简介
高性能伺服电机的特点是需要平稳旋转到失速,完全控制失速时的扭矩以及快速的加速和减速。过去,变速驱动器主要采用直流电机,因为它们具有出色的可控性。然而,现代高性能电动机驱动系统通常基于三相交流电动机,例如交流感应电动机(ACIM)或永磁同步电动机(PMSM)。这些机器已经取代了直流电机作为苛刻的伺服电机应用的首选机器,因为它们结构简单,惯性小,输出功率重量比高,在高速旋转时具有良好的性能。
现在已经很好地建立了矢量控制原理来控制这些交流电机;现在大多数现代高性能驱动器都采用数字闭环电流控制。在这样的系统中,可实现的闭环带宽与计算密集型矢量控制算法和相关矢量旋转可以实时实现的速率直接相关。由于这种计算负担,许多高性能驱动器现在使用数字信号处理器(DSP)来实现嵌入式电机和矢量控制方案。 DSP固有的计算能力可以实现非常快的周期时间和闭环电流控制带宽(在2到4 kHz之间)。
这些机器的完整电流控制方案也需要高 - 精密脉冲宽度调制(PWM)电压生成方案和高分辨率模数(A / D)转换(ADC),用于测量电机电流。为了保持平稳控制扭矩到零速,转子位置反馈对于现代矢量控制器至关重要。因此,许多系统包括转子位置传感器,例如旋转变压器和增量编码器。我们在此描述实现三相交流电机高性能控制器(如ADMC401)背后的基本原理 - 集成DSP控制器,强大的DSP内核,灵活的PWM生成,高分辨率A / D转换,和嵌入式编码器接口。
交流电机的变速控制
三相交流电机的高效变速控制需要生成具有可变频率的平衡三相可变电压组。可变频率电源通常通过使用功率半导体器件(通常为MOSFET或IGBT)作为固态开关从直流转换产生。常用的转换器配置如图1(a)所示。它是一个两级电路,其中固定频率的50或60 Hz交流电源首先被整流,以提供存储在直流链路电容器中的直流链路电压Vd。然后将该电压提供给逆变器电路,该逆变器电路为电动机产生可变频率的交流电。逆变器电路中的电源开关允许电机端子连接到Vd或地。这种操作模式提供了高效率,因为理想情况下,开关在打开和关闭位置都没有损耗。
通过快速顺序打开和关闭六个开关(图1a),三相可以在输出端子处合成具有平均正弦波形的交流电压。实际输出电压波形是脉冲宽度调制(PWM)高频波形,如图1b所示。在使用固态开关的实际逆变器电路中,可以实现大约20kHz的高速开关,并且可以在非常高的频率下产生复杂的PWM波形,其中所有电压谐波分量都是如此。远高于所需的基频 - 名义上在0到250 Hz的范围内。
电机的感抗随频率的增加而增加,因此高次谐波电流非常小,并且接近正弦电流在定子绕组中流动。如图1b所示,通过使用适当的控制器改变PWM波形来调节逆变器的基波电压和输出频率。在控制基波输出电压时,PWM过程不可避免地会修改输出电压波形的谐波含量。正确选择调制策略可以最大限度地降低谐波电压及其相关的谐波效应和电机中的高频损耗。
a。用于驱动三相交流电机的电源转换器的典型配置。
b。为电机生成可变电压,变频电源的典型PWM波形。
脉冲宽度调制(PWM)生成
在典型的交流电机控制器设计中,两者都是在产生PWM信号的过程中涉及硬件和软件考虑,最终用于打开或关闭三相逆变器中的功率器件。在典型的数字控制环境中,控制器以PWM开关频率(标称值为10至20 kHz)产生定时定时中断。在中断服务程序中,控制器软件计算用于驱动逆变器三个支路中每个支路的PWM信号的新占空比值。计算的占空比取决于电机的测量的状态(扭矩和速度)和期望的运行状态。占空比逐周期调整,以使电机的实际运行状态符合所需的轨迹。
