颠覆性创新技术不但是投资者追逐的风口,更是实业者努力创造的现实。走过130年创新路,ABB继续在数字化浪潮中御风而行,通过自有实验室实现了众多技术突破,同时携手新兴科技领域全球翘楚,致力于开放式创新。
人工智能、深度学习、边缘计算、数字孪生、Factory 2.0……热词频现,数字化技术与各行业的交汇将产生什么化学反应?数据与算法将如何赋能新制造,重新定义未来工厂?近期,我们将集中介绍ABB最新的科研成果和应用案例,跟我们一起来探寻这些热词背后的真相吧!
今天,人工智能已然成为智能制造、工业互联网大潮中的热门话题,人们赋予了人工智能非常多的期望。然而,人工智能必须要与人的经验结合才能最大程度发挥效能,工业领域的人工智能更是如此。工业生产往往由机械-电气-工艺构成复杂系统,变量多、系统机理复杂相互影响。因此,如何将人工智能的算法与模型和工业现场的应用场景相结合,这个需求本身就是一项创新。如何通过简单方法解决现实问题也是评估创新性的关键一环。机器学习作为人工智能最为重要的内容之一,是解决工业问题的有效方法。
当很贵的「单晶硅」
遇上很累的「多线切割机」
中国是全球最大的晶硅电池组件制造国。
单晶硅电池在长晶、切方后会进入切片工序。在这个工序里:放线轮的钢丝线会经过四个轴绕线(超过3000圈)然后被牵出,经过切方的晶棒会被放于其上;随后,通过在钢丝线上加载石英砂研磨材料将晶棒切为单片的晶片,然后通过后道的清洗、制绒、刻蚀、减反射膜(PECVD)等工序,并经过层压敷设等组装工序成为光伏组件,提供电力供应能力。
多线切割机是生产晶硅电池最为重要的设备,每天都处于连续工作状态,属于负荷非常重的生产设备,它的稳定性及可靠性会直接影响到工厂的产能和产品质量。众所周知,单晶硅棒材价格昂贵,因此如何提高多线切割机的健康预测至关重要。在生产切割过程中,若因为机器故障导致切割出废品,那么硅棒损耗、停机及人工成本带来的损失将非常高。
多线切割机机械结构简图
青岛高测科技股份有限公司(以下简称高测)是国内领先的光伏设备制造商,在过去数年里发展迅速,装机量大幅提升。为了更好地提升用户体验与服务效率,高测在原有基于状态监测的维护之上开发了基于机器学习的预测性维护模型。
「预测性维护」
挑战重重
预测性维护并非是一种全新的设备维护解决方法,在过去的数十年里,它已经被应用于航空发动机、大型鼓风机等诸多领域。
由于采用专用的分析模型,这些预测性维护往往需要对机械失效模型进行深入的研究,而且通常需要配备非常专业的维护人员。维护航空发动机这样的重值设备,尚可以承受高昂的维护价格;但对工业装备而言,这个方法往往经济性不足,并且航空发动机领域的相关知识不易于移植到其它行业,每个垂直的领域都有非常特殊的工况以及系统运行机制。
「数字驱动」
为设备提供稳定保障
数字驱动的机器学习的不断发展,让不依赖于机器固有复杂建模基础上的预测性维护成为可能,通过数据分析对潜在风险进行评估和预测,为设备提供稳定可靠的保障。
/无需额外硬件支持/
高测多线切割系统采用贝加莱的Panel PC作为控制系统。Panel PC是一款集成控制系统,可以将PC的强大计算能力、PLC实时控制能力和Windows丰富的HMI开发能力融为一体。因为具有开放的算法支持能力,该系统仅需在现有硬件和软件平台基础上进行机器学习算法设计,而无需额外配置一套专用的机器学习系统或其它类似AI加速器等硬件。原系统本身就提供了对牵引轴的温度点检测,四个驱动轴分别配有温度检测模块提供采样输入。
多线切割系统软硬件配置架构
/自定义的算法/
非监督式学习的经典算法经实验无法满足该应用场景的需求,因此工程师们需要自定义一种非监督式学习算法,更有针对性地解决该系统问题。得益于Automation Studio平台的开放能力,工程师们可以自定义机器学习算法。
工程师们选择了基于特征提取的非监督学习模式来开展学习过程。在这个系统中,工程师们在众多的参数中(包括电流、电压、温度、速度、位置)中选择了4个轴承温度作为测量点,构建了温度相关特征提取的策略。这是机器学习算法设计的重要一环,即必须确保数据的有效性和内在关联性。
在此基础上,对这些参数进行了适当的算法处理,并获得温度残差,即,温度的斜率 -均值(斜率的均值)得到残差,然后系统对残差数据进行基于以下三个目标参数的学习,寻找其最优值:
1.检测滑动窗口:W(秒)
2.发散水平阈值: α
3.比例阈值:β
通过大量数据的学习(超过20GB数据),以获取W, α, β的最优组合。
