Abstract: The flyback dc-dc converter topology results in significant cost and space savings for multiple output power supplies with high output voltage for power levels up to 100W. Flyback topologies store and transfer energy using a transformer, which due to physical limitations can cause large voltage transient spikes during the switching cycle. This article outlines the design of dissipative voltage suppression circuits (voltage snubbers) that can be used to suppress these transients on both the primary and secondary side.
The flyback topology (Figure 1A) results in significant cost and space savings for multiple output power supplies with high output voltage for power levels up to 100W. This topology uses a transformer, which is essentially a coupled inductor with multiple windings on the same magnetic core. Flyback topologies operate by storing energy in the transformer during the power switch on-time and transferring this energy to the output during the off-time. The energy is stored in a non-magnetic gap in series with the transformer core. In practice, the multiple windings cannot all be equally well coupled to the core because of the physical separation between the windings. A small amount of energy is also stored within and between these windings. This energy is represented in the circuit as a leakage inductance (Figure 1B).

Figure 1A. Basic topology of flyback circuit.
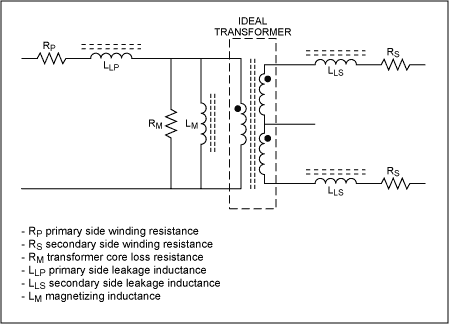
Figure 1B. Equivalent transformer model.
The flyback topology is attractive for multiple output supplies because the output voltages track one another with line and load changes and because adding outputs to the system does not require additional ICs. Despite its advantages, the flyback has the disadvantage of large transient voltage spikes at the drain of the power switch and at the secondary rectifier. These spikes are a function of the leakage inductance in the flyback transformer. Snubbers control the effects of the leakage inductance and improve the reliability of the power supply.
Snubbers can be either passive or active networks. Passive snubber network elements are restricted to resistors, capacitors, inductors and diodes. Passive snubbers can control either voltage or current and may be either dissipative or non-dissipative. If the energy in the snubber is dissipated in a resistive element it is classified as a dissipative snubber, but if the energy is returned to the input or moved ahead to the output it is classified as non-dissipative. This application note provides an overview of the different types of passive dissipative voltage snubbers used, guidelines on how they are designed, and their various limitations. In particular, snubbers used to reduce the stress on the switch and improve efficiency in a flyback topology are discussed.
The first section enumerates the need for a snubber on the primary side of a flyback converter. The second section explains the need for a snubber on the output side. This is followed by a discussion of the various types of dissipative voltage snubbers.
The primary leakage inductance, LLP, and the primary winding capacitance in the transformer, CP, and the output capacitance, COSS, of the MOSFET form a parasitic LC network. The peak voltage is given by:
VPEAK = IP (√(LLP/(CP+COSS))) + VIN + VOUT/N
Where IP is the current level circulating at the time the MOSFET turns OFF, N is the ratio of secondary to primary turns, VIN is the input voltage, and VOUT is the output voltage.
The square root term in the above equation represents the characteristic impedance of the parasitic LC network. Note that the highest voltage transient occurs when switching the highest level of current. This voltage overshoot may cause excessive power dissipation in the MOSFET even if it is within safe operating limits of the device and thus reduce the total efficiency. Also, it may cause instability in the loop due to (dv/dt) induced spurious turn-on of the MOSFET as a result of the transient voltage spike.
VPEAK,S = IREC√(LLS /CD) + VIN × N
The damping of the resonant circuit should be optimized as excessive damping can also lead to increased switching times and result in increased losses.
A snubber could therefore be used to clamp the voltage spike or damp the ringing to reduce noise in the system or both. Depending on the function performed by the snubber it can be broadly classified into three categories:

Figure 2A. Voltage clamp snubber.

