“今天中国有数百家做电动汽车的公司,不缺一家造电动车的,但是,缺一家真正能够解决电动汽车行业最大挑战、尤其是动力电池革命的公司。”
配套43万辆电动汽车,3代动力电池全生命周期验证,9年行驶积累0严重事故。
这是AESC成立12年以来交出的“答卷”,也是远景做出切入电池领域时,“不惜重金”选择收购这家日本企业的核心考量因素。
“今天中国有数百家做电动汽车的公司,不缺一家造电动车的,但是,缺一家真正能够解决电动汽车行业最大挑战、尤其是动力电池革命的公司。”
4月14日,在正式完成对于AESC的收购交割后,远景集团首席执行官、远景AESC董事局执行主席张雷首次接受媒体采访,向外界介绍远景切入电池领域选择收购AESC的原因,并阐释了未来远景AESC的战略发展规划。
▲远景集团首席执行官、远景AESC董事局执行主席张雷
相比于不少跨界涉足动力电池的企业更倾向于对于技术指标和产能规划的“高谈阔论”,远景的布局则将目光紧紧盯在了安全之上,似乎有点“不合时宜”。
高工锂电注意到,在这场长达近两个小时的媒体见面会上,包括张雷在内的几个高管谈论频率最高的一个词,就是“安全”。
这样的关注其实也不难理解,安全是电动汽车动力电池的底线,也自然是任何涉足该领域企业必须要解决的根本性问题,尤其是在高镍化趋势愈演愈烈的浪潮之下,安全提到多靠前的位置都不会“过分”。
而如果再仔细揣摩,你会发现,远景关注的AESC的安全,其实只是其最外在呈现出来的形式,这个结果背后,反映出的这家企业在产品开发、生产制造、产品验证等每个环节近乎固执的“执着”,用张雷的话说,这种日本企业体现出来的“工匠精神”,正恰恰是国内企业所欠缺和不足的。
而这,也正是远景集团紧盯着AESC安全数据背后的深层次原因。
在上海车展举行的远景AESC产品及战略发布会上,张雷再次清晰的表达了这种观点,他表示,目前电动汽车行业主要面临三大挑战:安全,成本,和电网融合,尤其电池安全,是电动汽车行业最大的‘灰犀牛’,而智能化是解决这些挑战的关键。
▲远景AESC产品及战略发布会
张雷向高工锂电表示,在双方的交割和整合完成后,AESC的“安全基因”会和远景多年来在能源物联网领域积累的数据与算法相融合,这种深度结合将会成为远景AESC参与动力电池市场竞争时的“杀手锏”。
按照远景的规划,除了将继续延续AESC电池‘零重大事故’的极致安全,同时,有信心到2025年将电池成本降到50美元/千瓦时。未来,基于远景的智能物联操作系统,电动汽车将成为绿色的移动智能终端,同清洁能源系统有机融合,为碎片化的可再生能源网络提供动态平衡。
