1 工艺介绍
本锅炉系统主要通过燃烧高炉煤气和焦炉煤气为某钢铁公司1000M3高炉提供动力,并季节性提供工业用暖。锅炉主要包括煤气(高炉煤气、焦炉煤气)系统、炉体部分、对流受热面(汽包及冷却壁,I、II过热器,I、II省煤器,I、II空气预热器)、点火器、送引风设备等组成。
按照各部分的功能大致分为汽水系统、风烟系统、燃烧系统、减温减压及公用系统几个子系统。
本控制系统主要控制锅炉及相关辅助设备的生产过程,使其符合工艺所要求达到的蒸汽温度(450℃)、压力(3.82MPa)、流量(130t/h)、纯度(过热蒸汽)。
1.1 汽水系统
汽水系统是供给锅炉保护和产生蒸汽的除氧水,生成载热的过热蒸汽送到汽机膨胀做功或者经过减温减压后供热。来自除氧给水系统的除氧水经过调节后送到I、II省煤器预热,然后送到锅炉汽包和与汽包相连的锅炉冷却壁中,经过锅炉燃烧生成的高温烟气的加热生成不饱和蒸汽,不饱和蒸汽经过I级过热器、I级过热器蒸汽集箱,经过喷水减温器减温处理后,再经过II级过热器、II级过热器蒸汽集箱后生成饱和的过热蒸汽,然后送到蒸汽母管,一部分送到汽机膨胀做功,一部分进入减温减压系统, 一部分提供除氧汽动给水泵做功给水。
1.2 风烟系统
空气(冷风)经过净化后通过1#、2#送风机送到I、II空气预热器中进行预热成为热风,热风送到热风烧嘴和煤气混合燃烧;高炉煤气和焦炉煤气通过高炉煤气管道和焦炉煤气管道送到燃烧喷嘴和热风混合燃烧,生成高温烟气,加热锅炉汽包中的除氧水使之成为不饱和蒸汽,然后高温烟气依次通过I过热器、II过热器、II省煤器、II空气预热器、I省煤器、I空气预热器将不饱和蒸汽加热成为高温高压的饱和蒸汽,并预热送到锅炉汽包中的除氧水和送到锅炉炉膛中的空气,最后通过引风机引至烟囱中排放。
1.3 燃烧系统
高炉煤气由外部接入,分为4路,分别进入锅炉的4个角(每角4个燃烧喷嘴),参与燃烧;进入锅炉和高炉煤气混合燃烧的热风分别进入锅炉的4个角(每角4个燃烧喷嘴),参与燃烧;焦炉煤气由外部接入,分为4路,分别进入锅炉的4个角(每角2个燃烧喷嘴),参与燃烧。正常情况下,燃料为高炉煤气,焦炉煤气只是在点火的时候用到,平时只是作为保安气(作为锅炉燃烧过程中的炉膛温度低时保护气)。
燃烧过程中通过热电偶和火焰观测器来检测炉膛温度变化。通过调节高炉煤气、焦炉煤气、风的配比来调节锅炉炉膛温度(燃料配比一般为100%高炉煤气,另外也有80%--90%高炉煤气加20%--10%焦炉煤气或者50%焦炉煤气)。整个燃烧过程中炉膛温度控制在1100±10℃左右。
1.4 减温减压及公用系统
本锅炉产生的过热蒸汽大部分送到汽机做功给高炉供风,其余的一部分送到中温中压联络管,另一部分送到1#、2#减温减压器经过工业水的减温减压后变为低温低压蒸汽,一部分送到厂区供热,另一部分通过加热蒸汽母管送到除氧器,一部分提供除氧汽动给水泵做功给水。
2.系统配置
2.1 DCS系统
计算机集散控制系统(DCS)由上位系统和下位系统组成。上位系统采用工业控制计算机,用Siemens组态软件WinCC完成现场数据的实时显示、存储、报警处理、打印及控制参数设定。下位系统由Siemens PLC构成,与现场设备相连。上位系统和下位系统之间的通讯采用Ethernet方式,其最高传输速率可达10-100Mbit/s,完全满足对数据实时监控的要求。自动控制系统采用S7 400 系列PLC硬件组成基础自动化系统, 采用WINCC V6.0监控软件,编程软件采用STEP 7 V5.3,Windows 2000作为系统平台界面,组成计算机操作系统,实现人机通讯。
