电子产品制造的微小型化和利润的日益缩水,使电子制造企业正面临着较大的生存和发展压力。对一个新产品来说,产品的成本和开发周期是决定这个设计成败的关键因素。业界研究表明,产品设计开支虽一般只占产品总成本的约5%,但它却影响产品整个成本的70%。为此,搞好成本及质量控制,在新产品设计的初期,针对产品各个环节的实际情况和客观规律,须全面执行最优化设计DFX(可制造性\成本\可靠性\装配性)方法。企业在管理上,对设计工作务须规范;对相关技术管理人员的培训、辅导和约束,不可或缺。
PCB/PCBA的可制造性和可靠性设计的提出有效的提高了电路工业设计的工艺水平,然而由于对PCB/PCBA的可制造性和可靠性设计的研究还缺少相对比较成熟的理论,所以在PCB/PCBA的可制造性和可靠性设计中还存在一些人为因素和技术上的问题,剖析问题的成因,提出有效的实现PCB/PCBA可制造性和可靠性设计的改进举措具有非常重要的意义在对具有可制造性能的PABC设计时要遵循的原则有以下几种。
1.以PCBA装配而为对象,整体考虑封装尺度与引脚间距:对整板工艺性影响最大的是封装尺度与引脚间距。在选择表面组装元器件的前提下,必须针对特定尺寸与组装密度的PCB,选择一组工艺性相近的封装或者说适合某一厚度钢网进行焊膏印刷的封装。比如手机板,所选的封装都适合于用0.1mm厚钢网进行焊膏印刷。
2.优选表面组装与压接元器件表面组装元器件与压接元器件,具有良好的工艺性。随着元器件封装技术的发展,绝大多数元器件都可以买到适合再流焊接的封装类别,包括可以采用通孔再流焊接的插装元器件。如果设计上能够实现全表面组装化,将会大大提高组装的效率与质量。
压接元器件主要是多引脚的连接器,这类封装也具有良好的工艺性与连接的可靠性,也是优先选用的类别。
3.整体考虑焊盘、阻焊与钢网开窗的设计焊盘、阻焊与钢网开窗的设计,决定焊膏的实际分配量以及焊点的形成过程。协调焊盘、阻焊与钢网三者的设计,对提高焊接的直通率有非常大的作用。
4.研究案例完善设计规则:可制造性设计规则来源于生产实践,根据不断出现的组装不良或失效案例持续优化、完善设计规则,对于提升可制造性设计具有非常重要的意义。
5.缩短工艺路径:工艺路径越短,生产效率越高,质量也越可靠。
6.优化元器件布局:元器件布局设计主要是指元器件的布局位向与问距设计。元器件的布局必须符合焊接工艺的要求。科学、合理的布局,可以减少不良焊点和工装的使用,可以优化钢网的设计。
7.聚焦新封装:所谓新封装,不完全是指新面市的封装,而是指自己公司没有使用经验的那些封装。对于新封装的导人,应进行小批量的工艺验证。别人能用,不意味着你也可以用,使用的前提必须是做过试验,了解工艺特性和问题谱,掌握应对措施。
SMT贴片加工技术要点
1、元件正确——要求各装配位号元器件的类型、型号、标称值和橱极性等特征标记要符合产品的装配图和明细表要求,不能贴错位置。
2、压力(贴片高度)——贴片压力(高度)要恰当合适,元器件焊端或引脚不小于1/2厚度要浸入焊膏。对于—般元器贴片时的焊膏挤出量(长度)应小于0.2mm,对于窄间距元器件贴片时的焊膏挤出量(长度)应小于0.1mm.