零重大事故背后的“秘密”
上海车展前一日,高工锂电在位于上海的远景集团总部,见到了刚刚从日本赶到中国的远景AESC执行副总裁渡边康晴。
在完成交割后,渡边康晴最近的变化除了对外名片加上了“远景”之外,还新增了一个极富挑战的工作:作为远景AESC的日方主导者之一,让AESC“安全”的基因在新建的无锡江阴工厂落地。
当被问及远景AESC如何实现“9年行驶积累0严重事故”背后的安全实现路径上,渡边康晴给出了详细解答。
“安全性是远景AESC的一个核心理念。主要通过两大途径来实现零事故,一个是设计,第二个是生产。”
在设计环节,首先是电芯要确保化学稳定性,要选择稳定的材料,并通过严格评估测试它的稳定性;在模组部分,通过结构来保护电芯免受到冲击。第三个阶段是pack,除了物理上的保护措施,关键是要通过BMS对电芯模组进行故障诊断,监测异常发生,并预测可能出现的问题,从而对问题进行管控。
渡边康晴介绍,在整个设计环节当中,其有一个整体思路是,材料、电芯、模组不同环节针对设计的要求不断探寻其边界和极限,并通过找到的极限,在各个领域来设定域值。
而在制造环节,远景AESC先从设计当中提取出监测项目,然后在制造环节当中再设定重要管理项。据悉,在远景AESC制造设定的重要管理项目中,一个电池包里涵盖的管理项目达770项以上。在实际的制造中,再根据上述项目做彻底完善的管理。
▲远景AESC首席执行官松本昌一
与此同时,远景AESC首席执行官松本昌一还现场介绍,针对于制造环节的重要监测管理数据,AESC会进行不断的追溯和追踪,一旦发现不良或者故障,就会及时对于工序进行调整修改,以此实现制造过程中的优化与提升。
远景AESC提供的数据显示,截至目前,其已经在设计和制造上拥有的技术专利超过2000个,覆盖电化学技术,电池工艺和结构设计,热平衡和能量管理电池包开发等方面。而也正是这笔庞大的专利资产,为其动力电池的安全可靠保驾护航。
正是基于设计与制造的结合,再加上长期基于整车上的测试与验证,成为AESC过去几年里实现高度安全的“秘钥”。
AIoT赋能动力电池技术
事实上,对于松本昌一和渡边康晴而言,将已经成熟的经验通过原有的团队管理和运营,进行体系化的输出,快速的复制到中国项目,这并非难事。