2.2 系统配置图

图1 DCS系统组成
3 控制功能
3.1 燃烧控制
锅炉运行供汽是为了满足汽轮机的运行负荷要求,同时满足鼓风机站提供低压蒸汽的需要。汽轮机和外供汽的负荷变化,会影响锅炉蒸汽压力的变化。只要满足蒸汽压力的稳定,必然满足蒸汽量的要求。因此,锅炉燃烧自动控制的目的就是通过自动燃烧达到稳定蒸汽母管的压力,来满足汽轮机及外供汽对蒸汽的要求。
由于锅炉的燃烧系统到供汽系统是一个较复杂的热力过程,在运行中将受到:汽轮机工况变化所引起的蒸汽负荷的变化及外供汽对蒸汽负荷的变化(称外扰);燃料热值、燃料种类等锅炉内部热负荷的变化所引起的蒸汽量的变化(称内扰);从燃料变化开始到炉内建立热负荷的时间(称燃烧设备的惯性);在锅炉受到外扰时,燃烧工况未变时而具有的吸热和放热能力(称锅炉的蓄热能力)。因此,自动燃烧程序应具有抗干扰的能力,以达到平稳地自动调节。
为使锅炉达到经济的燃烧,在燃料或负荷调节的同时,应改变送风和引风量。锅炉使用燃料可能有如下的配比:100%高炉煤气(正常运行使用此种配比)、80~90%高炉煤气加20~10%的焦炉煤气、50%高炉煤气加50%焦炉煤气。锅炉增减负荷量较大时,可以采用停开某一层或者数层高炉煤气燃烧器煤气管道上的电动调节阀和热风管道上的电动调节阀进行自动调节。
3.2 汽包水位控制
采用三冲量调节,即根据给水流量、汽包液位和蒸汽流量调节主给水阀,保证锅炉汽包水位的稳定,是前馈—反馈串级调节回路,框图如下:锅炉给水系统中,由锅炉提供两个给水调节阀,其中DN150调节阀是主调节阀,在正常负荷和高负荷运行时使用;旁通管设一个DN100的调节阀,在低负荷时使用,同时也作为主调节阀的备用阀。在自动给水状态下,只允许其中之一自动调节给水,此时,另一调节阀可画面手动给水;在程序投入之前,操作人员需要事先选定哪一个调节阀自动投入。如果此次未能设定,将按照上一次的设定执行。
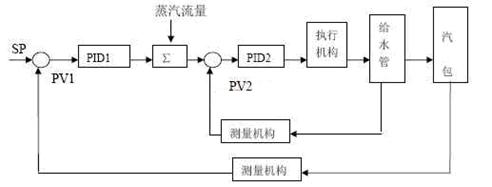
图2 汽包水位控制系统的结构图
其中:
SP---------汽包液位设定点 PV1--------汽包液位测量值
PID1-------汽包液位调节,为主调,反作用 PV2--------给水流量测量值
PID2-------给水量调节,为副调
----加法器,其公式如下:
X0=X2+2×(X1-50%) X0----输出
X1----汽包液位调节的输出 X2----蒸汽流量信号
将液位进行PID1调节后输出,和蒸汽流量进行加法运算,其结果作为PID2的设定点,PID2将此设定点与给水流量的偏差进行调节,输出带动执行机构,调节给水阀。
汽包液位是主被调量,给水量是副被调量,蒸汽流量是前馈量。当汽包液位上升时,PID1的输出减小,则加法器的输出也减小,给水阀关小,就减小了给水量。当汽包负荷变大时,即蒸汽流量增加,加法器的输出就增大,给水阀开大,就增大了给水量。
当蒸汽负荷突然增加,而出现“假液位”时,由于PID1是反作用,PID1的输出就减小,即加法器里的X1就减小;由于负荷增加,加法器里的X2就增加,这样,加法器的输出基本变化不大。经过短时间后汽包内压力恢复平衡,“假液位”消除,此时液位因蒸发量增加而开始下降,PID1的输出就增加,则给水量增加,直至汽包液位恢复到给定位置。
3.3 炉膛负压调节
炉膛负压自动控制是通过调节引风机入口风门开度,保持炉膛负压在-20--10 Pa的微负压状态,保证锅炉安全燃烧。当两台引风机同时运行时,应并列或者固定其中的一个对另一个进行调节,可在画面上选择并列还是固1调2(1为固1调2,0为固2调1)。炉膛负压设高、低报警。
