摘 要
三菱电机开发了首款6.5kV全SiC(Silicon Carbide)功率模块,采用高绝缘耐压HV100标准封装(100mmÍ140mm)。通过电磁仿真和电路仿真,优化了HV100封装的内部设计,并通过实际试验验证了稳定的电气特性。6.5kV HV100全SiC功率模块为了提高功率密度,将SiC SBD(SchottkyBarrierDiode)与SiC MOSFET芯片集成在一起。
在续流时,集成的SiC SBD会导通,而SiC MOSFET的寄生体二极管不会导通,所以避免了双极性退化效应发生。本文对比了Si IGBT功率模块(Si IGBT芯片和Si二极管芯片)、传统全SiC MOSFET功率模块(SiC MOSFET芯片,无外置SBD)和新型全SiC MOSFET功率模块(SiC MOSFET和SiC SBD集成在同一个芯片上),结果表明新型全SiC MOSFET功率模块在高温、高频工况下优势明显。
1、引 言
SiC材料具有优异的物理性能,由此研发的SiC功率模块可以增强变流器的性能[1-2]。相对Si芯片,全SiC芯片可以用更小的体积实现更高耐压、更低损耗,给牵引变流系统和电力传输系统的研发设计带来更多便利。3.3kV全SiC功率模块已经在牵引变流器中得到应用,有着显著的节能、减小变流器体积和重量等作用[3-4]。6.5kV Si IGBT模块已经用于高铁和电力传输系统,这些市场期待6.5kV SiC功率模块能带来更多好处。基于此,三菱电机开发了6.5kV全SiC MOSFET功率模块[5-7],其采用HV100标准封装[8],如图1所示。这个封装为方便并联应用而设计,电气稳定性显得尤为重要。
本文介绍了6.5kV新型全SiC MOSFET功率模块的内部结构和电气特性,相对于传统的Si IGBT模块、传统全SiC MOSFET功率模块,新型全SiC MOSFET功率模块在静态特性、动态特性和损耗方面优势明显。
2、6.5kV新型SiC MOSFET功率模块特性
2.1 集成SiC SBD的SiC-MOSFET芯片特性
HV100封装6.5kV新型全SiC MOSFET功率模块采用SiC MOSFET和SiC SBD一体化芯片技术,最高工作结温可达175℃。
模块设计中的一个重要难点是避免SiC MOSFET的寄生体二极管(PIN二极管)导通,一旦PIN二极管中有少子(空穴)电流流向二极管的阴极(SiC MOSFET的漏极),因为SiC芯片外延层特性,双极性退化效应发生的可能性就会增加。在续流状态下,SiC SBD的正向饱和压降在全电流范围内比SiC MOSFET的寄生体二极管要低。
独立放置的SiC MOSFET 和SiC SBD芯片如图2(a)所示,SiC SBD的面积是SiC MOSFET芯片面积的3倍;如果将SiC SBD集成在SiC MOSFET芯片上面,如图2(b)所示,总面积是单个SiC MOSFET芯片面积的1.05倍。集成在SiC MOSFET芯片上面的SiC SBD采用垂直元胞结构,在续流时承载全部反向电流,同时使SiC MOSFET芯片的寄生体二极管不流过电流,从而消除双极性退化效应。如图2所示,由于芯片面积减小,模块整体体积就可以减小。相对于传统的Si IGBT模块和传统全SiC MOSFET功率模块,采用相同HV100封装的新型全SiC MOSFET功率模块可以实现业界最高的功率密度。
2.2 新型SiC MOSFET功率模块的优化设计
6.5kV新型全SiC MOSFET功率模块内部采用半桥拓扑,一般的大功率应用可以采用并联连接来提高输出功率。高电压功率模块在高频下运行,需要考虑模块自身的寄生电容、寄生电感和寄生阻抗等。3D电磁仿真是验证内部封装结构和芯片布局的一种有效方法。电磁干扰可能带来三种不良的影响:一是开关过程中的电流反馈;二是上、下桥臂开关特性不一致;三是栅极电压振荡。电磁干扰会增加模块内部功率芯片布置、绑定线连接及其他电气结构设计的复杂性。
我们构建了6.5kV新型全SiC MOSFET功率模块的内部等效电路和芯片模型,通过3D电磁仿真和电路仿真,验证了功率模块设计的合理性。