一旦处理器计算出所需的占空比值,就需要一个专用的硬件PWM发生器来确保在下一个PWM和控制器周期产生PWM信号。 PWM生成单元通常由适当数量的定时器和比较器组成,这些定时器和比较器能够产生非常精确的定时信号。通常,期望产生PWM定时波形的10至12位性能。 ADMC401的PWM生成单元的边缘分辨率为38.5 ns,对应于开关频率为10 kHz时的大约11.3位分辨率。 ADMC401的专用PWM生成单元产生的典型PWM信号如图2所示,用于逆变器支路A.图中,AH是用于驱动逆变器支路A的高端功率器件的信号,AL用于驱动低端电源设备。占空比有效地调整施加到电机的平均电压,以实现所需的控制目标。
通常,关闭一个电源设备之间需要一个小的延迟(说AL)并打开互补电源设备(AH)。需要此死区时间以确保关闭设备有足够的时间在其他设备打开之前重新获得其阻塞功能。否则可能导致直流电压短路。 ADMC401的PWM生成单元包含用于自动死区时间插入PWM信号的必要硬件。
三相交流电机控制器的一般结构
对任何电动机驱动过程的精确控制最终可以减少到精确控制电动机的转矩和速度的问题。通常,通过使用适当的换能器测量电动机的速度或位置来直接控制电动机速度,并且通过适当控制电动机相电流间接控制转矩。图3显示了用于三相电机的典型同步框架电流控制器的框图。该图还显示了软件代码模块与电机控制器(如ADMC401)的专用电机控制外设之间的任务比例。控制器由两个比例加积分加差分(PID)电流调节器组成,用于控制参考系中的电机电流矢量,该参考系与测量的转子位置同步旋转。
有时可能需要在电压和速度之间实现去耦,从而消除速度依赖性和相关轴与控制回路的交叉耦合。然后使用合适的脉冲宽度调制策略(例如空间矢量调制(SVM))在逆变器上合成参考电压分量。还可以采用一些补偿方案来克服逆变器开关死区时间,有限逆变器设备导通电压和直流链路电压纹波的失真影响。
这两个组成部分定子电流矢量称为直轴和正交轴组件。直轴电流控制电机磁通,通常用永磁电机控制为零。然后可以通过调节正交轴分量直接控制电动机转矩。快速,精确的转矩控制对于高性能驱动至关重要,以确保在所有负载条件下快速加速和减速以及平滑旋转至零速度。
通过以下方式获得实际的直流和正交电流分量首先使用片上ADC系统,使用合适的电流感应传感器测量电机相电流并将其转换为数字电流。通常只需同时采样两个电机线路电流就足够了:由于三个电流之和为零,必要时可以从其他两个电流的同时测量推断出第三个电流。
控制器软件利用数学矢量变换(称为驻车变换),确保在所有运行条件下,应用于电机的三相电流组与电机轴的实际旋转同步。这种同步确保电动机始终产生每安培的最佳扭矩,即以最佳效率运行。矢量旋转需要实时计算测量的转子角度的正弦和余弦,以及多次乘法和累加运算。总的控制环路带宽取决于闭环控制计算的实施速度以及新的占空比值的计算结果。 26-MIPS,16位定点DSP内核固有的快速计算能力使其成为这些嵌入式电机控制应用的理想计算引擎。
模数转换要求
< p>为了控制高性能交流伺服驱动器,需要对测量电流值进行快速,高精度,同步采样的A / D转换。伺服驱动器具有额定运行范围 - 它们可以连续维持的特定功率水平,电机和功率转换器的温升可以接受。伺服驱动器还具有峰值额定值 - 能够在短时间内处理远远超过额定电流的电流。例如,可以在短时间内施加高达额定电流的六倍。这允许瞬时施加大扭矩,非常快速地加速或减速驱动器,然后恢复到正常操作的连续范围。这也意味着在驱动器的正常操作模式下,仅使用总输入范围的一小部分。
在秤的另一端,为了实现平稳和精确的旋转在这些机器中需要,补偿小的偏移和非线性是明智的。在任何电流传感器电子设备中,模拟信号处理通常受到增益和偏移误差的影响。例如,在用于不同绕组的电流测量系统之间可能存在增益不匹配。这些效果结合在一起产生不希望的扭矩振荡。为了满足这两种相互矛盾的分辨率要求,现代伺服驱动器使用12至14位A / D转换器,具体取决于应用所需的成本/性能折衷。
系统的带宽基本上受输入信息然后执行计算所需的时间量的限制。转换需要很多微秒的A / D转换器会在系统中产生无法容忍的延迟。闭环系统的延迟会降低系统可实现的带宽,带宽是这些高性能驱动器中最重要的品质因数之一。因此,快速模数转换是这些应用的必要条件。