3.4 锅炉送风自动控制
送风自动控制目的:使锅炉所投入的燃料在炉膛中燃烧时,自动投入合适的风量,以保证锅炉的经济燃烧。主要控制的参数为煤气压力及送风压力, 进而达到最高的的锅炉热效率, 烟气含氧量作为总风量的修正量。通过调节送风机的挡板开度来调节送风压力;当两台送风机同时运行时,应并列(或者固定其中之一,对另一个进行)调节入口风门,可在画面上选择并列还是固1调2(1为固1调2,0为固2调1)。
3.5 锅炉过热蒸汽温度自动调节(减温水自动调节)
锅炉过热蒸汽温度调节采用自制冷凝水喷水减温装置,锅炉过热蒸汽温度自动调节是根据集器集箱和减温器出口蒸汽温度自动调节减温水调节阀开度,控制减温水量,以保证集汽集箱中蒸汽温度控制在430--450℃范围内。当集汽集箱出口蒸汽温度降低时,汽温自动调节系统自动减少减温水量,随着汽温升高,减温水量增加,保证集汽集箱出口蒸汽温度稳定,反之则减小减温水量,避免汽温产生较大波动。喷水减温系统中,由锅炉提供两个给水调节阀,其中DN50调节阀是主调节阀,在正常运行时使用;旁通管设一个DN50的调节阀,作为主调节阀的备用阀。在自动给水状态下,只允许其中之一自动调节给水,另一调节阀备用;在程序投入之前,操作人员需要事先选定哪一个调节阀自动投入。如果此次未能设定,将按照上一次的设定执行。在主给水调节阀后设DN150的调节阀,根据所需要的冷凝水量调节该调节阀的开度。采用串级调节,蒸汽出口温度经PID1调节输出后,作为PID2(减温器出口温度调节)的设定点,PID2对此设定点和减温器出口温度的偏差进行调节,输出带动执行机构,调节减温水调节阀。
当测得集汽集箱出口蒸汽温度高时,PID1的输出增大,则减温水调节阀开大,增加减温水量;反之,则减小阀门开度,减少减温水量。
当有扰动时(主要扰动有烟气流量和温度的变化引起的扰动,减温器入口蒸汽流量和温度引起的扰动,减温水压力变化引起的扰动)首先反映在减温器出口的蒸汽温度变化,温度一高,则要求增加减温水量,调节就比较迅速,而对集汽集箱出口的蒸汽温度的影响就比较小,提高了调节品质。框图如下:

图3 过热蒸汽温度自动调节控制系统的结构图
4 监控功能
在画面上可显示锅炉各部分时的温度、压力、流量分布状况,采集的数据,历史趋势、报警闪烁画面,完成各阀门、设备的开启及操作,完成煤气、助燃空气的调节阀的操作及调节,各系统的自动调节与软手动调节、硬手动调节的无扰自动切换,各调节阀的操作及调节和保持各数据的动态显示。 主要画面如下:
主菜单:完成系统登陆,选择工作制度、切入主画面。
主画面:可显示锅炉炉的整个工艺生产流程及相关的主要参数值,报警闪烁,切入其他画面的功能按钮。分画面:各调节系统的画面,包括参数设定的功能键、棒状图、控制流程图、报警纪录,相关信息;历史趋势,相关的PID参数设定等。
报警画面:按工艺要求,当过程值超过报警上下限时,发出报警,并在报警画面上显示报警发生时间、报警值、报警等级、报警点,操作员在报警画面中可以完成报警确认、报警信息过滤等功能。
报表打印:可设置任意格式报表,可打印所有输入输出参数的报表。另外,对监控站设有多个安全级进行管理,每个安全级均由不同的权限,防止侵权或误操作。
5 应用效果
采用DCS系统及相关控制流程以后,首先使操作工操作方便,使用鼠标点击即可,整个锅炉的运行状况在计算机屏幕上一目了然。在实际应用中,采用DCS及相关控制技术的主要优点有:提高能源利用率,保证系统能够高效安全运行;出水温度稳定,提高舒适度;升温速度快。从控制性能看,调节比较及时,超调不大,上下波动小,运行稳定。
