数字孪生体(Digital Twin)是一个较新的概念,目前它主要被行业人士应用到较为抽象的描述中,例如,美国工业互联网联盟(IIC,Industrial Internet Consortium)和开源工业互联网联盟(Openii Consortium)都对数字孪生体比较关注。
按照工业4.0研究院数字孪生体研究中心(DTRC,Digital Twin Research Center)设计的数字孪生体系(DTS,Digital Twin System),它主要分为物理孪生体(PT,Physical Twin)和数字孪生体(DT,Digital Twin)。
本文尝试对机床领域的数字孪生体应用做一定分析。
在学术研究领域,Altintas等人对机床领域的数字化研究比较深入,不仅涉及到虚拟机床(Virtual Machine Tool),还涉及到虚拟加工(Virtual Machining),这两个部分是数字孪生体在机床领域的核心应用。
机床的数字孪生体应用示例
对于虚拟机床的情况,2005年Altintas在CRIP上发布了Virtual machine tool一文,对相关领域进行了深入的论述。后续不少商业软件对相关场景进行了开发,形成了完整的商业软件解决方案,例如,MATLAB、ANSYS等软件都提供相关功能。
接着在2014年,Altintas在CRIP上发布了Virtual process systems for part machining operations,阐释了虚拟加工的多种场景,包括切削力、扭矩、驱动、稳定度和震动等指标。目前的现状是,各种应用对于机械加工的场景进行了较好的数字化,但还缺乏单一的系统来实现所有解决方案。
ECOMATION提供的能源数字孪生体管理
除了Altintas关注的虚拟加工和机床,数字孪生体还可以在机床生命周期方面发挥作用,例如,能源消耗管理、部件的生命周期等,机床领域的专家进行了详细的研究,欧盟也对相关项目进行了支助,例如,ECOMATION、ESTOMAD(Energy Software Tools for Sustainable Machine Design)等。
与国内系统级的解决方案不同,ECOMATION的解决方案从机床到部件级别的能源消耗都有跟踪,形成了真正的数字化解决方案。据工业4.0研究院观察,德国宝马公司、戴姆勒等汽车企业就在做类似的能源管理应用。
Mikel Armendia、Aitor Alzaga等人针对机床的数字孪生体应用撰写的论文表示,之所以采用数字孪生体来对机床进行管理,是因为随着机床数字化程度加深,传统的管理办法不太有效,特别是信息物理系统(CPS,Cyber-Physical Systems)的方法。
数字孪生体可以获得机床和使用过程的全方位信息(holistic information),这使得工业大数据的应用成为可能,简单地讲,机床领域的数字孪生体应用具有以下好处:
1. 通过对实际机床的监测获得数据反馈,可以不断优化数字孪生体,简单地讲,数字孪生体可以结合到物理孪生体反馈回来的数据进行系统级别的改进。
2. 通常情况下,生产系统的部署花费的时间会影响产品的上市时间,如果应用数字孪生体,可以实现所谓虚拟委托(virtual commissioning),这样的做法可以减少装备系统的部署时间。
3. 在对设备进行保养修理等过程中,数字孪生体可以用来提升设备健康管理能力,利用大数据对虚拟设备(数字孪生体)进行训练,从而提升物理孪生体的应用效果。
4. 通过把数字孪生体集成到控制系统中去,从而更为方便优化机床的性能。
工业4.0研究院数字孪生体研究中心通过过去两年时间的研究,得出了与Mikel Armendia等人类似的结论,那就是在机床领域的数字孪生体应用,缺乏统一的思路和方法,主要以非标的个性化试验为主,国内一些参与机床或生产现场数字孪生体应用的案例,也大都如此。
接下来要进一步推进数字孪生体在机械或机床领域的应用,应该尽量系统化一些,不应该只停留在试验或可控的环境,这样才可能有较大的突破。
-
机床
+关注
关注
1文章
585浏览量
30290 -
工业互联网
+关注
关注
28文章
4323浏览量
94168 -
数字孪生
+关注
关注
4文章
1331浏览量
12279
原文标题:机床领域的数字孪生体应用及实践简介
文章出处:【微信号:openiiconsortium,微信公众号:数字孪生装备】欢迎添加关注!文章转载请注明出处。
发布评论请先 登录
相关推荐
数字孪生对工业4.0的影响
数字孪生在智能建筑中的使用
数字孪生与物联网的结合
什么是数字孪生?它有哪些优势?
基于数字孪生的智慧城市
什么是数字孪生
数字孪生:当数字科技遇上现实世界
数字孪生关键技术及体系架构
2024 ETAP 电气系统数字孪生平台技术研讨会(深圳站)
从理论到实践:数字孪生技术的全面应用探讨
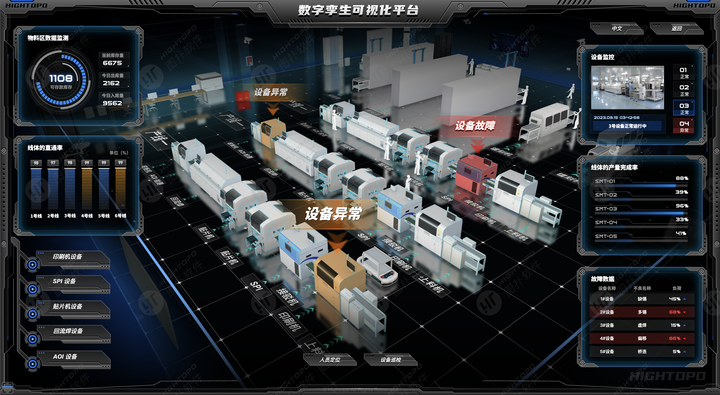
评论