本文主要是关于转动机械滚动轴承的相关介绍,并着重对转动机械滚动轴承发热原因进行了详尽的阐述。
滚动轴承
滚动轴承(rollingbearing)是将运转的轴与轴座之间的滑动摩擦变为滚动摩擦,从而减少摩擦损失的一种精密的机械元件。滚动轴承一般由内圈、外圈、滚动体和保持架四部分组成,内圈的作用是与轴相配合并与轴一起旋转;外圈作用是与轴承座相配合,起支撑作用;滚动体是借助于保持架均匀的将滚动体分布在内圈和外圈之间,其形状大小和数量直接影响着滚动轴承的使用性能和寿命;保持架能使滚动体均匀分布, 引导滚动体旋转起润滑作用。
作用
支承转动的轴及轴上零件,并保持轴的正常工作位置和旋转精度,滚动轴承使用维护方便,工作可靠,起动性能好,在中等速度下承载能力较高。与滑动轴承比较,滚动轴承的径向尺寸较大,减振能力较差,高速时寿命低,声响较大。
结构
滚动轴承的结构由部分组成
1.外圈——装在轴承座孔内,一般不转动
2.内圈——装在轴颈上,随轴转动
3.滚动体——滚动轴承的核心元件
4.保持架——将滚动体均匀隔开,避免摩擦
润滑剂也被认为是滚动轴承第五大件,它主要起润滑、冷却、清洗等作用
滚动轴承特征
1.专业化
轴承零件加工中,大量采用轴承专用设备。如钢球加工采用磨球机、研磨机等设备。专业化的特点还体现在轴承零件的生产上,如专业生产钢球的钢球公司、专业生产微型轴承的微型轴承厂等。
2. 先进性
由于轴承生产的大批量规模要求,使得其使用先进的机床、工装和工艺成为可能。如数控机床、三爪浮动卡盘及保护气氛热处理等。
3.自动化
轴承生产的专业化为其生产自动化提供了条件。在生产中大量采用全自动、半自动化专用和非专用机床,且生产自动线逐步推广应用。如热处理自动线及装配自动线等。
基本特点
好处
(1)。节能显著。由于滚动轴承自身运动的特点,使其摩擦力远远小于滑动轴承,可减少消耗在摩擦阻力的功耗,因此节能效果显著。从理论分析及生产实践中,主轴承采用滚动轴承的一般小型球磨机节电达30%~35%,中型球磨机节电达15%~20%,大型球磨机节电可达10%~20%。由于球磨机本身是生产中的耗能大户,这将意味着可节约一笔及其可观的费用。
(2)。维修方便,质量可靠。采用滚动轴承可以省去巴氏合金材料的熔炼、浇铸及刮瓦等一系列复杂其技术要求甚高的维修工艺过程以及供油、供水冷却系统,因此维修量大大减少。而且滚动轴承由于是由专业生产厂家制造,质量往往得到保证。也给球磨机使用厂家带来了方便。
优点
1、摩擦阻力小,功率消耗小,机械效率高,易起动;
2、尺寸标准化,具有互换性,便于安装拆卸,维修方便;
3、结构紧凑,重量轻,轴向尺寸更为缩小;
4、精度高,负载大,磨损小,使用寿命长;
5、部分轴承具有自动调心的性能;
6、适用于大批量生产,质量稳定可靠,生产效率高;
7、传动摩擦力矩比流体动压轴承低得多,因此摩擦温升与功耗较低;
8、起动摩擦力矩仅略高于转动摩擦力矩;
9、轴承变形对载荷变化的敏感性小于流体动压轴承;
10、只需要少量的润滑剂便能正常运行,运行时能够长时间提供润滑剂;
11、轴向尺寸小于传统流体动压轴承;
12、可以同时承受径向和推力组合载荷;