从节能降耗看,该生产线使用了工业过程优化自动控制技术以后,提高了系统可靠性,与同种类型锅炉相比, 每年减少故障停机时间约200小时,锅炉功率为130吨/小时,蒸汽按70元/吨计,每年可节约资金180余万人民币, 给企业带来可观经济效益。
本文作者创新点:提出了一种基于分布式煤气燃烧锅炉控制系统,既充分利用PC机丰富的软硬件资源实现友好的人机界面,又通过工业以太网结构与PLC机进行通信,对锅炉现场进行数据采集和及时处理,达到了锅炉燃烧工况良好、节能降耗的工艺要求;全面实现仪电合一,统一由PLC和DCS完成其控制功能,实现了全面EIC一体化的系统。该系统控制思想较为先进,运行稳定,安全,可靠,节能。采用SIMATIC S7-400系列可编程控制器进行锅炉控制,硬件可由软件组态,软件编程层次清楚,现场调试方便,利用其强大的通讯功能可组成各种分布式监控管理系统。
参考文献
[1]鹿世金.工业锅炉节能的控制技术[M].兵器工业出版社.1993.
[2]吴振纲,陈虎.PLC的人机接口与编程[J].微计算机信息,2005,8-1:21-23。
[3]郑金吴等.燃煤低压热水锅炉测控技术设计与研究[J].工业控制计算机.14卷第6期.2001.
[4]SIMATIC S7 STEP7 5.3编程手册
作者简介
王志明,男,生于1973年,山东曹县人, 工程师, 1994年毕业于沈阳黄金学院,2005年6月毕业于山东科技大学,软件工程硕士,现从事自动化维护与研究。工作单位:莱钢集团公司自动化部。
通讯地址:山东省莱芜市钢城区莱钢集团公司自动化部钢区车间 271104
本锅炉系统主要通过燃烧高炉煤气和焦炉煤气为某钢铁公司1000M3高炉提供动力,并季节性提供工业用暖。锅炉主要包括煤气(高炉煤气、焦炉煤气)系统、炉体部分、对流受热面(汽包及冷却壁,I、II过热器,I、II省煤器,I、II空气预热器)、点火器、送引风设备等组成。
按照各部分的功能大致分为汽水系统、风烟系统、燃烧系统、减温减压及公用系统几个子系统。
本控制系统主要控制锅炉及相关辅助设备的生产过程,使其符合工艺所要求达到的蒸汽温度(450℃)、压力(3.82MPa)、流量(130t/h)、纯度(过热蒸汽)。
1.1 汽水系统
汽水系统是供给锅炉保护和产生蒸汽的除氧水,生成载热的过热蒸汽送到汽机膨胀做功或者经过减温减压后供热。来自除氧给水系统的除氧水经过调节后送到I、II省煤器预热,然后送到锅炉汽包和与汽包相连的锅炉冷却壁中,经过锅炉燃烧生成的高温烟气的加热生成不饱和蒸汽,不饱和蒸汽经过I级过热器、I级过热器蒸汽集箱,经过喷水减温器减温处理后,再经过II级过热器、II级过热器蒸汽集箱后生成饱和的过热蒸汽,然后送到蒸汽母管,一部分送到汽机膨胀做功,一部分进入减温减压系统, 一部分提供除氧汽动给水泵做功给水。
1.2 风烟系统
空气(冷风)经过净化后通过1#、2#送风机送到I、II空气预热器中进行预热成为热风,热风送到热风烧嘴和煤气混合燃烧;高炉煤气和焦炉煤气通过高炉煤气管道和焦炉煤气管道送到燃烧喷嘴和热风混合燃烧,生成高温烟气,加热锅炉汽包中的除氧水使之成为不饱和蒸汽,然后高温烟气依次通过I过热器、II过热器、II省煤器、II空气预热器、I省煤器、I空气预热器将不饱和蒸汽加热成为高温高压的饱和蒸汽,并预热送到锅炉汽包中的除氧水和送到锅炉炉膛中的空气,最后通过引风机引至烟囱中排放。
