随着大功率电子元件对PCB散热能力的要求越来越高,市场对金属基板的需求也是水涨船高,同时对铜基板产品也提出了更高的加工要求。尤其是钻孔方面,越来越多的铜基板要求钻0.5mm以下的通孔,若按常规钻孔方式加工极易出现断刀报废的情况。本文将通过对铜基板钻孔机理的研究,提出一些改善钻孔工艺的方案,从而提升铜基板小孔的加工良率。
铜基板钻孔加工的难点分析
由于客户对散热或制板的需求较为多样,市面上用于铜基板的铜材料也有多种,而不同种类的铜基板其硬度也不一样。目前主流的铜基板所用材料为铜含量较高的紫铜,紫铜的特点是塑性较好以及强度、硬度稍低,其散热性能是各类铜基板中最好的。从PCB钻孔加工的角度来看,铜块同时兼有“硬”和“软”两方面的特点[1]。一方面铜块比FR-4等有机材料或有机复合材料硬很多,钻刀加工时切削难度大大增加,容易磨损过度导致断刀;另一方面铜块具有一定塑性,钻孔过程可能会使铜屑粘附刀头,如下图1所示,容易出现切屑不良导致断刀。尤其当钻孔的刀径小于0.7mm时,能承受的横向切削力和轴向力都很有限,褪屑能力又很弱,这对钻孔的挑战非常大。
图1 钻头粘铜
钻头的选择
上述展示当前铜基板小孔加工过程中存在的几个主要问题:磨损大、易断刀、散热难。尽管这些问题令人头疼,但通过选择适当的钻头却能够有效地缓解这些状况,从而改善铜基板钻小孔的方方面面。
✪钻刀易磨损问题的解决方案
首先是磨损大的问题,从硬度的角度来看,铜块比常规的板材要硬得多,这就决定了同样的钻刀对这些材料加工,必然是硬的铜块对钻刀磨损较大。为了提升钻刀的寿命,这就需要强化钻刀的耐磨损性能。现有的高速钢或硬质合金钻刀,尽管硬度偏低,然而其材质强度已经很高,具有良好的机械加工性能。因此在提升耐磨度这方面,业界的普遍做法并非更换钻刀材质,而是在现有钻刀上增加涂层[2],从而达到提高刀具表面硬度、减小摩擦系数、降低切削温度的目的,硬质合金与各种涂层技术的硬度对比如下表1所示。
表1 硬质合金与各种涂层技术的技术对比
可见添加涂层的刀具其表面硬度有所提升,使得产品的耐磨性能也大大提升,而摩擦系数降低也有利于降低钻刀的工作温度,提升钻孔品质的稳定性。
✪钻刀易断刀问题的解决方案
其次是易断刀的问题,加工铜基板时由于铜屑不易切断,且小钻刀容屑空间小,排屑难,往往容易导致钻刀被积累的铜屑阻断。该问题可尝试对钻刀结构的优化来提升其排屑能力,从而减少钻刀被铜屑阻断的情况发生。钻刀的结构参数很多,涉及到钻尖角、螺旋角、钻芯厚度、芯厚倒锥度、钻头前角和后角、钻头横刃斜角等等。但考虑到同时优化所有的参数需要进行大量刀具制作及大量试验验证,这里选取两个对刀具加工影响最大的参数进行结构调整,即钻尖角和螺旋角,这两个参数的调整与影响如下表2所示。
表2钻尖角与螺旋角调整对刀具的影响
要注意的是对钻刀以上参数的调整幅度要合理,应确保钻刀加工的孔位精度以及刚性,钻尖角过大会造成钻头定心差,螺旋角过大则切削强度及散热能力也会降低。
✪钻刀难散热问题的解决方案
常规PCB钻孔设备用的是冷空气散热,但对铜基板钻孔而言这种散热方式的效率并不能满足。业界有不少厂商采用喷洒酒精冷却铜基板的方案来实施钻孔作业,然而操作起来还是比较麻烦的。实际上对铜基板可以适当地采用分步钻孔的方式来加工,如下图2所示。分步钻孔提供了较长的时间给钻头和板材散热,同时有助于及时把铜屑带出,避免钻头缠铜断刀。尽管这样的加工效率会低些,但提升钻孔散热能力可有效避免钻孔粘铜情况,不仅延长了钻刀寿命,也使钻孔质量得到了较好的保证,从而降低钻孔不良率。
