0glass认为:工业4.0存在两个维度,第一个是“把人变成机器”,第二个“把机器变成人”。
0glass助力工业4.0概念落地,要做的就是“把人变成机器”,让AR智能眼镜辅助产业工人的生产工作和培训,把互联网和信息技术延伸到一线员工的工作当中,实现难以实现之事:比如持续记忆、标准化规范化的工作、人的大数据采集分析、即需即学的培训等。使工作实操、实时纠错、培训和知识传承等无限拉近在一个平面,提高生产效率、降低出错率、降低生产成本、进行个性化培训等。
“把机器变成人”,通过各类人工智能技术赋予设备和机器以智能,让其替代人类部分和甚至全部工作,也是工业4.0重要的落地方法之一。但在各个领域都能完全替代人工还需要一个漫长的过程。
近80%的中国企业希望拥抱工业4.0,但40%以上的企业认为自己还没有做好踏上工业4.0征程的准备。
工业4.0(又称第四次工业革命)是制造业数字化水平提升的时代机遇。
扎根于物联网、云计算、人工智能、虚拟现实、增值制造、机器人等突破性技术,工业4.0充分整合、优化虚拟和现实世界中的资源、人才和信息,致力于打造高灵活度、高资源利用率的“智能工厂”,实现从产品开发、采购、制造、分销、零售、到终端客户的连续、实时信息流通。这条贯穿整个商业价值链的“数字线程”,大大提高信息透明度,实现运营成本大幅降低、产品高度个性化、以及灵活高效的制造与产品开发流程,并促进商业模式的创新。工业4.0是突破世界现有生产力增长瓶颈的重要机遇。中国虽在近30年书写了制造业的传奇,但生产力仍落后于发达国家:即使是经过了15年的迅猛发展,生产力水平仍仅为主导发达国家的1/5。中国制造业过往的快速增长主要 依赖廉价劳动力、资本及对创新的模仿,但这些竞争优势如今正逐渐丧失。中国政府公布了《中国制造2025》,力争借助工业4.0的浪潮,从世界第一制造大国跻身发达制造大国之列。但中国制造商要成功实现数字化转型,必须基于自身现状,寻求适合中国的数字化转型之路。为全面了解中国企业的数字化运营现状,麦肯锡访问了130位来自各行业的企业代表。调查显示,中国制造商对工业4.0抱有极大的热情和期待(见下图),比美、日、德企业更为乐观:76%的中国受访企业相信技术革命将增强自身竞争力,远高于美、德、日三国(美57%,德50%,日54%)。而且, 中国民营企业最为乐观,86%的民企认为技术革命有利于提升竞争力,而国企和跨国企业相对保守,分别为68%和73%。
虽然中国制造商对工业4.0抱有很大的热情和期望,但对实施具体策略有 较多疑虑。只有57%的中国企业对工业4.0做好了充分的准备,远低于美国(71%)和德国(68%)。其中,国企最为保守,民企则大胆些:仅44%的国企声称已做好准备,而民企高达68%。中国制造商在数字化转型中的疑虑很可能来自于战略策略的不成熟。虽然43%的中国企业表示已制定了宏观的变革战略,但只有9%的企业能真正细化到清晰明确的职责分工,而该比例在美国 为33%、德国为35%,在日本为21%;另外,仅有6%的中国企业制定了明确 的实施路径,远低于美、德、日企业(22%,22%,31%)。相应地,缺乏系统的实施路径/工具箱亦成为中国制造业数字化转型的主要障碍。为了进一步探究中国制造业的现状,我们与50多位不同行业的企业代表和专家进行了深入的访谈,从数字化运营系统、管理系统和生态系统这三个维度对中国制造业进行了研究(见下图)。我们发现中国企业在这三个维度上均存在明显的差距和机遇。