1.3 燃烧系统
高炉煤气由外部接入,分为4路,分别进入锅炉的4个角(每角4个燃烧喷嘴),参与燃烧;进入锅炉和高炉煤气混合燃烧的热风分别进入锅炉的4个角(每角4个燃烧喷嘴),参与燃烧;焦炉煤气由外部接入,分为4路,分别进入锅炉的4个角(每角2个燃烧喷嘴),参与燃烧。正常情况下,燃料为高炉煤气,焦炉煤气只是在点火的时候用到,平时只是作为保安气(作为锅炉燃烧过程中的炉膛温度低时保护气)。
燃烧过程中通过热电偶和火焰观测器来检测炉膛温度变化。通过调节高炉煤气、焦炉煤气、风的配比来调节锅炉炉膛温度(燃料配比一般为100%高炉煤气,另外也有80%--90%高炉煤气加20%--10%焦炉煤气或者50%焦炉煤气)。整个燃烧过程中炉膛温度控制在1100±10℃左右。
1.4 减温减压及公用系统
本锅炉产生的过热蒸汽大部分送到汽机做功给高炉供风,其余的一部分送到中温中压联络管,另一部分送到1#、2#减温减压器经过工业水的减温减压后变为低温低压蒸汽,一部分送到厂区供热,另一部分通过加热蒸汽母管送到除氧器,一部分提供除氧汽动给水泵做功给水。
2.系统配置
2.1 DCS系统
计算机集散控制系统(DCS)由上位系统和下位系统组成。上位系统采用工业控制计算机,用Siemens组态软件WinCC完成现场数据的实时显示、存储、报警处理、打印及控制参数设定。下位系统由Siemens PLC构成,与现场设备相连。上位系统和下位系统之间的通讯采用Ethernet方式,其最高传输速率可达10-100Mbit/s,完全满足对数据实时监控的要求。自动控制系统采用S7 400 系列PLC硬件组成基础自动化系统, 采用WINCC V6.0监控软件,编程软件采用STEP 7 V5.3,Windows 2000作为系统平台界面,组成计算机操作系统,实现人机通讯。
2.2 系统配置图

图1 DCS系统组成
3 控制功能
3.1 燃烧控制
锅炉运行供汽是为了满足汽轮机的运行负荷要求,同时满足鼓风机站提供低压蒸汽的需要。汽轮机和外供汽的负荷变化,会影响锅炉蒸汽压力的变化。只要满足蒸汽压力的稳定,必然满足蒸汽量的要求。因此,锅炉燃烧自动控制的目的就是通过自动燃烧达到稳定蒸汽母管的压力,来满足汽轮机及外供汽对蒸汽的要求。
由于锅炉的燃烧系统到供汽系统是一个较复杂的热力过程,在运行中将受到:汽轮机工况变化所引起的蒸汽负荷的变化及外供汽对蒸汽负荷的变化(称外扰);燃料热值、燃料种类等锅炉内部热负荷的变化所引起的蒸汽量的变化(称内扰);从燃料变化开始到炉内建立热负荷的时间(称燃烧设备的惯性);在锅炉受到外扰时,燃烧工况未变时而具有的吸热和放热能力(称锅炉的蓄热能力)。因此,自动燃烧程序应具有抗干扰的能力,以达到平稳地自动调节。
为使锅炉达到经济的燃烧,在燃料或负荷调节的同时,应改变送风和引风量。锅炉使用燃料可能有如下的配比:100%高炉煤气(正常运行使用此种配比)、80~90%高炉煤气加20~10%的焦炉煤气、50%高炉煤气加50%焦炉煤气。锅炉增减负荷量较大时,可以采用停开某一层或者数层高炉煤气燃烧器煤气管道上的电动调节阀和热风管道上的电动调节阀进行自动调节。
3.2 汽包水位控制
采用三冲量调节,即根据给水流量、汽包液位和蒸汽流量调节主给水阀,保证锅炉汽包水位的稳定,是前馈—反馈串级调节回路,框图如下:锅炉给水系统中,由锅炉提供两个给水调节阀,其中DN150调节阀是主调节阀,在正常负荷和高负荷运行时使用;旁通管设一个DN100的调节阀,在低负荷时使用,同时也作为主调节阀的备用阀。在自动给水状态下,只允许其中之一自动调节给水,此时,另一调节阀可画面手动给水;在程序投入之前,操作人员需要事先选定哪一个调节阀自动投入。如果此次未能设定,将按照上一次的设定执行。