Figure 2B. Rate-of-rise voltage snubber.

Figure 3. MOSFET turn-off waveforms with clamping.
This implies that the power dissipated in the clamp at turn-off is
PCLAMP = (1/2) × VCLAMP × ICLAMP × Δt × f
Where, f is the switching frequency.
However,
Δt = (LLP × IP)/(VCLAMP - VOUT/N).
The power dissipated in the clamp is through the resistor. Therefore
RCLAMP = [2 × VCLAMP × (VCLAMP - VOUT/N)]/( LLP × IP² × f)
It is important to minimize the ripple, Vripple, superimposed on VCLAMP to keep the MOSFET drain voltage close to the clamp voltage. The minimum value for the capacitor, CCLAMP, is therefore CCLAMP = VCLAMP/ (Vripple × RCLAMP × f).
The capacitor, CCLAMP, should have a low ESR and low inductance to handle the high peak currents during turn-off. The RC time constant of the clamp should be chosen much larger than the switching period of the MOSFET. The series diode used in the clamp should be able handle the peak currents and must be a fast turn-on type.
The RC network may be replaced by a zener diode that can handle the voltage rating and the power dissipation. However, since the zener is not a fast switching device a capacitor may still be needed in parallel with the zener to handle the high frequency currents. Note that this snubber is not used in topologies with a clamped inductive load since it does not reduce ringing.
When the switch turns on, the snubber capacitor will discharge through the snubber resistor and the switch.
The capacitance value is obtained from IP = C (VC/ tr)
Where VC = voltage across the capacitor and tr = rise time of the voltage
The resistor is then chosen based on the time constant required. The RC time constant is much smaller than the switching frequency and, therefore, the power dissipated in the resistor is independent of its value. The power dissipation is determined by the value of the capacitance and the switching frequency. Since there is only one transition (discharge) through the resistor, the power dissipation in the resistor is given by P = (CVC²f)/2.
R = √(Lres/Cres)
Where Lres = parasitic inductance causing the resonance, Cres = parasitic capacitance causing the resonance.
The RC time constant of the snubber should be small compared to the switching period but long compared to the voltage rise time. The snubber capacitance must be larger than the parasitic resonance capacitance, but small enough to minimize dissipation in the snubber resistor. The snubber capacitance is generally chosen to be at least 3 to 4 times the value of the parasitic resonant capacitor. The power dissipated can be estimated from the snubber capacitance as
P = C × (VC)² × f
Where C is the snubber capacitance, VC is the voltage across the snubber capacitor, and f is the switching frequency.
It is very important to pay attention to parasitics in the components used in the snubber since these may render the snubber ineffective. The diodes used in snubbers should be able to handle large peak currents, but the average current is relatively small. The PC board layout may need to provide some heat sink area for these diodes. Capacitors have series inductance and this should be minimized to avoid introduction of any unwanted resonance in the circuit. Some electrostatic capacitors (ceramic and polymer film) offer extremely low ESR and ESL values. Capacitors can be paralleled to reduce circuit inductance. Care must be exercised in using this method. The series inductance of a large capacitance is capable of resonating with a small capacitance in parallel with it and the resulting resonant circuit will have a high Q.
The resistors used should have very low inductance to avoid excessive overshoots and ringing. Avoid using wirewound resistors. The layout should not introduce stray inductance, especially in high current paths. The transformer used in flyback converters should be designed to reduce leakage inductance and minimize overshoot and ringing. The actual design of the transformer is, however, beyond the scope of this application note and will be discussed elsewhere.
The switches in the circuit are usually the most susceptible devices that need snubbing. The switch is also in the input stage of the flyback circuit. In practice, the best procedure is to start from the input and proceed to the output stage when introducing the snubbers into the circuit. Once a node has been shown to need a snubber, the purpose of the snubber should be determined before selecting the type.