数字化运营体系目前,中国企业在价值链各职能环节上,包括产品开发、供应链、生产制造、销售和营销及售后服务,都未能充分有效地利用数字化管理工具。以汽车制造业为例:产品开发、供应链和质量管理都是亟待提高的核心领域。要生产出高品质、低成本的汽车,中国企业需要进行研发能力建设,在供应链中引入数字化的工具和流程,建立数字化的质量管理系统,并实现整条价值链的信息流程贯通和系统化质量提升。管理基础设施及理念与能力对工业4.0这一新概念的过度热衷很可能导致企业在技术设备上的非理性投资。事实上,许多中国企业在组织架构、绩效管理系统及人才、管理理念等仍不成熟,从而缺少对工业4.0的必要支撑。在组织架构上,仅有9%的受访企 业在工业4.0项目上有明确的职责分工,仅有6%的受访企业为工业4.0项目制 定了清晰明确的实施路径。同样,工业4.0具体实施路径规划、数字化人才、商业论证的匮乏是受访企业在工业4.0征程上的最大障碍。绩效管理体系和工业4.0项目的割裂是中国企业普遍存在的另一个问题。管理理念上,大多数企业并未把数字化转型视作核心事务,而只是一种象征性的举动,导致工业4.0 战略策略的狭窄和短视。总体而言,许多中国企业在从管理人员到一线员工, 从个人意识到技术技能等各个方面,要做好踏上工业4.0征程的准备还有很多工作要做。生态系统的相互作用中国工业4.0生态系统的建设处于刚刚起步的阶段:政府担任初始驱动者;技术开发资本开始涉足工业4.0领域;领先的制造商亦开始为自己打造跨企业、跨行业的生态系统。但中国的生态系统在许多方面仍落后于发达国家。 最为显著的差距表现在:研究与技术应用之间的脱节,缺乏具有核心竞争力的技术解决方案,以及行业参与者在价值链内协调性的不足。设计具有中国特色的工业4.0路径中国制造商能力参差不齐,现状复杂。要在数字化转型中成功获取最大的价值,需要的不是“万金油”式的解决方案,而是基于公司个体能力与业务需求量身定制的工业4.0路径(见下图)。
对缺乏精益运营基础、自动化水平低的企业来说,采用精益运营模式和理念,更能带来快速和显著的正面影响。此外,关键加工步骤的自动化、建立数据收集、分析、决策和执行能力也将是快速有效的抓手。对已拥有半自动化生产,并在关键质量节点进行数据收集的企业来说,升级管理组织架构,培养可以有效支持数字化转型、强化数据管理、分析、决策和执行的理念和能力,将会是突出重围的制胜关键。对已有先进制造水平,并具有敏捷的管理体系和商业模式的领先企业来说,借助数字化工具进一步提升管理和运营的敏捷性和灵活性,并大胆采用创新的商业模式,将是保持领先的关键。
中国制造要牢牢抓住工业4.0的机遇,必须通过以下三个关键举措设计量身定制的数字化转型路径。
打好数字化管理架构和理念能力基础
在基于不同业务职能的传统组织架构基础上,实施以传统职能团队作为支持平台,项目团队作为内部创业小组的双速组织设置,不仅能保证稳定性,还能提高敏捷性和创新的持续性。此外,管理层对数字化转型的共识和决心,有效的激励机制、数字化的绩效管理方法及数字化人才培养都是实现数字化转型的关键成功因素。设计数字化转型的战略举措适应定制化、自动化、智能化是全球制造业的发展趋势。借助工业4.0的技术浪潮,各行业应根据产品和客户类型、竞争动态判断相应产业发展趋势,并基于自身的基础,找出价值回报潜力最高的数字化领域,制定相应的数字转型战略和执行路线。
高效的产品开发:如今产品迭代速度加快、消费者需求不断变化。如 果能有效利用工业4.0带来的虚实结合理念和工具(CPS)、模块化、 标准化的研发模式,就能更快地完成从产品概念到产品原型的市场和 生产测试,再到量产和销售,企业就能更快地推出新产品,从而获得 市场先入的优势,赢得更可观的市场份额和利润。这对于快速迭代的高科技产品市场尤为重要。
定制化柔性生产:用户端的价值需求是重要的价值驱动因素。由用户需求驱动的产品开发,灵活高效的供应链和生产线,大数据驱动的精准营销和销售,以及售后智能服务和数据反馈等数字化转型举措将协助企业更快更好地响应快速变化的市场和消费者需求。另外,对B2B企业,利用互融互通的软件系统和数字化平台与关键客户、供应商在产品研发、订单排产、售后跟踪服务上进行更紧密地协作和信息互通,也是关键的数字化举措。
