1 引言
冶金关键过程控制系统中要求控制装置有极高的可靠性。在高炉炼铁生产中,如果控制系统出现故障,由此引起的停产和设备的损坏将造成极大的经济损失,只要系统中一个地方出问题,就会造成整个系统停产。仅仅通过提高控制系统的硬件及软件的可靠性来满足高炉炼铁对可靠性的要求是不可能的。因为可编程序控制器本身的可靠性的提高有一定的限度,并且可靠性的提高会使成本急剧增加。因此,对一些关键的、危险的或停止(故障)后对人员安全或设备损伤有重大隐患的控制部分经常使用冗余控制器或冗余系统就能够有效地解决上述问题。
2 数据冗余技术
“冗余”就是将相同功能的设备设计为2个或2个以上,如果一个设备有问题,另外一个设备就会自动承担起有问题设备的任务,使生产能够继续进行。具体说来就是备份出另一套服务。一般情况下是某一套系统运行,而第二个系统处于待命状态,可以通过人工方式监视第一套系统,当发现有故障时,便激活第二套系统。也可以用控制器对2个模块同时进行扫描,当其中一块停止回应时,系统从另一个模块中获取数据。由此可见,冗余的目的保证了系统工作的连续性(基本不会出现系统不工作的情况)、稳定性。
plc冗余可以分为软件冗余和硬件冗余两种。硬件冗余实现方式下对硬件型号有所要求,连接方式也不同,但对软件并无特殊要求。软件冗余投资不会太大,通过软件设计实现数据的读取、备用,监测到异常时自动切换。有些场合,也有按照冷冗余、暖冗余和热冗余来区分。
3 高炉自动化数据冗余
3.1 炉顶料罐压力冗余检测
炉顶料罐压力检测在日常生产中占有很重要的地位,若出现故障将直接影响到布料的顺利进行。莱钢1000立方米高炉整体由受料斗、料罐和高炉炉体三部分构成。焦炭、烧结矿等各种入炉原料由料车运到炉顶,倒入受料斗中。等到料罐内放散完毕后,即料罐压力为零时,打开上密阀和柱塞阀向料罐装料。装料完成后料罐将进行均压,此时料罐压力等于或者大于炉内压力,一旦高炉准备接受下一批炉料就进行布料,则打开下密阀并将料流调节阀开至设定开度,料罐中的炉料通过料流调节阀流到旋转的布料溜槽上。料罐清空后,关闭料流调节阀和下密封阀,打开放散阀进行放散,准备下一次装料。
从上述过程中可看到料罐压力在生产中的重要性,如果无法正确到检测料罐压力,会导致受料斗中的入炉原料无法进入料罐中,同时料罐中已有的炉料不能顺利向炉内布放。
并且当初高炉设计时,将“料罐压力”和“炉内压力”两个检测点的信号先引入本体控制室中,然后通过光纤通讯,传到槽下控制室,该控制室的plc接受并且处理后,再对炉顶设备进行控制。所以通讯是否畅通也是一个不得不警惕的隐患。
通过研究分析,采用数据冗余中硬件冗余的方式,可在原有设备基础上增加一套压力变送器,其信号不通过第三方传递,直接引致槽下控制室中进行处理。平时两套设备都在运行,由本体控制室通讯来的信号和直接从高炉传来的备用信号送给槽下控制室的plc处理,遵循一用一备的原则选择使用。这样就减少了对一套设备的依赖,增加了设备可靠性和操作灵活性。图1为改造后的数据传输、处理过程。

图1 高炉冗余数据传输处理
备用压力变送器要与原有的设备具有型号和相同的规格,这样采集的数据才有可比性,不会有较大的误差;两路信号的使用原则为“一用一备”,即在生产中只使用一路信号,参与生产控制,另一路信号处于备用状态。互为切换使用,当某一路信号出现异常时,另一路可迅速投入使用;监控画面要将两路信号的状态实时体现出来,通过显示的数值和数值的变化来判定两套变送器的运行状况。从而为选用哪一路信号参与控制做参考。监控画面设计如图2所示。

图2 监控画面
炉内压力用棒图的形式表示炉内压力检测点的变化情况。料罐压力。用棒图的形式表示两路料罐压力检测点的变化情况。切换设定用于手动切换使用料罐压力检测点信号。异常设定做了一个报警系统,当两路料罐压力之间的差值大于设定值后即认定为异常,发出报警,由操作人员做出判断。
通过改造,两套压力变送器运行状况良好,平时两套设备同时工作着,互为备用,都能很好得参与到生产控制中去,降低了因设备故障而影响生产的几率,画面上的棒图表示可以很好的反映出两路信号的变化情况,操作简单,而且在不影响生产的基础上可以很方便的对设备进行维护保养,提高了设备寿命和系统整体的可靠性,使维护更加方便。
3.2 数据库冗余的应用
冗余可以分为软件冗余和硬件冗余两种,软件冗余的特点是投资少,见效快,在莱钢1000立方米高炉的软件冗余应用中,最有代表性的就是历史记录数据库的冗余设计。
在自动化控制系统的监控画面中,历史趋势占有很重要的地位,通过历史趋势,操作人员可以很方便的判断当前一段时间的生产状况,为下一步的生产起到指导作用。或者在生产中出现事故后,操作人员往往首先去查看历史趋势,从而判断事故原因。历史趋势的数据需要记录在数据库中,因此,为了确保历史数据的完整性和安全性,需要对数据库进行冗余设计。
如图3的系统结构所示,该控制室有三台上位机,都通过交换机和plc进行数据交换,②号、③号机都安装数据库,用于保存历史数据,通过交换机可以互访对方的数据库。若其中一台出现故障,另一台可以继续记录历史数据,不影响历史数据的查询和记录。