这些应用中使用的A / D转换器的第三个重要特性是 timing 。除了高分辨率和快速转换之外,还需要同步采样。在任何三相电机中,必须在完全相同的时间测量电机三个绕组中的电流,以便获得机器中扭矩的瞬时“快照”。任何时间偏斜(不同电流的测量之间的时间延迟)是通过测量手段人为插入的误差因子。这种非理想性直接转化为转矩波动 - 这是一种非常不理想的特性。
集成在ADMC401中的ADC系统提供快速(6 MSPS),高分辨率(12- bit)ADC内核集成了双采样和保持放大器,可以同时采样两个输入信号。 (如前所述,这允许计算第三电流的同时值。)ADC内核是高速流水线闪存架构。可以转换总共8个模拟输入通道,接受附加的系统或反馈信号以用作控制算法的一部分。这种集成性能水平代表了用于高性能应用的嵌入式DSP电机控制器的最新技术。
位置感应&amp;编码器接口单元
通常,电机位置通过使用安装在转子轴上的编码器来测量。增量编码器产生一对正交输出(A&amp; B),每个输出在电机轴的每转中具有大量脉冲。对于具有1024行的典型编码器,两个信号每转产生1024个脉冲。使用专用的正交计数器,可以对A和B信号的上升沿和下降沿进行计数,这样转子轴的一次旋转可以分成4096个不同的值。换句话说,1024线编码器允许将转子位置测量为12位分辨率。旋转方向也可以从正交信号A和B的相对相位推断出来。
通常在电机控制器上有一个专用的编码器接口单元(EIU);它管理双正交编码器输出信号的转换,以产生并行数字字,始终代表实际的转子位置。通过这种方式,DSP控制软件可以在算法需要时简单地读取实际的转子位置。
这一切都很好,但是成本敏感的伺服电机驱动器种类越来越多具有较低性能要求的应用既不能承受转子位置传感器的成本也不能满足空间要求。在这些情况下,可以使用估计的而不是测量的转子位置来实现相同的电机控制算法。
DSP内核能够使用复杂的转子位置估算算法计算转子位置,例如扩展卡尔曼估算器,可通过测量电机电压和电流来提取转子位置的估计值。这些估算器依赖于DSP中足够精确的电机模型的实时计算。通常,这些无传感器算法可以与中等到高速旋转的基于传感器的算法一样工作。但随着电机速度的降低,从电压和电流测量中提取可靠的速度相关信息变得更加困难。通常,无传感器电机控制主要适用于压缩机,风扇和泵等应用,不需要在零或低速下连续运行。
结论
现代DSP三相交流电机的控制在市场上继续蓬勃发展,无论是在成熟的工业自动化市场还是在家用电器,办公自动化和汽车市场的新兴市场。对这些机器进行有效且经济的控制需要在硬件和软件之间进行适当的平衡,以便时间关键的任务(例如PWM信号的生成或转子位置传感器的实时接口)由专用硬件单元管理。另一方面,使用DSP内核的快速计算能力,最好在软件中处理电机的整体控制算法和新电压指令的计算。与旧硬件解决方案相比,在软件中实施控制解决方案具有易于升级,可重复性和可维护性的所有优势。所有电机控制解决方案还需要集成合适的A / D转换系统,以便快速准确地测量电机的反馈信息。 ADC系统的分辨率,转换速度和输入采样结构需要严格针对特定应用的要求。
-
dsp
+关注
关注
553文章
7984浏览量
348687 -
交流电机
+关注
关注
3文章
387浏览量
33613 -
三相交流电机
+关注
关注
1文章
23浏览量
3158
发布评论请先 登录
相关推荐
单相交流电机和三相交流电机的驱动芯片?
什么是三相交流电源对称?对称三相交流电源特征
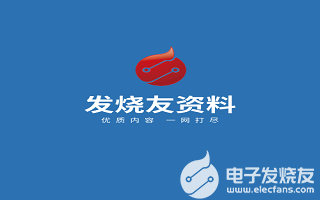
三相交流电机正反转固体控制器的设计
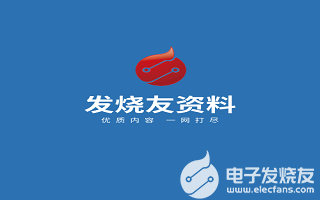
三相交流电的产生问题 三相交流电路和单相交流电路对比分析
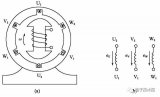
评论