A flyback topology application circuit using the MAX1856 is shown in Figure 4. This is an example of using two snubber circuits for different objectives. D3, C11 and R11 form a clamp to limit the drain voltage and R5 with C10 forms a RC snubber to damp the ringing at the secondary rectifier (D2). Comparing the waveforms in Figure 5A and Figure 5B demonstrates the effect of the RC snubber at the secondary rectifier.
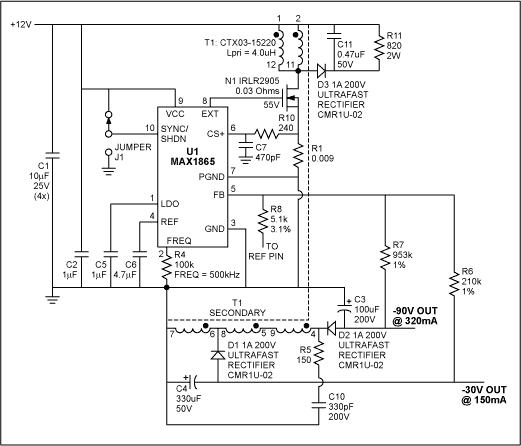
Figure 4. Flyback application circuit using the MAX1856.

Figure 5A. Voltage at the D2 rectifier cathode without a snubber. (CH1= Voltage waveform at EXT/pin 8 of MAX1856; CH2= cathode of rectifier D2).
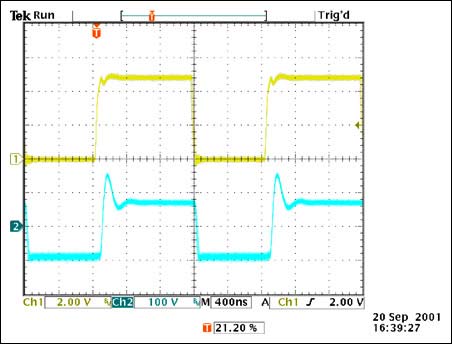
Figure 5B. Voltage at the D2 rectifier cathode with a snubber (R5=150Ω; C10=330 pF). (CH1= Voltage waveform at EXT/pin 8 of MAX1856; CH2= cathode of rectifier D2).
In conclusion, this application note has discussed the use of passive voltage snubbers with particular reference to flyback converter topology. A properly snubbed circuit is more efficient, more reliable and will perform well over time, within temperature and production tolerances. It is important to understand and use the snubber circuits when it is necessary to control switching voltage transients.
The flyback topology (Figure 1A) results in significant cost and space savings for multiple output power supplies with high output voltage for power levels up to 100W. This topology uses a transformer, which is essentially a coupled inductor with multiple windings on the same magnetic core. Flyback topologies operate by storing energy in the transformer during the power switch on-time and transferring this energy to the output during the off-time. The energy is stored in a non-magnetic gap in series with the transformer core. In practice, the multiple windings cannot all be equally well coupled to the core because of the physical separation between the windings. A small amount of energy is also stored within and between these windings. This energy is represented in the circuit as a leakage inductance (Figure 1B).

Figure 1A. Basic topology of flyback circuit.
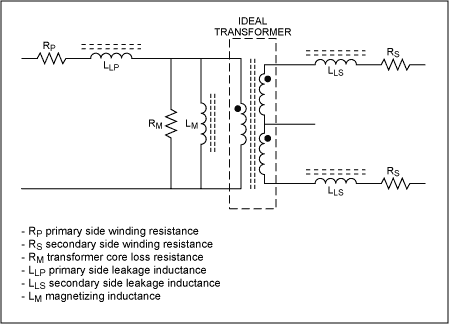
Figure 1B. Equivalent transformer model.
The flyback topology is attractive for multiple output supplies because the output voltages track one another with line and load changes and because adding outputs to the system does not require additional ICs. Despite its advantages, the flyback has the disadvantage of large transient voltage spikes at the drain of the power switch and at the secondary rectifier. These spikes are a function of the leakage inductance in the flyback transformer. Snubbers control the effects of the leakage inductance and improve the reliability of the power supply.