图2分步钻孔示意图
铜基板钻孔参数的摸索
选择适当的刀具后,需要针对铜基的钻孔加工参数进行摸索,以检验钻孔效果能否满足要求。这里以0.5mm钻刀为例,对紫铜类铜基板加工,定制钻尖角145°,螺旋角40°的涂层钻刀,其余参数按常规设计,刀具如下图3所示。
图3定制0.5mm涂层刀具
✪转速区间的摸索
为了避免其它参数影响转速调整对钻孔质量的效果,将钻机的进给速度调整至最低0.1m/min,从最低钻速逐步提升,筛选适合转速区间,各转速设置下的钻孔测试结果如下表3所示。
表3 进给速度0.1m/min下各转速的刀具表现
可见在10krpm/min到20krpm/min这个区间的转速能够满足0.5mm钻刀钻铜块的要求。而更高的转速则出现了断刀的情况,断刀的孔位也出现了孔形崩坏,如下图4所示。
图4 高钻速条件断刀及孔形崩坏
✪钻孔深度的摸索
根据上述可接受的转速区间,选择居中的15krpm/min的钻速,依然保持0.1m/min最低进给速度,对钻孔深度逐步提升,分别进行不同深度的钻孔测试,其结果如下表4所示。
表4 各钻孔深度的刀具表现
可见钻刀仅钻到0.7mm的深度就出现了断刀的现象,原因在于孔内铜屑的残留在钻孔过程中不断累积,从而使刀具受到铜屑不均匀的阻力而断刀,如下图5所示。显然该刀具对于加工深度大于0.6mm的铜基板,必须采用多次叠加钻孔的方式进行加工。
图5 铜屑阻碍深钻导致断刀
✪进给速度的摸索
继续选取15krpm/min的钻速,进给速度从最低的0.1m/min逐步提升,分别进行不同进给速度的钻孔测试,各进给速度与刀具情况如下表5所示。
表5 各进给速度下的刀具表现
上表的测试结果稍显意外,在较合适的转速下,进给速度作了丝毫的提升还是断刀了。究其原因,进给速度提升会使钻刀的轴向力增大,并且由于对铜块钻孔的钻速较低,切削和排屑量跟不上进给速度也会导致断刀,低转速高进给下残屑导致的断刀效果如下图6所示。
图6 低转速高进给下残屑导致的断刀
铜基板小孔加工效果
基于上述摸索的试验结果,这里设定钻速15krpm/min,进刀速度0.1m/min,钻深1.0mm,分步钻2次,对铜基板进行0.5mm小孔的钻孔测试,同时以无涂层和有涂层的钻刀对比作刀具寿命测试,可得效果如下表所示6。
表6 无涂层和有涂层的钻刀寿命表现
可见在适合的加工参数下,钻刀未出现断刀状况,孔形也无破损,如下图7所示,而有无涂层的对比结果也很好得体现出涂层钻刀的耐用性。
图7 铜基板0.5mm钻针控深钻孔效果
总结
上述加工方案的提出,优化了对铜基板小孔加工的刀具及参数选择,从加工情况来看,也改善了铜基板小孔加工易断刀及钻孔品质不良的状况。尽管相比一些专业的五金加工设备,其加工效率要低很多,但本方案的优势就在于无需添加额外设备,基于现有PCB钻孔工艺就能实现铜基板的小孔加工,降低了技术门槛和投入成本。
参考文献:
[1]何文学,张加锋.紫铜零件小尺寸孔的钻孔加工分析[J].湖南工业职业技术学院学报,2015,10.
