今年1月,入选工信部“中德智能制造合作试点示范项目”的埃斯顿工业机器人智能工厂正式投产。一改传统的人工装配生产模式,埃斯顿工业机器人智能工厂实现埃斯顿自有品牌机器人与核心部件等产品的自动化、柔性化、精益化的智能制造。该工厂由博世力士乐与埃斯顿合作设计与建设,其中三条部件装配线由博世力士乐提供交钥匙解决方案,机器人装配机器人总装线由埃斯顿设计并完成。从2017年3月项目启动到今年初工厂的正式投产,埃斯顿不仅迎来了其创新创业发展新的里程碑,还向业界展现出了智造“加速度”。
对于这座智能工厂,埃斯顿自动化集团董事长总经理吴波给予了高度评价:
它是一个现代化生产设备、先进信息化生产系统、环境优美的智能工厂;
是一个拥有完全自主核心技术,核心部件国产化率最高的机器人生产智能工厂;
是一个具备德国工业4.0技术支撑的,以国产机器人为基础的智能化生产线的生产基地。
在6月中旬的实地探访中,埃斯顿工业机器人智能工厂项目负责人储经理告诉工控小编,通过几个月的实际运行,埃斯顿工业机器人智能工厂目前实现产能提高8倍,制造周期缩短60%,直接人工成本下降50%。
精益生产,通往智能制造的必由之路
近十年,我国机器人产业快速发展。2017年,中国继续成为全球第一大工业机器人市场,销量突破12万台,约占全球总产量的三分之一。
然而,国内机器人厂商依然面临发展“囧”境:中国工业机器人市场依然以进口品牌为主,国产品牌的市场占有率低;进口品牌产品系列齐全,国内品牌产品相对单一;国内厂商的研发实力相对薄弱,对关键零部件进口依赖度高,且直面市场的激烈竞争,“价格战”现象显著。以上种种,都迫使国内机器人厂商借助新一轮科技革命与新兴技术向智能制造和互联工业转型升级,以提升自身的核心竞争力。
在向智能化转型升级的征程中,埃斯顿选择了精益生产与管理路径。“埃斯顿的优势在于,我们是国内少数拥有工业机器人关键技术和核心部件的企业。新工厂的建设初衷,于内要实现埃斯顿自有品牌机器人与核心部件等产品的自动化、柔性化、精益化的智能制造,促进企业升级调整;对外要促进国内机器人行业技术升级,增强我国机器人产业在国际市场的核心竞争力,在行业内起到更好的引领示范作用。”储经理坦言道。
储经理表示,成功建设这一复杂项目的关键在于实现工厂全价值链的精益生产与管理,而博世力士乐作为埃斯顿的长期战略合作伙伴,对精益生产有着深刻的理解,其精益生产系统经过博世集团全球270多个工厂成功验证。同时,博世力士乐拥有在中国成功实施工业4.0项目的丰富经验,可以提供融合工业4.0技术的包含元件、系统、软件在内的整体解决方案,因此成为埃斯顿工业机器人智能工厂项目合作的不二人选。
作为精益生产理念的“布道者”与“践行者”,博世力士乐认为,精益生产系统是引入工业4.0技术并实现生产力转型升级的前提条件。在推广工业4.0技术的同时,博世力士乐更注重与中国制造商分享精益生产理念,帮助其找到最适合自己的转型升级之路。
埃斯顿的“精益生产之道”
古有孔子因材施教,现有博世因地制宜。什么才是适合埃斯顿的“精益生产之道”?博世力士乐为埃斯顿提供了定制化的交钥匙解决方案,主要包含两部分内容:
*以精益生产价值流咨询为基础的智能工厂设计(博世精益生产系统BPS理念)
*质量:产品质量零缺陷
*成本:100%增值的价值创造过程
*交付:100%交付率按客户要求将正确的产品以正确的数量交付至正确的地点
*单件流:产品从客户下单到最后送达客户手中的整个增值过程中不存在缓冲库存,以最大的灵活度和最高的效率满足客户期望。
*三条机器人部件装配线,应用了博世力士乐3种关键的工业4.0产品/技术。
*工业拧紧应用的智能数据解决方案(Tightening):确保所有批次规模的成本效益和可靠的拧紧流程,即使一个批次只有1件产品;并且将所有处理参数归档进行数字生命周期管理。
*智能动态手工装配系统(ActiveAssist):准确识别工件,正确指引员工,100%确保加工质量。
*智能动态生产管理系统(ActiveCockpit):实时显示所有生产数据,进行快速决策和有效沟通。
“相比埃斯顿传统机器人生产线的机械装配和人工装配模式,三条机器人部件装配线消除了以往人工经验所带来差错与不足,能够更高效、更快速、更柔性、更精益地组织实施生产,产品合格率更高,生产流程可视化、数据可追溯。”储经理说,三条产线均采用“智能化工作站+标准化作业”模式,可实现混线生产,从而保证埃斯顿随时都能够以高成本效益和高竞争力的方式来满足客户不断变化的需求。
*小型机器人手腕智能组装线
混线组装:多个型号的小型手腕
单班产能:3080件/年
*小型机器人手臂智能组装线
混线组装:多个型号的小型手臂
单班产能:2900件/年
*大型机器人手腕智能组装线
混线组装:多个型号的大型手腕
单班产能:1650件/年
什么才是中国制造转型升级的正确选择?