衡量系统效果的关键指标在于“检出率”与“误报率”,这两个参数通常成对出现。在设计算法时,追求检出率则会导致阈值设置比较低,误报率就会提高,因此需要通过设置合适的阈值以寻求最优的故障预测。通过在15台机器上数千刀的裁切过程,在检出率90%的情况下,预测性维护系统仅有0.2%的误报率,达到了超预期的学习效果和非常高的投资回报率。
创新就是要在最小投入下获得最大产出。该系统无需额外硬件资源投入而达到极高的预测效果,充分体现了人的智慧与机器的学习完美结合。
▲理论解析▲
Gartner的分析师Carlton在2017年对机器学习架构进行了阐述。简单的说,机器学习正如下图所示,通过输入数据,由学习系统对数据进行处理,并达到数据输出。这里不同的数据包括结构性和非结构性数据。考虑到现实数据源的复杂性,需要对数据进行预处理,进入的数据才可以被学习系统识别。学习系统会借助各种不同的监督或非监督学习算法来处理数据,并生成各种应用结果,例如预测、分类等应用。
机器学习就其原理而言,并非想象中那么高深。机器学习要解决的是一种较为“确定”的应用,但是对于很多机器的控制工艺而言,往往更依赖于人的经验,而人的经验差别较大且不确定性较高。另外,人的经验在遇到新的工艺时候也需要学习和验证。机器学习试图建立一种适应变化的能力,让不同工况下的控制实现工艺最优化。
因此,机器学习在某种意义上来说就是“授人以渔”,而传统模型则是“授人以鱼”。
机器学习包括了监督学习、非监督式学习和强化学习。监督式机器学习主要任务通过机器学习模型和已有信息,对感兴趣的变量进行预测,或者对相关对象进行分类。常用的监督式机器学习有随机梯度、朴素贝叶斯、支持向量机、神经网络、决策树等。非监督式学习是在没有先验知识或信息缺乏的情况下,对数据集的规则进行自学习,主要应用是聚类,主要算法包括K-means、近邻算法、高斯混合模型等。强化学习旨在通过对实际事件得到观察得到行为优化的结论,目前强化学习暂时主要停留在学院派研究中。
未来工业应用场景分析
预测性维护
通过数据(温度,流量,电流,加速度等)监测过程并预测其预期行为的区域,以检测设备故障或生产错误。在传统应用中,我们使用固定阈值,并在物理值超过阈值时生成警报,这种方法需要非常专业的机械模型和失效分析,并对人员专业度要求极高。而通过数据驱动的机器学习方法,可以通过大量的数据采集和学习来实现对故障的预测,在对机器造成不可逆转损坏或重大生产损失之前更好地识别潜在故障。实际应用可以是非常通用的:从注塑机到风力发电机组到过程自动化。
示例主要涉及机器人技术(拾取,放置和分拣)领域,在其他一些专业验证和测量过程中也是如此,目前的视觉算法还无法轻易解决这些问题。
视觉分析是机器学习常用场景(图片来自网络)
机器视觉是最为普遍的工业检测应用,可以通过视觉系统对生产线的加工对象进行检测。相较于传统的依靠人工经验长期积累的机器视觉方案而言,采用机器学习方法可以通过学习构建对产品的分类、定位、识别、缺陷分析等应用场景更为灵活、适应更广且更为经济的方案,并且通过与控制系统的通信也可以实现视觉与机器运动、逻辑的同步。
设备预测性维护相关的振动传感器信息
视觉缺陷监测的学习与预测
生产质量影响因素分析
优化
优化的目的在于提高控制质量如响应速度与精度。机器学习可以消除人类专家微调模型参数(机器动力学,风力涡轮机定向,卷筒张力)的需要,以便最大化奖励:输出生产、过程精度、功率提升。应用程序可应用于任何区域,由于需要与机器进行有效的交互,因此需注意安全限制。
控制
控制是目前大部分研究所关注的一个复杂领域,其目标是让机器学习算法在没有任何先前知识的情况发现流程的控制策略。涉及许多变量并且没有可用分析解决方案的复杂过程(例如电网管理,供应链,化工厂等)可以尝试这种方法。
当然,就目前阶段而言,机器学习必须与人的智慧和知识进行紧密结合,才能更好地发挥效果。
-
ABB
+关注
关注
26文章
525浏览量
52777 -
机器学习
+关注
关注
66文章
8422浏览量
132742
原文标题:热词科普 | 「机器学习」在单晶硅切割工艺中的应用
文章出处:【微信号:ABB_in_China,微信公众号:ABB中国】欢迎添加关注!文章转载请注明出处。
发布评论请先 登录
相关推荐
天水华天传感器CYB系列单晶硅与无线压力变送器产品介绍
东芝 BiCD 单晶硅集成电路TB6560AHQ/AFG规格数据表
非晶硅太阳能电池技术原理与应用
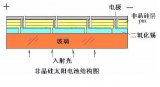
单晶硅压力变送器和扩散硅的区别
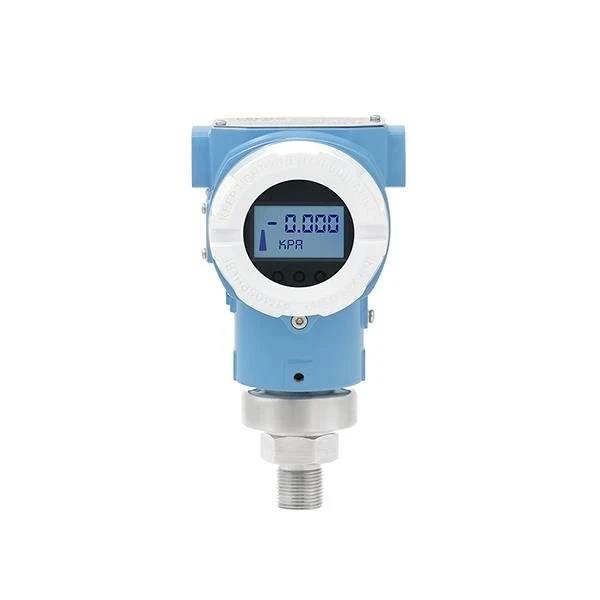
晶棒切割工艺流程及注意要点
芯片制造工艺:晶体生长基本流程
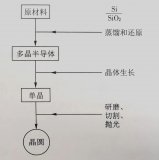
评论