Snubbers can be either passive or active networks. Passive snubber network elements are restricted to resistors, capacitors, inductors and diodes. Passive snubbers can control either voltage or current and may be either dissipative or non-dissipative. If the energy in the snubber is dissipated in a resistive element it is classified as a dissipative snubber, but if the energy is returned to the input or moved ahead to the output it is classified as non-dissipative. This application note provides an overview of the different types of passive dissipative voltage snubbers used, guidelines on how they are designed, and their various limitations. In particular, snubbers used to reduce the stress on the switch and improve efficiency in a flyback topology are discussed.
The first section enumerates the need for a snubber on the primary side of a flyback converter. The second section explains the need for a snubber on the output side. This is followed by a discussion of the various types of dissipative voltage snubbers.
Primary Leakage Inductance and the MOSFET Switch
The primary leakage inductance LLP in a flyback does not participate in the primary to secondary energy transfer and so has a negative impact on efficiency. Since the leakage inductance does not find a path for the current built up in it during the switch on-time, it leads to a voltage spike at the turn-off of the MOSFET and also delays the transfer of power from the primary to the secondary. The parasitic elements in the transformer and the switch determine the magnitude of this voltage spike. At high output voltagesthe circuit parasitics become large relative to the amount of output power delivered.The primary leakage inductance, LLP, and the primary winding capacitance in the transformer, CP, and the output capacitance, COSS, of the MOSFET form a parasitic LC network. The peak voltage is given by:
VPEAK = IP (√(LLP/(CP+COSS))) + VIN + VOUT/N
Where IP is the current level circulating at the time the MOSFET turns OFF, N is the ratio of secondary to primary turns, VIN is the input voltage, and VOUT is the output voltage.
The square root term in the above equation represents the characteristic impedance of the parasitic LC network. Note that the highest voltage transient occurs when switching the highest level of current. This voltage overshoot may cause excessive power dissipation in the MOSFET even if it is within safe operating limits of the device and thus reduce the total efficiency. Also, it may cause instability in the loop due to (dv/dt) induced spurious turn-on of the MOSFET as a result of the transient voltage spike.
Secondary Leakage Inductance and the Rectifier Diode
The transformer secondary leakage inductance may couple with the reverse recovery current IREC of the output rectifier diode to cause ringing when the diode turns off. The transformer secondary leakage inductance LLS and the capacitance CD of the rectifier determine this resonant frequency. The ringing may generate significant radiated and conducted noise. There is typically very little loss in the resonant circuit so this network will cause many cycles of ringing after the spike. The ringing can therefore affect the current sense signal used by the controller in a flyback configuration. The overshoot caused by this ringing may exceed the diode voltage rating and cause damage to the diode. The maximum positive voltage across the rectifier can be estimated asVPEAK,S = IREC√(LLS /CD) + VIN × N
The damping of the resonant circuit should be optimized as excessive damping can also lead to increased switching times and result in increased losses.
A snubber could therefore be used to clamp the voltage spike or damp the ringing to reduce noise in the system or both. Depending on the function performed by the snubber it can be broadly classified into three categories:
- Rate-of-rise control snubber
- Voltage clamp snubber
- Damping snubber
RCD Voltage Snubber
This snubber is applicable to rate-of-rise voltage control and/or clamping. The presence of the diode in the configuration makes this a polarized snubber. The two possible configurations for this resistor-capacitor-diode (RCD) snubber are shown in Figure 2. The configuration shown in Figure 2A can only act as a voltage clamp. The variation shown in Figure 2B is applicable to either rate-of-rise control or clamping of the drain voltage of the switch.
Figure 2A. Voltage clamp snubber.

Figure 2B. Rate-of-rise voltage snubber.