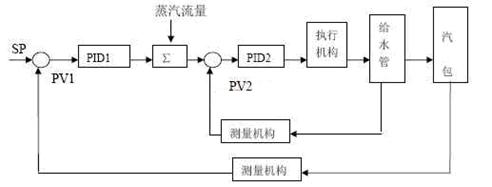
图2 汽包水位控制系统的结构图
其中:
SP---------汽包液位设定点 PV1--------汽包液位测量值
PID1-------汽包液位调节,为主调,反作用 PV2--------给水流量测量值
PID2-------给水量调节,为副调

X0=X2+2×(X1-50%) X0----输出
X1----汽包液位调节的输出 X2----蒸汽流量信号
将液位进行PID1调节后输出,和蒸汽流量进行加法运算,其结果作为PID2的设定点,PID2将此设定点与给水流量的偏差进行调节,输出带动执行机构,调节给水阀。
汽包液位是主被调量,给水量是副被调量,蒸汽流量是前馈量。当汽包液位上升时,PID1的输出减小,则加法器的输出也减小,给水阀关小,就减小了给水量。当汽包负荷变大时,即蒸汽流量增加,加法器的输出就增大,给水阀开大,就增大了给水量。
当蒸汽负荷突然增加,而出现“假液位”时,由于PID1是反作用,PID1的输出就减小,即加法器里的X1就减小;由于负荷增加,加法器里的X2就增加,这样,加法器的输出基本变化不大。经过短时间后汽包内压力恢复平衡,“假液位”消除,此时液位因蒸发量增加而开始下降,PID1的输出就增加,则给水量增加,直至汽包液位恢复到给定位置。
3.3 炉膛负压调节
炉膛负压自动控制是通过调节引风机入口风门开度,保持炉膛负压在-20--10 Pa的微负压状态,保证锅炉安全燃烧。当两台引风机同时运行时,应并列或者固定其中的一个对另一个进行调节,可在画面上选择并列还是固1调2(1为固1调2,0为固2调1)。炉膛负压设高、低报警。
3.4 锅炉送风自动控制
送风自动控制目的:使锅炉所投入的燃料在炉膛中燃烧时,自动投入合适的风量,以保证锅炉的经济燃烧。主要控制的参数为煤气压力及送风压力, 进而达到最高的的锅炉热效率, 烟气含氧量作为总风量的修正量。通过调节送风机的挡板开度来调节送风压力;当两台送风机同时运行时,应并列(或者固定其中之一,对另一个进行)调节入口风门,可在画面上选择并列还是固1调2(1为固1调2,0为固2调1)。
3.5 锅炉过热蒸汽温度自动调节(减温水自动调节)
锅炉过热蒸汽温度调节采用自制冷凝水喷水减温装置,锅炉过热蒸汽温度自动调节是根据集器集箱和减温器出口蒸汽温度自动调节减温水调节阀开度,控制减温水量,以保证集汽集箱中蒸汽温度控制在430--450℃范围内。当集汽集箱出口蒸汽温度降低时,汽温自动调节系统自动减少减温水量,随着汽温升高,减温水量增加,保证集汽集箱出口蒸汽温度稳定,反之则减小减温水量,避免汽温产生较大波动。喷水减温系统中,由锅炉提供两个给水调节阀,其中DN50调节阀是主调节阀,在正常运行时使用;旁通管设一个DN50的调节阀,作为主调节阀的备用阀。在自动给水状态下,只允许其中之一自动调节给水,另一调节阀备用;在程序投入之前,操作人员需要事先选定哪一个调节阀自动投入。如果此次未能设定,将按照上一次的设定执行。在主给水调节阀后设DN150的调节阀,根据所需要的冷凝水量调节该调节阀的开度。采用串级调节,蒸汽出口温度经PID1调节输出后,作为PID2(减温器出口温度调节)的设定点,PID2对此设定点和减温器出口温度的偏差进行调节,输出带动执行机构,调节减温水调节阀。