13、在很大的载荷-速度范围内,独特的设计可以获得优良的性能;
14、轴承性能对载荷、速度和运行速度的波动相对不敏感。
缺点
1、噪音大。
2、轴承座的结构比较复杂。
3、成本较高。
4、即使轴承润滑良好,安装正确,防尘防潮严密,运转正常,它们最终也会因为滚动接触表面的疲劳而失效。
性能
调心性能
轴中心线相对轴承座孔中心线倾斜时,轴承仍能正常工作的能力。双列向心球面球轴承和双列向心球面滚子轴承具有良好的调心性能。滚子轴承和滚针轴承不允许内、外圈轴线有相对倾斜。各类滚动轴承允许的倾斜角不同,如单列向心球轴承为8′~16′,双列向心球面球轴承为2°~3°,圆锥滚子轴承≤2′。
极限转速 在一定载荷和润滑条件下轴承所允许的最高转速。极限转速与轴承类型、 尺寸、精度、 游隙、保持架、负荷和冷却条件等有关。轴承工作转速应低于极限转速。选用高精度轴承、 改善保持架结构和材料、采用油雾润滑、改善冷却条件等,都可以提高极限转速。
轴承润滑
主要有脂润滑和油润滑。采用脂润滑不易泄漏、易于密封、使用时间长、维护简便且油膜强度高,但摩擦力矩比油润滑大,不宜用于高速。轴承中脂的装填量不应超过轴承空间的1/2~1/3,否则会由于搅拌润滑剂过多而使轴承过热。油润滑冷却效果好,但密封和供油装置较复杂。油的粘度一般为 0.12~0.2厘米/秒。负荷大,工作温度高时宜选用粘度高的油,转速高时选用粘度低的油。润滑方式有油浴润滑、滴油润滑、油雾润滑、喷油润滑和压力供油润滑等。油浴润滑时,油面应不高于最下方的滚动体中心。若按弹性流体动压润滑理论设计轴承和选择润滑剂粘度,则接触表面将被油膜隔开。这时,在稳定载荷作用下,轴承寿命可提高很多倍。
现代机器、仪器等设备正向高速、重载、精密、轻巧等方面发展,这对滚动轴承提出许多新的要求,如在减小尺寸的同时要求轴承保持甚至提高额定负荷,采用新技术改进工艺,提高制造精度,降低成本。通用滚动轴承已很难满足各式各样的要求,对生产量大的机器设备应设计制造专用轴承,在加强标准化的同时,增加品种,扩大专用轴承的比例。现代工业的发展还需要在特殊工况下工作的特种轴承,如在高速、高温、低温、强磁场或在酸、碱等介质中工作的轴承。
转动机械滚动轴承发热原因
(1)原因:轴承精度低
方法:选用规定精度等级的轴承。
(2)原因:主轴弯曲或箱体孔不同心
方法:修复主轴或箱体。
(3)原因:皮带过紧
方法:调整皮带使松紧适当。
(4)原因:润滑不良
方法:选用规定牌号的润滑材料并适当清洁。
(5)原因:装配质量低
方法:提高装配质量。
(6)原因:轴承内外壳跑圈
方法:更换轴承及相关磨损部件。
(7)轴向力太大
方法:清洗、调正密封口环间隙要求0.2~0.3mm之间,更正叶轮平衡孔直径及校验静平衡值。
(8)轴承损坏
方法:更换轴承。
转动设备常见故障的诊断方法
转动设备运转好坏,对安全生产有着重要的影响。转动设备运行状况差可能引起工艺参数变化,影响产品质量及产量,严重时还可能酿成事故。因为由机械振动引起的设备损坏率很高,而振动信号中含有丰富的机械状态信息量,很多机器设计是否合理、零部件是否存在缺陷、材质好坏、制造和安装质量是否符合要求、运行操作是否正常等诸多原因产生的故障,都能从振动状态信息中反映出来68,而且振动信号易于拾取,于是运用振动监测来解决转动设备的振动问题,便成为改善设备运行状况的有效途径之一。