新的挑战在于,这个位于无锡江阴的项目,将会基于最近几年的开发积累,准备量产新一代Gen5 – 811体系的电池,高镍体系之下,如何在原有经验的基础上,在产品开发验证速度上和效率上做进一步的提升,并能保证其在安全性和此前保持一致,考验着中方和日方团队的智慧。
▲远景AESC新一代Gen5–811体系电池
▲远景AESC新一代Gen5–811体系电池
这时,远景集团在数据算法以及能源管理领域积累多年的经验就派上了用场。
张雷的思路是,通过AI算法和物联网的思路,一方面会对于电池的安全起到提升作用,还能在降本、未来电池的梯次利用等环节发挥更大的作用。
事实也的确在朝着张雷构想的这个方向前进。
据了解,在远景AESC成立后,其将会为智能互联网中每一个电池模组加载芯片,进行电池工作模组工作状态的监测,并预防危险的发生。
同时,基于远景AESC 9年行驶数据积累,通过AI算法优化原材料配方,数字化解构电池使用工况,大数据分析每个失效的机理,作为 AIoT 数据的输入端。
远景AESC 还在利用电化学仿真优化加速电芯设计节奏,预测不同工作环境下的电池表现,在提升研发效率,缩短开发周期的同时,促进新一代产品研发。
值得关注的还有,远景AESC还在用物联网技术,优化动力电池全生命周期管理,统计建模,预测表征电池可靠性和寿命,最大程度简化电池检测筛选工序,降低成本,解决退役的动力电池组在拆解、检测、分类、二次成组中的技术、安全和经济性等痛点。
在制造环节,远景AESC江阴工厂为解决传统动力电池生产中存在的效率低、误差大、三废高等问题,通过智能识别与处理技术,全面防止异物污染及湿气滲入等主要电池生产安全隐患,以此实现了智能物联网与制造的结合。
全球动力电池格局未来变量
技术赋能的同时,远景AESC在中国的落地,还在通过本土供应链的导入,为接下来成本的降低做准备,远景AESC执行董事及中国业务负责人赵卫军表示,中国的锂电供应链已经在逐步实现国际化,无论是在材料还是在设备领域,都已经能达到国际水平,且性价比优势明显,未来,本土供应链的导入将会让远景AESC参与市场竞争时更具优势。
在产能布局上,按照规划,位于无锡江阴的中国基地三期拟建总年产能达20GWh,一旦建成,将成为远景AESC全球最大的生产基地,这背后透露出的信号是,对于将要参与全球动力电池市场竞争的远景AESC而言,只有快速落地中国,建立规模化优势,才可能更快的获得市场认可。
高工锂电通过与中日双方的交流,感受最为明显的一点是,双方对于彼此价值观的认同,以及对于正在进行的整合的配合与期待。
