科学技术的不断进步使现代社会与电子技术密切相关。对手机,便携式计算机,存储器,硬件驱动器,CD-ROM驱动器,高分辨率电视等电子产品的小型化和轻量化提出了严格的要求。为了获得这样的目标,必须在制造方面进行研究。技术和组件。 SMT(表面贴装技术)符合这一趋势,为电子产品的小型化奠定了坚实的基础。
20世纪90年代SMT步入成熟阶段。然而,对电子组装技术提出了更高的要求,电子产品迅速向便携性,小型化,网络化和多媒体发展,其中BGA(球栅阵列)封装是一种步入实用阶段的高密度组装技术。焊点质量在确定SMT组件的可靠性和性能方面发挥着至关重要的作用,BGA焊点质量应该集中在其上。因此,本文将提供一些有效的措施来保证BGA元件的焊点质量,从而实现SMT组件的最终可靠性。
BGA简介封装技术
BGA封装技术早在20世纪60年代就已开始,并由IBM公司首次应用。然而,BGA封装技术直到20世纪90年代初才进入实用阶段。
早在20世纪80年代,人们就对电子小型化和I/O引脚数量提出了更高的要求。尽管SMT具有小型化特性,但对高I/O引脚数和精细间距元件以及引线共面性提出了更严格的要求。然而,由于制造精度,可制造性,成本和组装技术方面的限制,QFP(四方扁平封装)元件的极限间距为0.3mm,限制了高密度组件的发展。此外,由于细间距QFP组件要求对组装技术提出严格要求,这使得它们的应用面临限制,组件制造商转而使用比QFP组件更有优势的BGA组件上的R& D。
细间距元件的局限在于它们的引线容易弯曲和断裂并且易受损坏,对引线共面性和安装精度提出了很高的要求。 BGA封装技术利用了一种新的设计思维模式,即圆形或圆柱形焊球隐藏在封装下方,因此引线间距较大,引线较短。因此,BGA封装技术能够解决通常在细间距元件上产生共面性和翘曲的问题。
因此,BGA元件的可靠性和SMT组件性能优于普通SMD(表面贴装器件)。 BGA元件的唯一问题在于它们在焊点测试方面的难度,难以保证质量和可靠性。
BGA元件焊点问题
到目前为止,可靠的电子装配器,例如PCBCart,BGA元件焊接缺陷通过电子测试暴露出来。在BGA组件装配过程中控制装配技术过程质量和确定缺陷的其他方法包括浆料筛选,AXI样品测试和电子测试结果分析。
满足质量评估要求是一项具有挑战性的技术,因为在包装下拿起测试点很困难。在BGA元件缺陷检测和识别方面,电子测试通常是无法进行的,这在一定程度上增加了缺陷消除和返工的成本。
在BGA元件缺陷检测过程中,电子测试只有在连接BGA组件后才能判断电流是打开还是关闭。如果实施非物理焊点测试作为辅助,则有利于装配技术过程和SPC(统计过程控制)的改进。
BGA元件装配是一种基本的物理连接技术过程。为了能够确认和控制技术工艺的质量,必须知道并测试物理元件,以影响其长期可靠性,例如焊膏体积,引线和焊盘的对准以及润湿性。否则,根据电子测试产生的结果进行修改是令人担忧的。
BGA组件检查方法
它是对于测试BGA元件焊点的物理特性非常重要,并确定在技术工艺研究期间如何始终如一地为装配过程中的可靠连接做出贡献。所有测试提供的反馈信息都与每个技术过程或焊点参数的修改有关。
物理测试能够标记焊膏筛选的情况变化和BGA组件连接的情况在回流焊接过程中。此外,它还可以展示同一电路板和板上所有BGA组件的情况。例如,在回流焊接过程中,极端湿度会随着冷却时间的变化而变化,这可以反映在腔体数量和BGA焊点尺寸上。
事实上,对于BGA元件组装的整个技术过程,没有那么多的检测设备可以进行精确的测量和质量检测。自动激光检测设备能够在元件安装之前测试焊膏印刷情况,但它们以低速运行,无法对BGA元件进行回流焊接质量检测。
X射线检测应用了器件,焊盘上的焊膏表示阴影图像,因为焊膏位于焊点上方。对于不可折叠的BGA组件,由于前置的焊球,也可以看到阴影,这肯定使得难以确定。这是因为焊膏或前置焊球引起的阴影效应阻止了X射线检测设备的工作,这些设备只能粗略地反映BGA封装的工艺缺陷。此外,外围检查还面临着由于污染物导致的焊膏或开路不足等挑战。
横截面X射线检测技术能够克服上述限制。它可以检查焊点的隐藏缺陷并显示BGA焊点的连接。
BGA焊点的基本缺陷
•开路电路
由于焊盘污染,不可折叠的BGA焊点始终会出现开路。由于焊膏无法使PCB(印刷电路板)上的焊盘润湿,因此它将通过焊球爬到元件表面。如上所述,电子测试可以确定开路,但无法区分开路是否由焊盘污染或焊料筛选缺陷引起。 X射线检测设备也不能指示开路,这是由于前置焊球的阴影效应造成的。
截面X射线检测技术能够捕获焊盘之间的切片图像。组件,然后由于污染物确认开路。因为由于污染物引起的开路产生精细的焊盘直径和相对大的部件直径,所以可以使用部件直径和焊盘直径之间的差异来确定是否由于污染而发生开路。至于焊膏不足导致的开路,只有横截面检测装置可以制造。
•Void
由于流动的蒸汽滞留在低共晶点的焊点处,因此会产生可折叠的BGA元件焊接。空隙可被视为可折叠BGA组件发生的主要缺陷。在回流焊接过程中,由于空隙引起的浮选聚焦在元件表面上,因此大部分焊点失效也发生在那里。
通过预热和增加可以消除空隙问题回流焊接过程中的瞬态预热时间和低预热温度。一旦空隙超过一定的尺寸,数量或密度范围,可靠性肯定会降低。然而,另一所学校认为空隙不应受到限制,但应加速其破裂和扩展,以便尽快发现它们失败并消除。
-
BGA
+关注
关注
4文章
543浏览量
46796 -
PCB打样
+关注
关注
17文章
2968浏览量
21690 -
华强pcb线路板打样
+关注
关注
5文章
14629浏览量
43022
发布评论请先 登录
相关推荐
BGA焊点空洞的形成与防止
BGA焊点虚焊原因及改进措施
BGA焊接的工作原理、焊点检查和返工程序
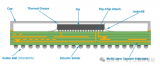
评论