RCD Clamp
In the clamp mode the purpose of the snubber is to clamp the voltage during turn-off at the drain of the MOSFET. The parallel RC circuit may be returned to ground or to a voltage other than ground (i.e., input voltage if the drain can go above input voltage) since this will reduce the power dissipation in the resistor. The MOSFET switch itself will have to sustain the peak power dissipation during turn-off. The value of the capacitor, CCLAMP, and resistor, RCLAMP, is based on the energy stored in the parasitic inductance, as this energy must be discharged into the RC network during each cycle. The voltage across the capacitor and resistor sets the clamp voltage, VCLAMP. The turn-off waveform at the drain of the MOSFET switch is as shown in Figure 3.
Figure 3. MOSFET turn-off waveforms with clamping.
This implies that the power dissipated in the clamp at turn-off is
PCLAMP = (1/2) × VCLAMP × ICLAMP × Δt × f
Where, f is the switching frequency.
However,
Δt = (LLP × IP)/(VCLAMP - VOUT/N).
The power dissipated in the clamp is through the resistor. Therefore
RCLAMP = [2 × VCLAMP × (VCLAMP - VOUT/N)]/( LLP × IP² × f)
It is important to minimize the ripple, Vripple, superimposed on VCLAMP to keep the MOSFET drain voltage close to the clamp voltage. The minimum value for the capacitor, CCLAMP, is therefore CCLAMP = VCLAMP/ (Vripple × RCLAMP × f).
The capacitor, CCLAMP, should have a low ESR and low inductance to handle the high peak currents during turn-off. The RC time constant of the clamp should be chosen much larger than the switching period of the MOSFET. The series diode used in the clamp should be able handle the peak currents and must be a fast turn-on type.
The RC network may be replaced by a zener diode that can handle the voltage rating and the power dissipation. However, since the zener is not a fast switching device a capacitor may still be needed in parallel with the zener to handle the high frequency currents. Note that this snubber is not used in topologies with a clamped inductive load since it does not reduce ringing.
Rate-of-Rise Control RCD Snubber
When the RCD snubber is used to control the rate of voltage rise at the MOSFET drain, the capacitor must be completely charged and discharged during each cycle to be able to control the rate-of-rise of the drain voltage. The RC time constant of the snubber should, therefore, be much smaller than the switching period (consider the effect of duty cycle on pulse width). Typically, the time constant should be about 1/10th the switching period. When the switch turns off, the inductor current is diverted through the snubber diode to charge the capacitor to the rail. At that time, it is expected that the output rectifier will turn on.When the switch turns on, the snubber capacitor will discharge through the snubber resistor and the switch.
The capacitance value is obtained from IP = C (VC/ tr)
Where VC = voltage across the capacitor and tr = rise time of the voltage
The resistor is then chosen based on the time constant required. The RC time constant is much smaller than the switching frequency and, therefore, the power dissipated in the resistor is independent of its value. The power dissipation is determined by the value of the capacitance and the switching frequency. Since there is only one transition (discharge) through the resistor, the power dissipation in the resistor is given by P = (CVC²f)/2.
Simple RC Snubber
This is probably the most widely used snubber and is applicable for both rate-of-rise control and damping. In inductively clamped topologies, where there is still some stray inductance, the RC snubber can be used to reduce the peak power dissipation in the switch by controlling the rate-of-rise of drain voltage. The RC snubber, however, will absorb energy during each voltage transition and can reduce efficiency. Also, the RC snubber will reduce the switching speed of the MOSFET switch. Care must be used in choosing the value of R and C to optimize the total performance. The main application of a RC snubber is to damp parasitic ringing in the circuit due to unclamped inductance in configurations such as the flyback converter. In these applications, the value of the resistor must be close to the characteristic impedance of the parasitic resonant circuit it is intended to damp. Choose the snubber resistor to beR = √(Lres/Cres)
Where Lres = parasitic inductance causing the resonance, Cres = parasitic capacitance causing the resonance.
The RC time constant of the snubber should be small compared to the switching period but long compared to the voltage rise time. The snubber capacitance must be larger than the parasitic resonance capacitance, but small enough to minimize dissipation in the snubber resistor. The snubber capacitance is generally chosen to be at least 3 to 4 times the value of the parasitic resonant capacitor. The power dissipated can be estimated from the snubber capacitance as
P = C × (VC)² × f
Where C is the snubber capacitance, VC is the voltage across the snubber capacitor, and f is the switching frequency.
