在昨天的文章写完以后,还有个工艺方面的讨论需要仔细拿出来谈一谈,是有关未来EV电池的可维修性的问题。如下图所示,日产在从40kWh=>62kWh是做了挺多的变化。为了把多出来的电芯塞到原有的Pack空间里面,电池的可维修性就做了一些妥协,主要是如下图所示的,焊接和结构上做了交换。
原有的是标准化的模组,可以8个电芯位单元进行替换维修(4个为单元是可以替换的)
现在采用焊接的方式,不同配置的模组都要准备备件,而且内部不可维修
具体的就是类似之前LG和SK普遍使用,单端出Tab的下面,采用Tab焊接到母线牌的方式来完成,如下图所示:
之前的焊接电芯在成组的方式:电芯是采用超声焊接的方式通过小的母线牌往外连接。
因此在这个时候的设计,还是充分考虑可维修性,在端接的特性把连接阻抗放在第二位。
目前的激光焊接方式:更多的是考虑工艺层面的速度和效率,等到实物发布出来我们可以看下是否是之前类似的焊接模式
这里主要的考虑几个事情,在电池顶部的空间使用率
电池之间的阻抗均匀性和整个连接阻抗
还有就是由于电芯增多之后的加工节拍考虑,激光焊接比超声快很多
代价就是这么多电芯就合在一起,走上了和其他软包电芯企业一样的做法
在之前发布的z制造视频里面,是没有涉及这个工艺环节的
我觉得这种结构的改变,等于LG、SK和日产的设计很多细节在之前的分叉之后,使得软包的模组设计方向都开始趋同了。
小结:其实挺好奇下一代日产的纯电动平台方向上,有关于电芯的采用会不会在尺寸和模组设计上会有更大的改进,在NCM的特性上,AESC的电芯的很多问题会和其他企业一样多,简单的模组设计是否有效,还能不能保持自身的安全记录,真的是一个疑问
-
模组
+关注
关注
6文章
1556浏览量
30754 -
激光焊接
+关注
关注
3文章
503浏览量
21202 -
电芯
+关注
关注
14文章
745浏览量
26065
原文标题:LEAF模组的激光焊接
文章出处:【微信号:QCDZSJ,微信公众号:汽车电子设计】欢迎添加关注!文章转载请注明出处。
发布评论请先 登录
相关推荐
激光焊接的优点
为什么说新一代Leaf电池模组是自然冷却方式集大成者
LEAF电池模组演变
ccm模组/vcm激光自动焊接方法的简单介绍
适合摄像头OIS模组焊接的激光喷锡焊接设备
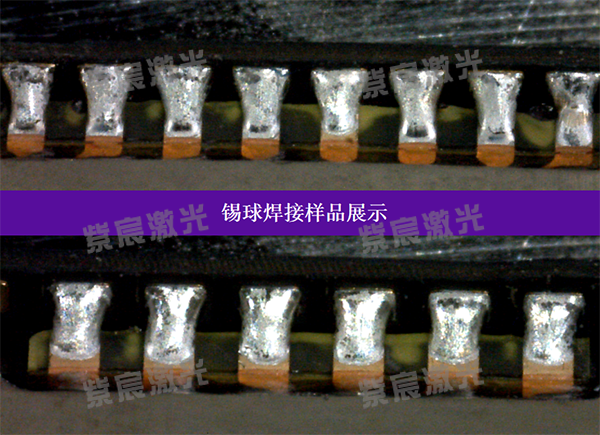
激光焊接:CCM摄像头模组精密制造的核心
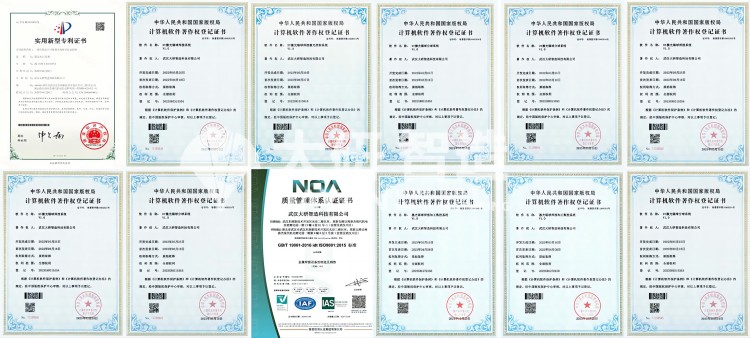
评论