图3 系统结构
通过上述改造,监控系统的灵活性大大提高,操作性能进一步得到了改善,利用现有的资源,做出了合理的资源优化。将软件冗余的技术特点,应用到生产建设中。
3.3 探尺的冗余检测改造
莱钢1000立方米高炉现采用一部机械探尺,一部雷达探尺的双探尺模式对炉内料面进行检测。之所以采用这种方式,是根据实际生产特点做出的改进。不同与以往简单的数据采集设备冗余,应看作是对同一检测对象的设备类型冗余。
高炉竣工之初,安装使用的是两部机械探尺,投入生产后,发现传统的机械探尺虽然测量数据可靠,但体积大,而且经常发生故障。过去高炉塌料后,机械探尺根本探不到料面,不能反映料面深度。雷达探尺是一个连续的测量过程,是通过雷达的原理来探测料面的深度,探测深度不受限制,采用非接触的测量方式,24小时不间断工作,通过电子部件算出探头到介质表面的距离,能够准确及时地反映高炉料面情况,设备体积小,易操作,测量精度高。适应高温、粉尘、潮湿的工作环境,可连续、稳定检测高炉料位,无机械磨损故障,通过与机械探尺配合使用,可以更好地掌握高炉料面情况。
经过改造,拆除了一部机械探尺,在原开口处安装一部雷达探尺,与原先的机械式探尺同时使用,同时在值班室位机上做出料位实时曲线图和历史曲线图,可以随时供查看,便于高炉工长对整个高炉进行全面掌控,及时判断出高炉崩料、坐料等异常情况,很好跟踪机械探尺,弥补机械探尺探测深度只有四米、加料时探不出、监测有间隙等不足,为高炉提供准确的料位数据,有利于高炉提高操作控制的准确性,为高炉稳定、顺行提供技术保证。
3.4 控制回路与限位信号冗余的应用
对一些采用液压回路控制的设备,出于技术方面的考虑,各增加一套控制回路,作为备用。如:上密阀、柱塞阀、下密阀、放散阀和均压阀。这些在日常生产中具有很重要作用的阀都有一个共同特点,就是都采用了液压控制。液压装置易发生油路阻塞或因为天气寒冷导致控制失灵等故障,而且故障不能迅速修复,因此增加一套独立的控制回路就十分的必要,同时在这些被控制的设备上增加备用的限位信号,对判断是设备故障还是控制回路故障具有重要的指导作用。监控画面的设计要做到能对现场设备做出正确判断,还要很方便地对冗余设备进行切换使用,以柱塞阀的控制画面如图4所示。
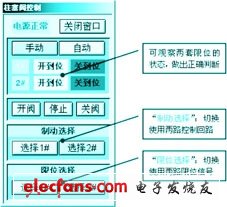
图4 柱塞阀控制
4 高炉自动化数据冗余关键
要做到数据信号的独立性。虽然在plc每个模板上都留有少量的备用点,但在冗余设计中应遵循的一个原则,即冗余的信号要与原先的信号接在不同的模板上,否则因为模板的故障而导致两路信号全部失灵,失去了冗余设计的本意。
对于输入量冗余的处理,特别是检测信号的冗余,我们虽然接受两组信号,但并不一定把两组数据都进行处理,即:同时接受,但只处理一组。因为这样可以减少系统的运算时间,在程序控制过程中只取一组信号,另一组处于备用状态,不会造成程序混乱。
当出现故障时,两套设备是自动进行切换,还是操作人员手动进行切换是冗余设计的两种思路,自动切换的优点就是当出现故障时程序能第一时间内发现故障,并自动做出相应的处理,缺点就可能因为假信号的干扰而做出错误的判断,而且操作人员不易觉察。通过权衡利弊后,莱钢1000立方米高炉采用的方式为手动切换,由于采用了异常报警,当出现异常时,操作人员同样可以及时发现,通过他对当时情况的分析,做出相应的操作,这样的好处就是操作人员可以察觉到异常,并且易于查找事故原因。
冗余设计是需要从全局考虑,当发生事故时,造成的损失是很容易计算出来的,但增加了防范措施后,因成功防范事故得到的收益和创造的效益却是无形的,得不到的。因此对该有冗余的设备不重视,舍不得投入,往往就会因小失大;但发生事故几率很小的地方却增加冗余,任凭设备损耗,无形中增加了不必要的投入,提高了生产成本。
5 结束语
通过数据采集冗余设计,莱钢1000立方米高炉大大地提高了系统的可靠性和工作的连续性,实际应用的效果也非常理想,加快了高炉的生产节奏,提高了产量,对于提高系统自动化控制水平,减轻操作人员负担,降低事故率,提高了设备寿命具有重大意义。
评论