振动就是机械系统随着时间在其平衡位置附近作微小的往复运动。振动监测就是在不停机的情况下,采集设备振动信号,判断设备运行是否正常,如异常,则分析诊断异常的原因、部位、严重程度,并提出针对陛的操作和维修建议。
一、常用振动分析方法
常用的振动分析方法有波形、频谱、相位分析及解调分析法。频谱图显示振动信号中的各种频率成分及其幅值,不同的频率成分往往与一定的故障类别相关。波形图是对振动信号在时域内进行的处理,可从波形图上观察振动的形态和变化,波形图对于不平衡、松动、碰摩类故障的诊断非常重要。双通道相位分析通过同时采集两个部位的振动信号,从相位差异中可以对相关故障进行有效的鉴别。解调是提取低幅值、高频率的冲击信号,通过包络分析,给出高频冲击信号及其谐频,此技术在监测滚动轴承故障信号方面较为有效。
二、转动设备常见故障振动特征及案例分析
1、不平衡
转子不平衡是由于转子部件质量偏心或转子部件出现缺损造成的故障,它是旋转机械最常见的故障。结构设计不合理,制造和安装误差,材质不均匀造成
的质量偏心,以及转子运行过程中由于腐蚀、结垢、交变应力作用等造成的零部件局部损坏、脱落等,都会使转子在转动过程中受到旋转离心力的作用,发生异常振动。
转子不平衡的主要振动特征:
1)振动方向以径向为主,悬臂式转子不平衡可能会表现出轴向振动;
2)波形为典型的正弦波;
3)振动频率为工频,水平与垂直方向振动的相位差接近90度。
案例:某风装置泵轴承箱靠联轴器侧表面振动烈度水平13.2 mm/s,垂直11.8 mm/s,轴向12.0 mm/s。各方向振动都为工频成分,水平、垂直波形为正弦波,水平振动频谱如图1所示,水平振动波形如图2所示。再对水平和垂直振动进行双通道相位差测量,显示相位差接近90度。诊断为不平衡故障,并且不平衡很可能出现在联轴器部位。
解体检查未见零部件的明显磨损,但联轴器经检测存在偏心,动平衡操作时对联轴器相应部位进行打磨校正后振动降至2.4 mm/s。
2、不对中
转子不对中包括轴系不对中和轴承不对中两种情况。轴系不对中是指转子联接后各转子的轴线不在同一条直线上。轴承不对中是指轴颈在轴承中偏斜,轴颈与轴承孔轴线相互不平行。通常所讲不对中多指轴系不对中。
不对中的振动特征:
1)最大振动往往在不对中联轴器两侧的轴承上,振动值随负荷的增大而增高;
2)平行不对中主要引起径向振动,振动频率为2倍工频,同时也存在工频和多倍频,但以工频和2倍工频为主;
3)平行不对中在联轴节两端径向振动的相位差接近180度;
4)角度不对中时,轴向振动较大,振动频率为工频,联轴器两端轴向振动相位差接近180度
案例:某高速泵由振动频谱图(图3)可以看出,50 Hz(电机工频)及其2倍频幅值显著,且2倍频振幅明显高于工频,初步判定为不对中故障。再测量泵轴承箱与电机轴承座对应部位的相位差,发现接近180度。
解体检查发现联轴器有2根联接螺栓断裂,高速轴上部径向轴瓦有金属脱落现象,轴瓦间隙偏大;高速轴止推面磨损,推力瓦及惰性轴轴瓦的间隙偏大。检修更换高速轴轴瓦、惰性轴轴瓦及联轴器联接螺栓后,振动降到A区。