[2]张贺勇,陈成,骆金龙,罗春峰,付连宇.硬质与超硬涂层在印制电路板微型刀具上的应用[J].印制电路信息,2014,11
吴军权
研发工程师,CPCA行业工程师
主要从事PCB新技术与新产品研发项目
发布评论请先 登录
相关推荐
铜杆加工企业智能化管理 MES 系统解决方案
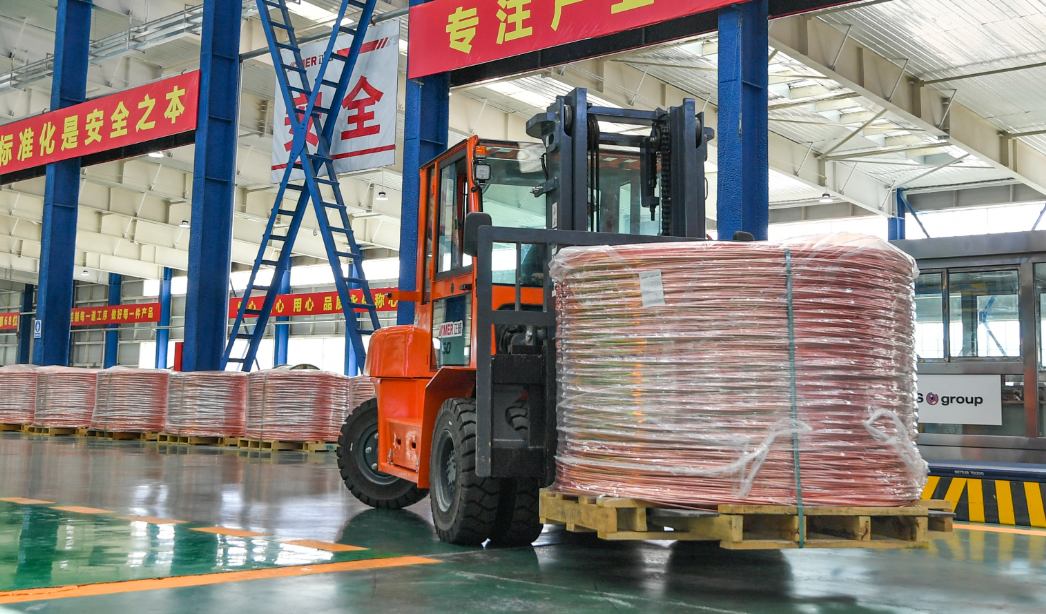
DOH技术工艺方案解决陶瓷基板DBC散热挑战问题
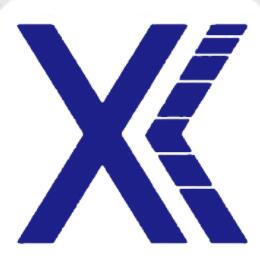
PCB盗铜工艺:技术与艺术的完美融合
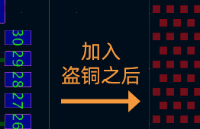
PCB设计中填充铜和网格铜有什么区别?
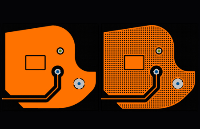
PCB设计中填充铜和网格铜有什么区别?
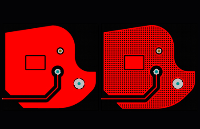
AMD获得玻璃核心基板技术专利
IC 封装载板用有机复合基板材料研究进展
解读热电分离PCB铜基板的卓越性能与应用前景
热电分离工艺铜基板:电子领域的创新力量
热电分离铜基板:构建高性能电子生态的基石
黄山谷捷:创新应用冷精锻工艺,引领散热基板行业新潮流
陶瓷基板技术PK:DBC vs DPC,你站哪一边?
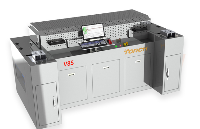
玻璃基板时代,TGV技术引领基板封装
高效、精准:皮秒激光切割机在陶瓷基板加工中的应用
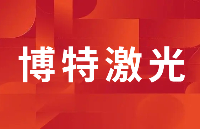
评论