] 中提到的重复比较方法。第二,采用主站冗余机制。OCS-CAN定义了大量的备用主站,可 以随时替换出错的主站。
第三,进行模块检测[4]来正式核实容错机制的正确性。该正式核 实考虑到大量的错误模型,包括可能出现的信息矛盾。 试验证明,该方法不仅可以提高系统数据传输的精度和可靠性,而且可以将成本控制在 一个合理的水平,是一种经济有效的CAN 时钟同步方法。
5.结论:
基于 CAN 总线的数控机床网络解决了局域网型数控机床的缺点,结构简单、实时性好、 可靠性高、通信距离长、连接设备多。
本文的设计结果表明,对一个控制量多、实时性要求 严格的数字控制系统,基于CAN 总线的通信完全能够满足要求。 本文作者创新点:利用CAN 总线构成了一个全闭环的开放式数控系统,并且本数控系 统的最大控制能力为能够控制七个伺服轴和一个主轴。
-
CAN总线
+关注
关注
145文章
1942浏览量
130717 -
计算机
+关注
关注
19文章
7486浏览量
87844 -
数控机床
+关注
关注
19文章
779浏览量
46351 -
自动控制
+关注
关注
10文章
714浏览量
44152
发布评论请先 登录
相关推荐
基于RBAC的数控机床信息集成系统
关于数控机床一体机在数控机床上的应用分析
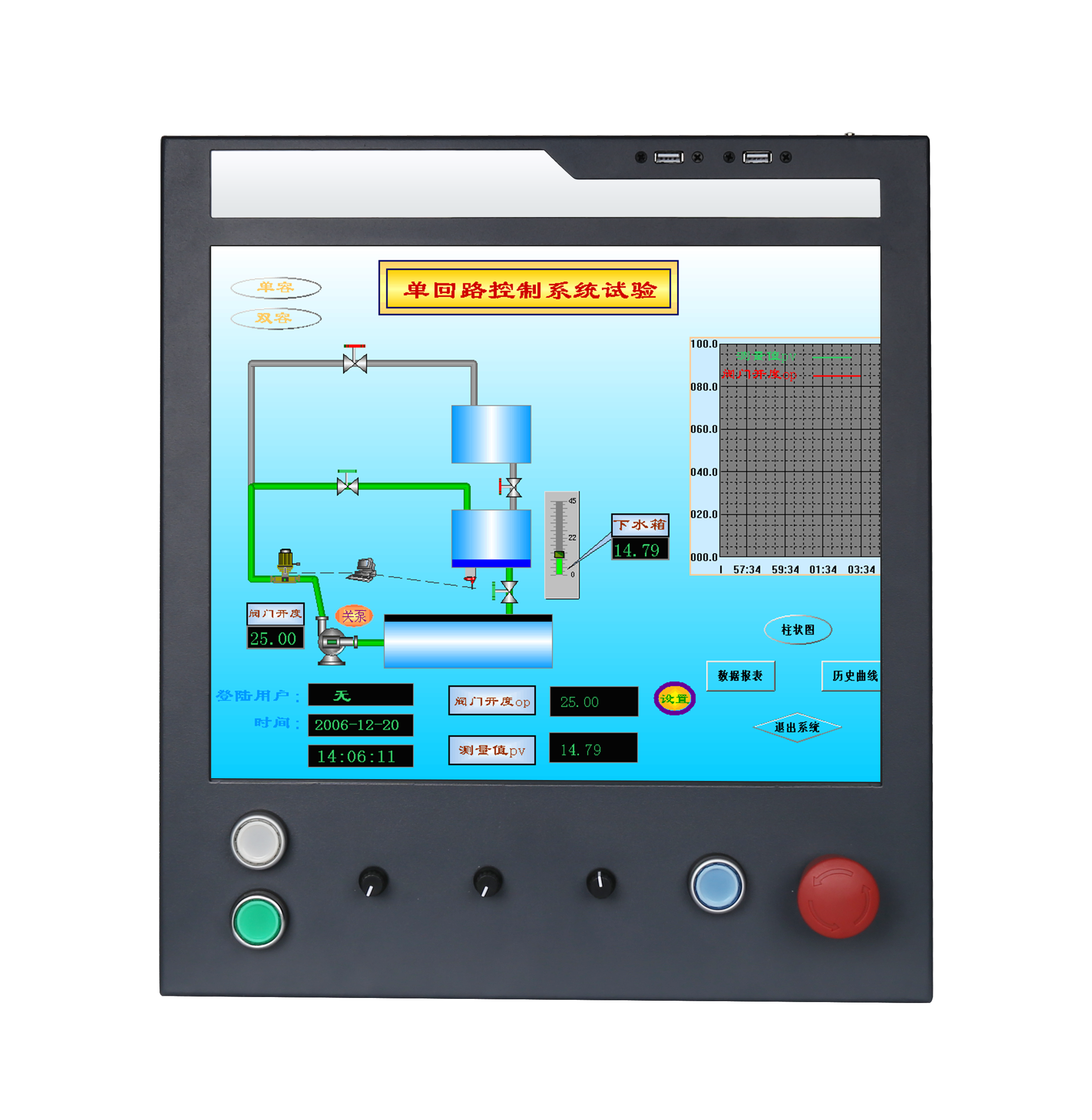
评论