3、松动
机械存在松动时,极小的不平衡或不对中都会导致很大的振动。通常有三种类型的机械松动,第一种类型的松动是指机器的底座、台板和基础存在结构松动,或水泥灌浆不实以及结构或基础的变形,此类松动表现出的振动频谱主要为1x。第二种类型的松动主要是由于机器底座固定螺栓的松动或轴承座出现裂纹引起,其振动频谱除1X外,还存在相当大的2X分量,有时还激发出1/2X和3X振动分量。第三种类型的松动是由于部件间不合适的配合引起的,产生许多振动谐波分量,如1X、2X、6868,nX,有时也会产生1/2X、1/3X、6868等分数谐波分量。这时的松动通常是轴承盖里轴瓦的松动、过大的轴承间隙、或者转轴上零部件存在松动。
案例:某风机振动增大,轴承箱最大振动16.9 mm/s。该机为悬臂式离心式风机,最大振动在轴承箱靠叶轮侧,倍频丰富,初步判断存在松动。监测四个地脚,发现其中一个地脚03(靠叶轮侧)振动较大,约9 mm/s,其余三个地脚振动分别为0.5 mm/s、1.8 mm/s和2.0 mm/s,很明显03地脚有松动。
由引风机地脚03垂直振动频谱图(图4)可以看出,1X、2X较大,还有较多的谐波成分。紧固地脚螺栓后轴承箱最大振动降至4.2 mm/s,仍偏大,分析应该还存在轴承或轴上零件配合松动。解体检查引风机,发现轴承与压盖紧力不足,加铜垫片调整压盖紧力后振动降到2.7 mm/s。
案例:某风机非联轴器端轴承箱振动大幅上升,最大振动轴向方向为14.8 mm/s。现场监测记录列于表1。水平、垂直、轴向振动均表现出2倍工频显著,且垂直、轴向2倍工频幅值大于工频成分。
因轴支承为滑动轴承,据相关振动分析理论,轴瓦松动将使转子产生很大的振动,振动频率一般为1/2或2倍转速频率,初步分析可能存在轴承压盖紧力不足,建议先检查轴承压盖紧力。检查验证确实存在压盖紧力不足,调整后振动降至B区。
4、流体扰动
高速离心泵中的流体,从叶轮的流道中流出,进入扩压器或蜗壳时,如果流体的流动方向与叶片角度不一致,流道中就产生很大的边界层分离、混流和逆向流动,流体对扩压器叶片和蜗壳隔舌的冲击,将使流体在管道中引起很大的压力脉动和不稳定流动,这种压力波又可能反射到叶轮上,激发转子振动,振动频率为叶轮叶片数乘以转速(称叶片过流频率)或其倍数。在工艺流量与泵额定流量偏差较大或叶轮出口与蜗壳对正不良时,过流频率振动明显,称流体扰动。一般把叶轮外缘和开始卷曲处的距离拉大,能够缓和压力脉动并减小振幅。
结语
关于转动机械滚动轴承的相关介绍就到这了,如有不足之处欢迎指正。
-
轴承
+关注
关注
4文章
2146浏览量
31441 -
转动
+关注
关注
0文章
10浏览量
7911
发布评论请先 登录
相关推荐
项目分享:基于机智云平台的滚动轴承在线监测系统
基于DSP+MCU的列车滚动轴承故障诊断系统研究
滚动轴承的圆度怎么检测?
滚动轴承故障诊断的实用技巧
滚动轴承的基础介绍和噪声测试的详细资料概述
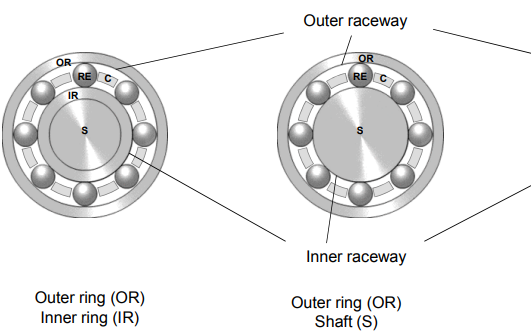
评论