It is very important to pay attention to parasitics in the components used in the snubber since these may render the snubber ineffective. The diodes used in snubbers should be able to handle large peak currents, but the average current is relatively small. The PC board layout may need to provide some heat sink area for these diodes. Capacitors have series inductance and this should be minimized to avoid introduction of any unwanted resonance in the circuit. Some electrostatic capacitors (ceramic and polymer film) offer extremely low ESR and ESL values. Capacitors can be paralleled to reduce circuit inductance. Care must be exercised in using this method. The series inductance of a large capacitance is capable of resonating with a small capacitance in parallel with it and the resulting resonant circuit will have a high Q.
The resistors used should have very low inductance to avoid excessive overshoots and ringing. Avoid using wirewound resistors. The layout should not introduce stray inductance, especially in high current paths. The transformer used in flyback converters should be designed to reduce leakage inductance and minimize overshoot and ringing. The actual design of the transformer is, however, beyond the scope of this application note and will be discussed elsewhere.
The switches in the circuit are usually the most susceptible devices that need snubbing. The switch is also in the input stage of the flyback circuit. In practice, the best procedure is to start from the input and proceed to the output stage when introducing the snubbers into the circuit. Once a node has been shown to need a snubber, the purpose of the snubber should be determined before selecting the type.
A flyback topology application circuit using the MAX1856 is shown in Figure 4. This is an example of using two snubber circuits for different objectives. D3, C11 and R11 form a clamp to limit the drain voltage and R5 with C10 forms a RC snubber to damp the ringing at the secondary rectifier (D2). Comparing the waveforms in Figure 5A and Figure 5B demonstrates the effect of the RC snubber at the secondary rectifier.
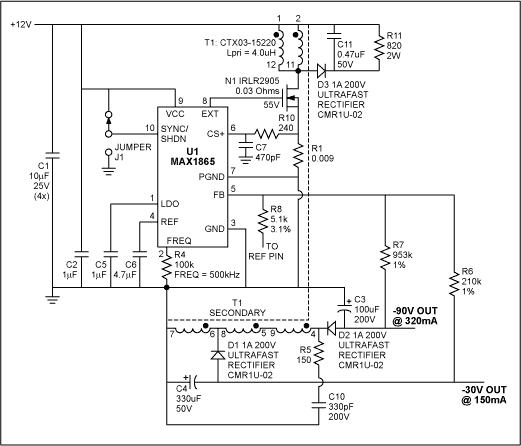
Figure 4. Flyback application circuit using the MAX1856.

Figure 5A. Voltage at the D2 rectifier cathode without a snubber. (CH1= Voltage waveform at EXT/pin 8 of MAX1856; CH2= cathode of rectifier D2).
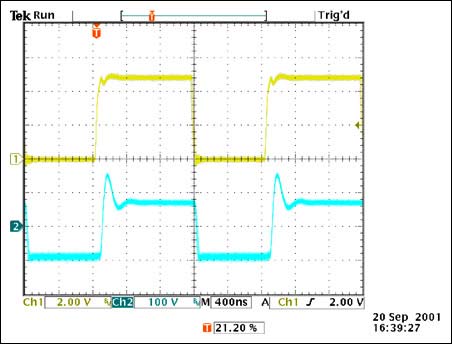
Figure 5B. Voltage at the D2 rectifier cathode with a snubber (R5=150Ω; C10=330 pF). (CH1= Voltage waveform at EXT/pin 8 of MAX1856; CH2= cathode of rectifier D2).
In conclusion, this application note has discussed the use of passive voltage snubbers with particular reference to flyback converter topology. A properly snubbed circuit is more efficient, more reliable and will perform well over time, within temperature and production tolerances. It is important to understand and use the snubber circuits when it is necessary to control switching voltage transients.
评论