3、位置准确——元器件的端头或引脚均和焊盘图形要尽量对齐、居中。元器件贴装位置要满足工艺要求。因为两个端头Chip元件自定位效应的作用比较大,贴装时元件长度方向两个端头只要搭接到相应的焊盘上,宽度方向有1/2搭接在焊盘上,再流焊时就能够自定位,但如果其中一个端头没有搭接到焊盘上,再流焊时就会产生移位或吊桥:而对于SOP、SOJ、QFP、PLCC等器件的自定位作用比较小,贴装偏移是不能通过再流焊纠正的。
二、SMT贴片加工如何防止桥连
第一:提高助焊剞的活性
第二:提高焊料的温度
第三:提高PCB的预热温度,增加焊盘的湿润性能
第四:使用可焊性好的元器件/PCB
第五:去除有害杂质﹐减低焊料的内聚力﹐以利于两焊点之间的焊料分开。
SMT贴片加工是目前电子行业中最常用的表面贴装技术,正确掌握贴片加工方法,避免不良焊接方式的出现,不仅可以提高产品质量加快工作效率,还可以避免不必要的浪费与损失,节约成本。
-
pcb
+关注
关注
4322文章
23124浏览量
398521 -
元器件
+关注
关注
112文章
4726浏览量
92485 -
封装
+关注
关注
127文章
7941浏览量
143093
发布评论请先 登录
相关推荐
微流控芯片中的CNC加工技术
精密与超精密加工技术的发展趋势
SiC单晶衬底加工技术的工艺流程
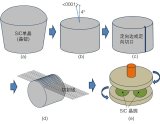
组合逻辑电路设计时应遵循什么原则
轧辊激光熔覆修复加工技术
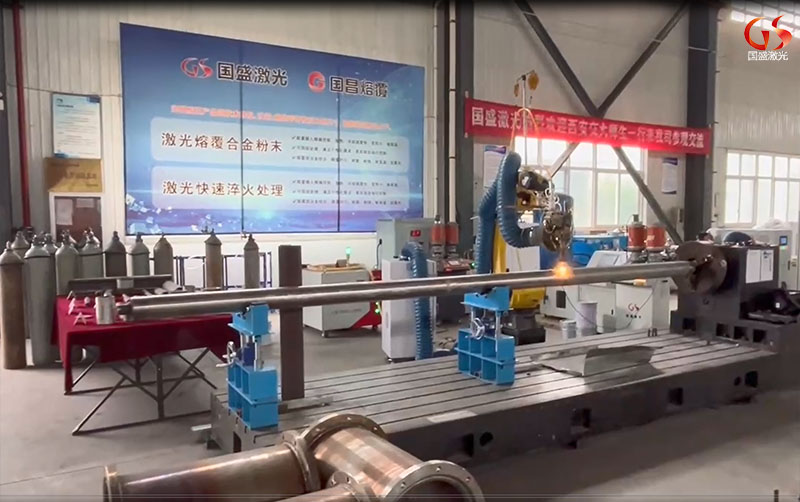
数控加工工艺处理的原则和步骤是什么
信号分析和信号处理必须遵循的原则
会议回顾 | Aigtek第四届全国超声加工技术研讨会高光时刻!
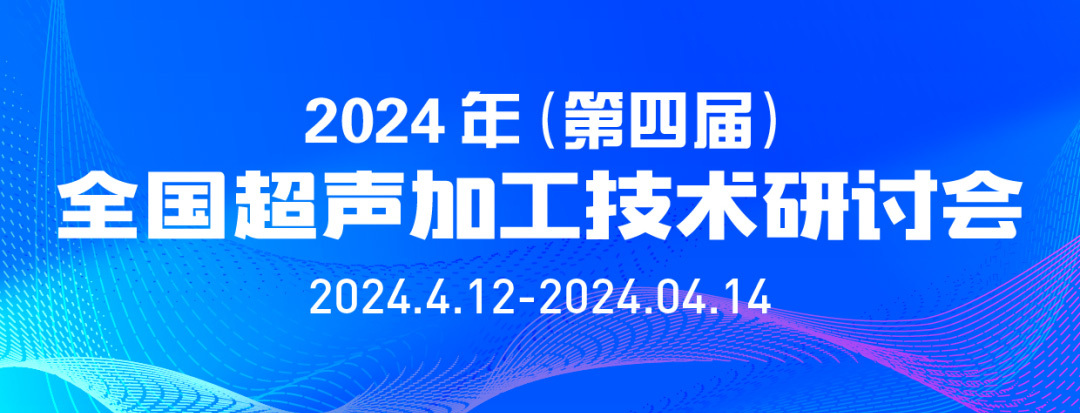
会议回顾 | Aigtek第四届全国超声加工技术研讨会高光时刻!
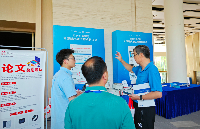
电路仿真所遵循的基本原则是什么
SMT贴片加工锡膏使用注意事项
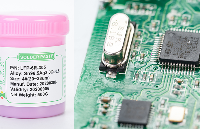
评论