当测得集汽集箱出口蒸汽温度高时,PID1的输出增大,则减温水调节阀开大,增加减温水量;反之,则减小阀门开度,减少减温水量。
当有扰动时(主要扰动有烟气流量和温度的变化引起的扰动,减温器入口蒸汽流量和温度引起的扰动,减温水压力变化引起的扰动)首先反映在减温器出口的蒸汽温度变化,温度一高,则要求增加减温水量,调节就比较迅速,而对集汽集箱出口的蒸汽温度的影响就比较小,提高了调节品质。框图如下:

图3 过热蒸汽温度自动调节控制系统的结构图
4 监控功能
在画面上可显示锅炉各部分时的温度、压力、流量分布状况,采集的数据,历史趋势、报警闪烁画面,完成各阀门、设备的开启及操作,完成煤气、助燃空气的调节阀的操作及调节,各系统的自动调节与软手动调节、硬手动调节的无扰自动切换,各调节阀的操作及调节和保持各数据的动态显示。 主要画面如下:
主菜单:完成系统登陆,选择工作制度、切入主画面。
主画面:可显示锅炉炉的整个工艺生产流程及相关的主要参数值,报警闪烁,切入其他画面的功能按钮。分画面:各调节系统的画面,包括参数设定的功能键、棒状图、控制流程图、报警纪录,相关信息;历史趋势,相关的PID参数设定等。
报警画面:按工艺要求,当过程值超过报警上下限时,发出报警,并在报警画面上显示报警发生时间、报警值、报警等级、报警点,操作员在报警画面中可以完成报警确认、报警信息过滤等功能。
报表打印:可设置任意格式报表,可打印所有输入输出参数的报表。另外,对监控站设有多个安全级进行管理,每个安全级均由不同的权限,防止侵权或误操作。
5 应用效果
采用DCS系统及相关控制流程以后,首先使操作工操作方便,使用鼠标点击即可,整个锅炉的运行状况在计算机屏幕上一目了然。在实际应用中,采用DCS及相关控制技术的主要优点有:提高能源利用率,保证系统能够高效安全运行;出水温度稳定,提高舒适度;升温速度快。从控制性能看,调节比较及时,超调不大,上下波动小,运行稳定。
从节能降耗看,该生产线使用了工业过程优化自动控制技术以后,提高了系统可靠性,与同种类型锅炉相比, 每年减少故障停机时间约200小时,锅炉功率为130吨/小时,蒸汽按70元/吨计,每年可节约资金180余万人民币, 给企业带来可观经济效益。
本文作者创新点:提出了一种基于分布式煤气燃烧锅炉控制系统,既充分利用PC机丰富的软硬件资源实现友好的人机界面,又通过工业以太网结构与PLC机进行通信,对锅炉现场进行数据采集和及时处理,达到了锅炉燃烧工况良好、节能降耗的工艺要求;全面实现仪电合一,统一由PLC和DCS完成其控制功能,实现了全面EIC一体化的系统。该系统控制思想较为先进,运行稳定,安全,可靠,节能。采用SIMATIC S7-400系列可编程控制器进行锅炉控制,硬件可由软件组态,软件编程层次清楚,现场调试方便,利用其强大的通讯功能可组成各种分布式监控管理系统。
参考文献
[1]鹿世金.工业锅炉节能的控制技术[M].兵器工业出版社.1993.
[2]吴振纲,陈虎.PLC的人机接口与编程[J].微计算机信息,2005,8-1:21-23。
[3]郑金吴等.燃煤低压热水锅炉测控技术设计与研究[J].工业控制计算机.14卷第6期.2001.
[4]SIMATIC S7 STEP7 5.3编程手册
作者简介
王志明,男,生于1973年,山东曹县人, 工程师, 1994年毕业于沈阳黄金学院,2005年6月毕业于山东科技大学,软件工程硕士,现从事自动化维护与研究。工作单位:莱钢集团公司自动化部。
通讯地址:山东省莱芜市钢城区莱钢集团公司自动化部钢区车间 271104

评论