自动化、智能化生产: 打造信息化的,且与生产需求节奏相匹配的供应链、自动化的生产线、数字化的管理系统,尤其是工业4.0带来的自省、自我预测、自我维护等监测和控制系统的新功能,能够减少人为失误,降低人力成本, 减少流程浪费,提高生产效率,进而提升产品的质量和利润。这是许多行业在未来激烈竞争中创造利润和价值的关键举措,尤其是那些需要量产且利润空间压力较大的大宗商品企业。
建立可持续的生态体系在工业4.0方面领先全球的国家已经采取一系列行动,推动当地工业4.0生态体系的发展。美国为促进最新数字生产技术在工业的应用,建立了由联邦政府领导的国家制造业创新网络。德国政府针对工业4.0定期出台各方面的配套政策。在制造商层面,德国汽车零部件和家用电器制造商博世集团与价值链内外的50多个企业建立合作关系,发展物联网技术的创新应用。基于国际最佳实践,中国要加快数字化运营生态体系的建设,需要
①建立全国性创新中心;
②加强学术界和工业间研发和应用的联系;
③为初创企业和中小企业提供资金、设施、政策支持;
④吸引海内外数字化人才;
⑤加强网络安全的防范措施;
⑥协调供应链企业的数字化改造;
⑦拓展制造商与垂直行业间的战略合作伙伴关系。
总体而言,中国制造业并没有像美国、德国等发达国家那样由第三次工业革命逐渐过渡到第四次工业革命。许多中国企业仍处于工业2.0,甚至更低的水平。但工业4.0这一新概念加上中国制造2025行动纲领的大力推广使许多企业对数字化转型抱以很大的热情和期望。不过,要使数字化转型、智能制造的 愿景真正落地,中国企业必须根据自己的发展现状、行业发展趋势,打好精益 管理基础、审慎选择数字化技术投资的领域,积极建设数字化组织架构、管控机制和人员能力,而且要放眼全局,勇于合作,打造良好的产业生态系统。
-
机器人
+关注
关注
211文章
28398浏览量
206996 -
工业4.0
+关注
关注
48文章
2012浏览量
118614
原文标题:中国工业4.0之路|0glass低调分享
文章出处:【微信号:KingseeAR,微信公众号:AR工业应用】欢迎添加关注!文章转载请注明出处。
发布评论请先 登录
相关推荐
OPPO荣登2024中国企业专利创新百强榜第四
高通发布《2023高通中国企业责任报告》
十字路口的全球化,中国企业的破局之道
Meta商业技术负责人出席“2024中国企业出海高质量发展创新大会暨钛动科技秋季AI产品发布会”
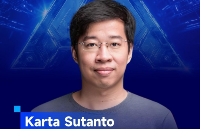
电动汽车电池市场遇阻,中国企业出货量逆势同比大幅增
中国企业扬帆出海正当时 ADVANCE.AI 出海大咖荟 上海站圆满落幕!
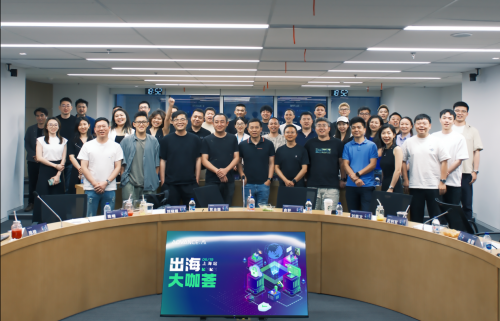
马云双出席2024全国企业家活动日暨中国企业家年会并发表主题演讲
亚马逊云科技推出Claude 3生成式AI大模型,中国企业可调用于其他场景
华为以27.9%的市场份额摘得2023年中国企业级Wi-Fi 6市场桂冠
中国企业超卓航科引领高端溅射靶材产业发展
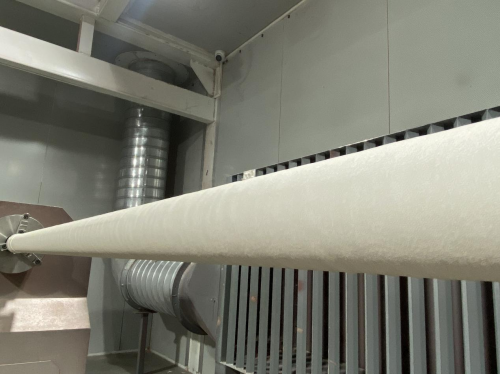
迅镭激光中标中国企业500强潍柴集团,赋能装备智造!
IDC中国企业级存储市场预测
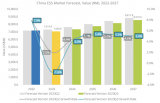
2023中国企业级存储市场:整体韧性成长,领域此消彼长
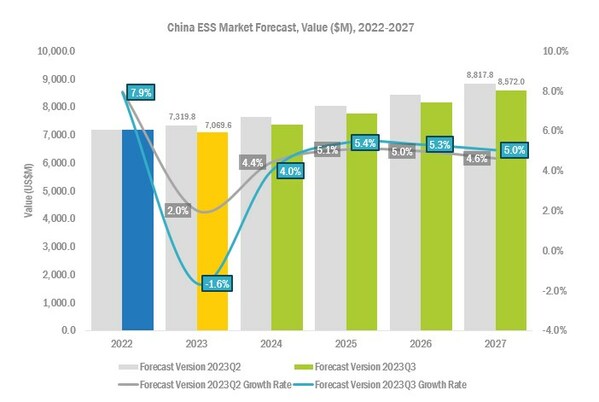
评论