2.2.1
优化开关速度
如果在模块封装设计时没有考虑电磁干扰,在实际工况中,就会产生开关过程中的电流反馈,使芯片的固有开关速度发生变化,进而可能造成上桥臂和下桥臂的开关速度不一致。负的电流反馈可以降低芯片的开关速度,导致芯片的开关损耗增加,因此开关速度的不平衡可以导致模块内部各个芯片的热分布不一致。图3显示了6.5kV新型全SiC MOSFET功率模块在有电磁干扰和无电磁干扰下的仿真开通波形,从图中可以看出,通过优化内部电气设计,电磁干扰对6.5kV新型全SiC MOSFET功率模块没有影响。图4为6.5kV新型全SiC MOSFET功率模块上桥臂和下桥臂的仿真开通波形,两者的波形几乎完全一样,在实际测试时也验证了这一点。
2.2.2
栅极电压振荡抑制
在高电流密度功率模块中,内部有很多功率芯片并联,寄生电容和寄生电感可能组成复杂的谐振电路,从而可能造成栅极电压振荡。栅极电压振荡幅度过大,可能损坏栅极。通常可以增大芯片内部的门极电阻来达到抑制振荡的目的,但是增大内部门极电阻会造成开关损耗增加,在设计模块时,我们希望内部栅极电阻尽可能小。借助仿真手段,在保持小的栅极电阻的情况下,我们通过优化内部电气布局很好地抑制了栅极电压振荡。
图5为6.5kV新型全SiC MOSFET功率模块在优化内部设计之前和优化之后的栅极电压仿真波形。优化之前,有一个比较大的振荡,振幅可达13V。优化之后,栅极电压振荡得到抑制,幅度只有2V,在实际测试中也验证了这一点。
2.3 静态特性参数对比
图6为400A IGBT模块(从额定电流1000A IGBT转换而来)、400A传统全SiC MOSFET功率模块(不含SiC SBD)和400A新型全SiCMOSFET功率模块通态压降对比。在150℃时,SiIGBT的通态电阻比较低,这是因为Si IGBT是双极性器件,而SiC MOSFET属于单极性器件。400A传统全SiC MOSFET功率模块(不含SiC SBD)和400A新型全SiCMOSFET功率模块芯片面积几乎相同,所以在全温度范围内其通态电阻也几乎相同。
二极管正向压降对比如图7和图8所示。图7是各模块件在非同步整流状态(MOSFET不导通)下二极管电流特性的对比,图8为各模块在同步整流状态(MOSFET导通)下二极管电流特性的对比。从图中可以看出,在非同步整流状态下,传统SiC-MOSFET功率模块的表现呈非线性特性;而新型全SiC MOSFET功率模块,无论在同步整流还是非同步整流时,都呈线性特征。由上,无论在MOSFET导通状态,还是在二极管导通状态,全SiC MOSFET功率模块都表现出单极性器件的特性。
2.4 动态特性参数对比
图9为新型全SiC MOSFET功率模块在3600V/400A 在室温和高温下(175℃)的开通波形对比,从图中可以看出,经过内部结构优化的新型全SiC MOSFET功率模块上桥臂和下桥臂在室温和高温下的开关速度几乎完全一样,所以其室温和高温下的损耗也几乎一样。一般来说,随着温度的增加(载流子寿命增加),反向恢复电流也会随之增加,但是如图9所示,高温下的反向恢复电荷(Qrr)相对常温增加很少。与静态特性一样,新型全SiC MOSFET功率模块在动态特性上表现出单极性器件的特性。
2.5 实测开关波形和开关损耗对比
图10为传统全SiC MOSFET功率模块和新型全SiC MOSFET功率模块的开通波形在室温和175℃下对比,从图中可以看出在室温下,两者波形很接近,但是在175℃下,传统全SiCMOSFET功率模块反向恢复电流更大,VDS下降速度更慢。而新型全SiC MOSFET功率模块因为反向恢复电流小,所以其VDS下降速度更快。同时这些特性表明两者的开通损耗和反向恢复损耗在室温下非常接近,但是在高温下,新型全SiC MOSFET功率模块的开通损耗和反向恢复损耗相对更小,主要原因是反向恢复时,新型全SiCMOSFET功率模块的寄生体二极管不导通。
