两种紧凑,高效的灯泡更换设计理念
LED灯现在作为标准白炽灯的插件替代品在零售店中占据显着位置。在标准尺寸灯泡的颈部内安装LED所需的保护和恒流驱动电子设备是一种挤压,特别是对于使用T8灯管或基于爱迪生螺旋的紧凑型设计的灯具。在这些应用中,驱动电子设备的空间非常小,并且限制了可以使用的部件的尺寸和数量。缺乏空间也加剧了热管理问题。更糟糕的是,LED负载的位置使其与电源紧密热接触。为避免过热和随之而来的故障,LED驱动器必须以尽可能高的效率运行。
严格的规定
除了提供稳定的恒流输出外,LED驱动器(电源)还必须遵守日益严格的法规,涵盖功率因数和电源消耗的谐波失真。 1 许多LED驱动器解决方案采用两级方法,具有升压PFC级,后接一个恒流驱动器,通常是反激式转换器。升压PFC级通常可实现95%的最大效率,恒流驱动器约为90%,整体效率达到85%。
这种方法需要一个电感器,两个电源开关和两个控制器 - 许多组件都可以装入一个小型灯壳中。 PFC级和反激式转换器分别执行开关电流流动或输入和输出电流整形的类似功能。如果两个开关活动可以组合成单个级,则需要更少的组件,并且仅用一个驱动器电路和一个开关级就可以实现更高的效率。
图1:使用组合式PFC和CC转换器的单级LED驱动器。
这种电路如图2所示 - 单级,组合PFC和恒流驱动器,使用Power Integrations公司生产的LinkSwitch™-PH IC。 2 单片器件采用725 V功率MOSFET与集成控制和保护电路配合使用。
图2:单级组合PFC和CC转换器使用LinkSwitch-PH(来源:Power Integrations)。
控制PFC和恒定电流
控制器结合了专有的功率因数校正技术和初级侧控制连续导通模式PWM开关功率级。通过在单个集成电路内将这种控制方法与单片功率MOSFET和相关的驱动电路相结合,可以显着减少LED驱动器的元件数量。
使用LinkSwitch-PH IC和图2所示的电路,对于需要电路的15 W LED驱动器(相当于60 W白炽灯泡),可实现大于90%的转换效率比同等的两阶段方法更少的组件。由于输入电流直接由电源开关整形,因此不需要输入大容量电容。 LED驱动器不使用电解大容量电容器,其在LED灯中所见的升高的环境温度下具有短寿命,这可能导致两级解决方案的问题。
最低成本的非隔离解决方案
虽然隔离式反激式转换器非常有效,但它们在效率,尺寸和成本方面存在一些限制。电源变压器中的开关损耗降低了整体效率,而电气隔离间隙空间可占据8 W转换器总可用电路板面积的15%以上。由于变压器必须满足高压隔离要求和更昂贵的结构,因此磁性元件的成本更高。
更简单且成本更低的方法,至少对于高达30瓦的功率水平,是使电源不隔离并使用灯泡外壳作为安全隔离。这允许使用更有效(无变压器损耗)的简单降压/降压 - 升压转换器,并使用更低成本的磁性(电感器)。仍然可以使用已经描述的LinkSwitch-PH系列器件和Power Integrations的LinkSwitch™-PL系列的单级组合PFC + CC转换方法。这些器件可配置为用于低压输出的高效降压转换器,提供具有低THD的高PF,并实现高集成度和简单降压架构所固有的节省。这种方法适用于许多设计,尤其适用于高压应用(176 VAC至264 VAC)。
使用尽可能高的LED串电压获得高效率,但是,特别是在低压(90 VAC至132 VAC)应用中,这种方法显示出降压转换器的局限性。如果输出串电压过高,降压转换器无法提供具有足够低THD的解决方案以满足EN61000-3-2(C/D)或达到20%的典型ATHD限值。通过创建与电压波形的正弦波形状紧密匹配的电流波形来实现低THD。当输入电压(整流正弦波)超过输出级时,降压转换器只能将电流传递到输出级。因此,对于每个AC线半周期的一部分,当电压从零上升(并且当电压接近零时),不会发生功率因数校正并且THD减小。对于高输出电压(在低压应用中超过35 VDC),导通角很短,转换器不再能够产生符合EN61000-3-2C/D谐波电流限制的电流波形。
对于高效应用中的许多非隔离LED驱动器,使用降压 - 升压转换器方法。降压 - 升压的一个固有优势是无论输出电压电平如何,它都可以连续从AC输入获取功率,使输入电流接近正弦波。两个例子证明了这种方法的功效和优雅。第一种是长串LED驱动器,设计用于安装在T8管灯内。该电路能够驱动100 V LED串,但效率超过91%,功率因数大于0.9,THD超过25%。第二种设计使用最少的组件,旨在安装在小型B10灯罩内。
图3:采用LNK409EG的25 W降压 - 升压型LED驱动器原理图(来源:Power Integrations)。