“精益生产并非一蹴而就,这是一个持续改进的升级之路,它具有强大的创新力与生命力。埃斯顿则藉由精益设备、精益员工、精益运营三大关键性要素来实现工业机器人智能工厂愿景。”埃斯顿机器人工程有限公司总经理王杰高博士说,从2017年3月启动到现在,埃斯顿机器人智能工厂项目在短短一年时间里已经取得了里程碑式的成果。
王杰高博士表示,投运后的埃斯顿机器人智能工厂,可以说是国内自主品牌机器人产品产能最大、智能化生产制造水平国际国内领先的生产工厂,在业内将率先实现机器人生产的智能制造。另外,本项目的实施,对埃斯顿机器人及核心部件的智能化生产应用与推广、对促进国内机器人行业技术升级、对增强我国机器人产业在国际市场的核心竞争力,都带来了非常积极的作用,经济、社会及环境效益十分显著。
博世力士乐亚太区精益生产管理总监Ingo Claussen表示,博世力士乐与埃斯顿的机器人智能工厂项目引领了国产机器人智能制造迈进新纪元,是博世力士乐与本土企业在工业4.0合作上的又一次成功。
“只选对的,不买贵的”,这句广告语在普罗大众的实践中得到印证。回归中国制造业本身,精益生产以其深厚资历、灵活实用的特性,在当今工业4.0、数字化工厂、工业物联网、工业大数据、人工智能等诸多概念中显示出独特魅力,更有业内专家坚定表明“离开精益制造,别谈什么工业4.0、智能制造”。
可以说,精益化,是中国企业目前最急迫的工业技术升级与管理转型。从农业文明到工业文明的进程中,精益生产是一条必经之路。但它并没有过时,在全球智能制造浪潮下,精益生产更是以与时俱进的开放性吸纳了自动化、信息化与智能化的先进技术,为企业带来“自革命”式的“蝶变”,而这正是中国制造业转型升级的正确路径选择。
项目简介:
埃斯顿工业机器人智能工厂项目,被列为国家发改委增强制造业核心竞争力项目、工信部“中德智能制造合作试点示范项目”、江苏省“双百工程”、南京市重点工程。
项目预计总投资10亿元,其中一期计划投资5.9亿元,主要为建设机器人产品生产智能化车间12000平米、机器人智能制造生产线车间12000平米、中试车间8000平米。项目一期投产,机器人及成套设备产能达到9000台/套。
该智能工厂的落成实现了机器人本体生产的自动化、信息化,将机器人自主产品成功应用到生产线中,自主机器人产品应用在50台套以上,实现在装配、搬运、检测等工艺环节用机器人生产机器人,使用MES系统、WMS系统、云数据、PCS系统、PMS系统等信息化手段实现机器人本体生产的智能化,保证机器人产品的品质和过程监控,使得国产机器人的工程化和产业化水平迈上新的台阶,赶超国际先进水平。
-
机器人
+关注
关注
211文章
28366浏览量
206888 -
智能制造
+关注
关注
48文章
5543浏览量
76306 -
智能工厂
+关注
关注
3文章
997浏览量
42405
原文标题:案例:精益生产,“智”赢未来
文章出处:【微信号:ofweekgongkong,微信公众号:OFweek工控】欢迎添加关注!文章转载请注明出处。
发布评论请先 登录
相关推荐
解锁精益生产,照亮LED的智能制造之路!
航空电子的精益转型之路
智能电网的精益转型之路怎么走
光伏行业的精益转型之路
如何在数字化时代实现精益生产的创新发展?
构建数字化精益生产体系,提升制造业竞争力新策略
研华DataInsight助力制造业精益生产,引领数智制造大势
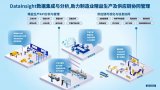
评论