在175℃时,传统全SiC MOSFET功率模块在开通时会有一个比较大的振荡,而振荡可能造成电磁干扰,进而影响模块的安全工作。实际应用中,希望这个振荡越小越好,为了抑制振荡,可以减缓模块开关速度或者增加外部吸收电路。但是对于新型全SiC MOSFET功率模块,在高温下振荡非常小,无需采取额外措施来抑制振荡。
在高压全SiC MOSFET功率模块中,造成以上差异的主要原因是传统全SiC MOSFET功率模块有一层厚的外延层,在反向恢复时会产生比较大的反向恢复电流。
图11为Si IGBT模块、传统全SiC MOSFET功率模块和新型全SiC MOSFET功率模块的开关损耗对比(Si IGBT模块与全SiCMOSFET功率模块分别设置在最佳开关速度)。从图中可以看出,全SiC MOSFET功率模块损耗明显小于Si IGBT模块。并且,在175℃时,新型全SiC MOSFET功率模块比传统全SiC MOSFET功率模块开通损耗低18%,反向恢复损耗低80%。
3、损耗对比
在开关频率fs=0.5kHz、2kHz和10kHz,PF=0.8,调制比M=1,母线电压VCC=3600V,输出电流IO=200A的工况下,对比了采用Si IGBT模块(150℃)、传统全SiC MOSFET功率模块(175℃)和新型全SiC MOSFET功率模块(175℃)的逆变器损耗,如图12所示。从图中可以看出,在fs=0.5kHz,通态损耗占很大比例,此时全SiC MOSFET功率模块比Si IGBT模块低64%,同时传统全SiC MOSFET功率模块和新型全SiC MOSFET功率模块相差很小。
在fs=2kHz,全SiC MOSFET功率模块比Si IGBT模块低85%,而新型全SiC MOSFET功率模块相对传统全SiCMOSFET功率模块低7%。在fs=10kHz,开关损耗占据很大比例,此时全SiC MOSFET功率模块比Si IGBT功率模块低92%,而新型全SiC MOSFET功率模块相对传统全SiCMOSFET功率模块低16%。从以上可以看出,新型全SiCMOSFET功率模块更适合高频、高温应用。
4、结 论
三菱电机开发了业界首款采用HV100封装的新型6.5kV全SiC MOSFET功率模块。通过电磁仿真、电路仿真和实际测试,确认了内部电气设计的合理性。同时,新型6.5kV全SiC MOSFET功率模块采用SiC SBD和SiC MOSFET一体化芯片设计,减小了模块体积,实现了6.5kV业界最高的功率密度。通过静态测试和动态测试,确认了新型6.5kV全SiC MOSFET功率模块无论在SiC MOSFET导通还是SiC SBD导通时都表现出单极性器件的特性,且其SiC SBD在高温下反向恢复电流小,没有双极性退化效应。新型6.5kV全SiC MOSFET功率模块在高温下导通时VDS下降更快,其导通损耗更小,且没有振荡现象发生。
同时,对比了Si IGBT模块、传统全SiC MOSFET功率模块和新型全SiC MOSFET功率模块的损耗,在开关频率为10kHz时,新型全SiCMOSFET功率模块的损耗比Si IGBT模块大概低92%,比传统全SiC MOSFET功率模块相对低16%。相对传统全SiC MOSFET功率模块,由于SiC MOSFET体二极管与集成的SiC SBD之间反向恢复特性的不同,新型全SiC MOSFET功率模块在高温、高频等应用工况下更有优势。
-
MOSFET
+关注
关注
147文章
7158浏览量
213153 -
三菱电机
+关注
关注
0文章
177浏览量
20641 -
SiC
+关注
关注
29文章
2806浏览量
62608
原文标题:【论文】集成SiC SBD的6.5kV全SiC MOSFET功率模块
文章出处:【微信号:GCME-SCD,微信公众号:GCME-SCD】欢迎添加关注!文章转载请注明出处。
发布评论请先 登录
相关推荐
三菱电机成功开发基于新型结构的SiC-MOSFET
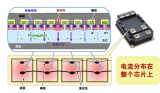
评论