对于“野心勃勃”的远景而言,其不仅希望通过”日本工匠精神“与“中国高效率低成本的运营效率和供应链优势”、AESC的电化学积累和远景的物联网及算法互补结合,来大踏步进入动力电池领域,并还将进一步突破动力电池性能与应用边界,打造更多V2X智能场景,让电动汽车参与将来碎片化的可再生能源系统,通过掌握未来的“新石油”打造自己的能源物联网版图。
而对于像松本昌一、渡边康晴为代表的日方高管团队而言,其似乎也急于摆脱过去,希冀通过来自全球最大电动汽车市场的资本、资源、市场,来重新回到舞台中央。
正是这种双方之间的期待与共识,或许将会让远景AESC成为国内乃至全球动力电池市场格局中的重要变量。
-
电动汽车
+关注
关注
156文章
12080浏览量
231202 -
动力电池
+关注
关注
113文章
4534浏览量
77639
原文标题:【大族激光•高工特写】远景AESC重返 “舞台中央”
文章出处:【微信号:weixin-gg-lb,微信公众号:高工锂电】欢迎添加关注!文章转载请注明出处。
发布评论请先 登录
相关推荐
大核桃防爆气体检测终端确保高危气体场景“零事故、零伤害”的安全目标
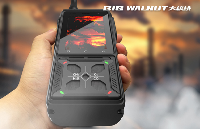
零重力飞机工业完成A+轮融资
欧姆龙保护协调方案提高装置安全对策
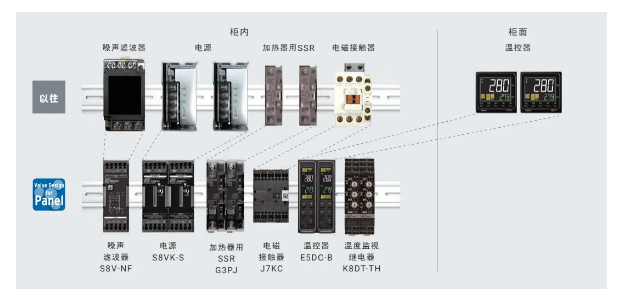
武汉凯迪正大分享电缆隐患排查治理:安全生产的基石
努比亚发布自主研发的星云大模型,在AI技术领域又一重大突破
XKCON祥控防爆型筒仓安全监测系统能够对筒仓进行7x24h长期在线监测
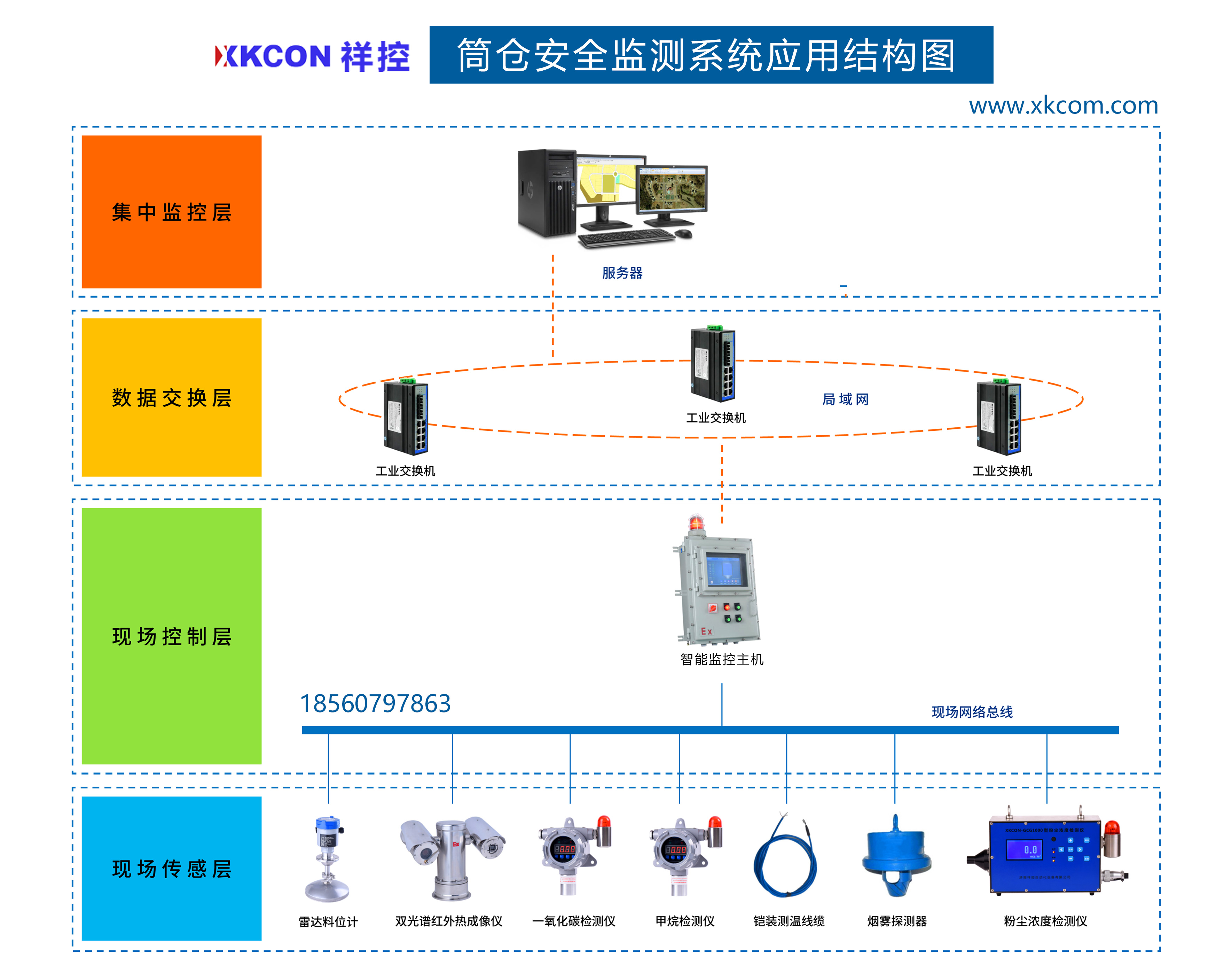
水电站关键螺栓在线监测预警系统解决方案
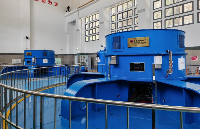
秘密背后的秘密-高速PCB的层叠确认时,工厂为何不写铜箔类型
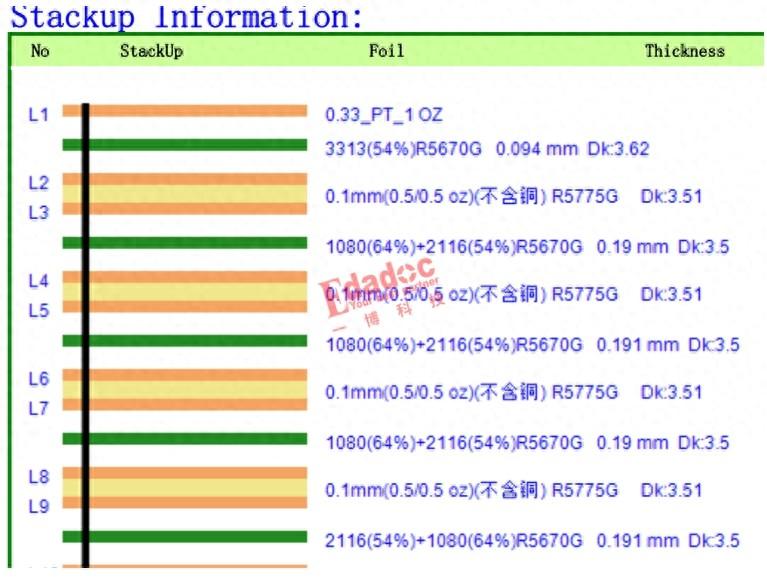
秘密背后的秘密-高速PCB的层叠确认时,工厂为何不写铜箔类型
谷东科技大模型应用方案荣获深航飞机维修AI+应用创新大赛第二名
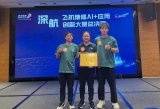
螺栓预紧力在线监测系统解决方案及实用案例
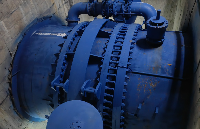
评论