图3是采用降压 - 升压拓扑的完整非隔离25 W功率因数校正LED驱动器电路。 3 它提供250 mA恒定电流输出,标称值为100 V,电压为180 -265 VAC输入。
物理设计非常出色,如图4和图5所示。电路板宽19.5毫米,高10毫米。
图4:填充电路板(来源:Power Integrations)。
图5:安装在T8灯管中的LED驱动器(来源:Power Integrations)。
降压 - 升压电源电路由U1,输出二极管D6,输出电容C5和C7以及输出电感T1和T2组成。由于管内的空间限制,使用两个电感器。 T1和T2一起提供所需的降压 - 升压电感,T1中的偏置绕组为U1提供电源电流,并为断开的负载/过压关断功能提供反馈。
无电流检测
LinkSwitch-PH IC提供高精度输出恒流控制,无需与负载串联的电流检测电阻。 R7-R10,Q1,C6和D5包含一个电压 - 电流转换器网络,可向反馈(FB)引脚提供与输出电压成比例的控制电流。二极管D1和C3检测峰值AC线电压。 C3上的电压以及R3和R4设置输入电压进入电压监测(V)引脚。 U1使用该电流来控制线路欠压(UV),过压(OV)和前馈电流。
LinkSwitch-PH器件内部控制引擎结合反馈引脚电流,电压监测引脚电流和漏极电流信息,在1.5:1输出电压变化范围内提供恒定输出电流(LED串电压变化± 25%),在固定线路输入电压。恒流控制引擎可补偿电感容差以及输入和输出变化。
低EMI特征是LinkSwitch-PH的连续导通模式PFC功能和频率抖动的结果。这种EMI滤波非常简单,足够小,可以安装在T8灯管的范围内。
Candelabra
第二个例子中应用的设计目标是高效率和小尺寸,使驱动器适合装入烛台和B10尺寸灯。
图6:使用LNK458KG的4.5 W降压 - 升压电源(来源:Power Integrations)。
图6显示了4.5 W功率因数校正LED驱动器(非隔离降压 - 升压),这次使用Power Integrations的LinkSwitch-PL LNK458KG。 4 LinkSwitch-PL 5 IC与前面讨论的LinkSwitch-PH设备非常相似。它们针对低功耗,非隔离应用(高达16 W)进行了优化,并且只需四个连接即可提供。该控制算法使用直接LED电流检测,并且可以使用最少的外部元件支持无闪烁TRIAC调光。
图6所示电路从85 -135 VAC输入提供超过42 - 56 V的90 mA恒流输出。尽管元件数量非常少,但LED驱动器的效率超过86%,PF大于0.95,而115 VAC时THD超过15%。
图7:填充电路板(来源:Power Integrations)。
图7中的填充电路板仅宽16 mm,长28 mm。
设计选择
为了最大限度地减少元件数量和最大化效率,我们做出了许多重要的设计选择该设计经过优化,可在低交流输入电压范围(85-135 VAC和47-63 Hz)下工作。在使用中,驱动器与LED负载一起封装在密封的外壳中。非隔离输出依靠外壳为用户提供保护,如果LED输出失效开路,驱动器将关闭以防止发生过压。
在电路输入端,EMI滤波由2-π滤波器网络执行,该滤波器网络由电容器C1,C2,C3和差分扼流圈L1和L2组成。输入滤波器加上LinkSwitch-PL器件的频率抖动功能可以符合B类发射限值。有限的总电容保持高功率因数。
降压 - 升压动力传动系由U1(电源开关+控制),D2(续流二极管),C7(输出电容)和L3(电感)组成。二极管D1用于防止出现在U1的漏极 - 源极上的负电压,特别是在输入电压的过零点附近。当功率MOSFET导通时,旁路电容C4为器件提供内部电源。输出电流反馈通过R3上的压降检测,然后通过低通滤波器(R4和C5)进行滤波,以保持LinkSwitch-PL IC工作点,使得平均FEEDBACK(FB)引脚电压为290 mV in稳态运行。
只需调整R3和R5的值即可设置输出电流工作点。通过将R3更改为12.7Ω,将R5更改为13Ω,电路将在96 V标称输出下提供45 mA电流。
-
led
+关注
关注
242文章
23502浏览量
666400 -
驱动器
+关注
关注
54文章
8404浏览量
147881 -
控制器
+关注
关注
113文章
16624浏览量
180665
发布评论请先 登录
相关推荐
5个灯的LED闪光灯驱动器电路,5 Lamp/LED Fla
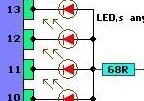
基于ROHM的车载背光灯用LED驱动器电路设计
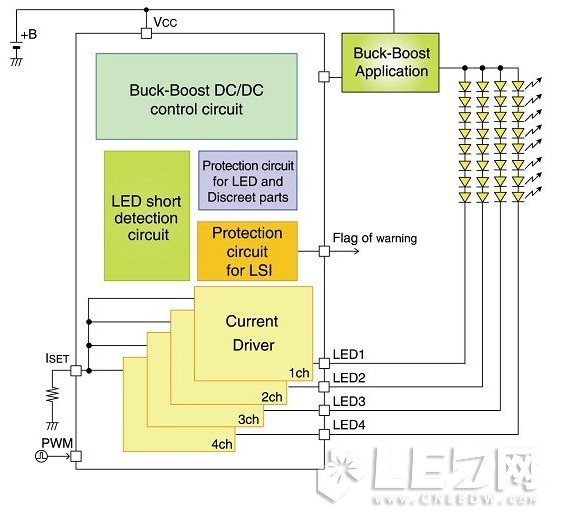
评论