数控机床主要由传统的数控系统,加上伺服、位置反馈系统组成,普通机床改造的目的是利用数控系统控制机床自动完成机械加工任务,提高机床的生产效率和加工精度。在改造中需要解决的问题是把机床的手动进给和机床的换刀,改造成由伺服驱动控制的进给和数控系统PLC控制的刀架自动换位。本文以CA6140型普通机床为例,介绍普通机床的数控化改造步骤和方法。
改造的总体思路为通过数控系统对输入的零件加工程序进行运算处理,然后通过输入/输出接口控制步进驱动模块,由驱动模块发出步进脉冲驱动步进电机,经同步齿形传动带(简称同步带)使滚珠丝杠转动,从而带动刀架实现纵向和横向的进给。螺纹的车削由编码器控制,电动刀架的换刀由数控系统内部的PLC控制。改造步骤如下:
1.选择数控系统由于伺服电机驱动器及电机的价格比较高,故选用“广数”的DY3三相混合式步进电机驱动器及步进电机。并且该系统的编程格式与FANUC系统很接近,GSK980TA系统还可以控制步进电机,所以是最合适的。
2.Z向进给系统(纵向进给)纵向进给由Z向进给电机经同步传动带使滚珠丝杠转动,然后通过丝杠螺母带动大拖板左右运动,步进电机通常安装在纵向丝杠的右端。Z向步进电机的型号为1106GB350B,参数:电流2.8A。步距角0.03°/0.75°,转矩12N/m。
改造方法:
(1)拆下普通丝杠、光杠与溜板箱,把溜板箱内的齿板、传动轴拆除,加工一个螺母固定套,安装在溜板箱内,改由步进电机驱动滚珠丝杠,根据CA6140车床的最大负荷,选取滚珠丝杠直径为40mm,型号为CD40x6-3.5-E2,其额定动载荷是19kN,强度足够。
(2)加工右端的支撑座和两个支撑孔,孔的位置精度要求很高,使其分别与电机的支撑轴和支撑丝杠的轴承同轴配合。
(3)加工左端的支撑座,用于固定丝杠的左端,保证支撑座底面的平面度。
(4)对安装螺母的支撑座进行铣、磨、钻、攻丝等加工,保证其形位公差。
(5)装配后,对滚珠丝杠与导轨的平行度进行调整,确保丝杠传动平稳,受力均匀。
3.X向进给系统(横向进给)横向进给由X步进电机直接驱动滚珠丝杠,使刀架横向运动。
步进电机安装在大拖板后,为了保证同轴度和传动精度,用法兰盘将步进电机与溜板箱固定在一起。X向步进电机的型号为110BYG350A,参数:电流2.4A,步距角0.03°/0.8°,转矩8N/m。
改造方法:
(1)拆下小拖板、刀架及丝杠、手轮,留下小拖板,其余的不用。
(2)加工法兰盘,保证法兰盘孔与大拖板后孔的同轴度,最后配钻四个螺纹孔,并攻螺纹。
(3)加工一个连接套用于连接丝杠与电机主轴。
(4)铣去大拖板上与螺母发生干涉的部位,将螺母安装在大拖板上。
(5)安装完成后,用垫片调整螺母上下位置,使丝杠运行平稳,受力均匀。
4.刀架为了提高生产效率、缩短辅助加工时间,刀架要求有自动换刀功能。经济型数控机床一般都选用宏达四方电动刀架,这种刀架简单、经济实用。刀架的转动由三相电机驱动,到位信号由霍尔元件来检测。
改造方法:
(1)拆除原手动刀架。
(2)在小拖板上钻四个安装孔,并攻丝,安装好电动刀架。安装好中间继电器、正反转接触器和热继电器,然后调试刀架,电源相序接反的话,任换两相即可。
5.编码器车螺纹时,主轴转一圈,刀具移动一个螺距。为了保证不乱扣,主轴与丝杠应保持同步动作。主轴与丝杠的同步动作由编码器来保证(可见编码器的重要性)。为了保证同步动作,编码器与主轴的传动比应为1:1,可以用尼龙板制作两个齿数相同的齿轮。然后制作一个可调支架,以保证两个齿轮能正确地啮合。
改造方法:
(1)拆下原有齿轮,装上塑料齿轮,调整支架位置,保证正确啮合。
(2)试切螺纹,看连接是否有误。
6.行程开关行程开关用来保证工作台运行在安全的位置,和作为机械回零的检测信号。
改造方法:
(1)配钻螺纹孔,并攻螺纹,安装行程开关和挡块。
(2)调整挡块的位置,使减速信号和回零信号分开。
-
数控车床
+关注
关注
2文章
80浏览量
16568
发布评论请先 登录
宝山回收普通车床,普陀回收线路板
数控车床加工实验
数控车床基本操作
简介车床数控化改造中PLC的使用
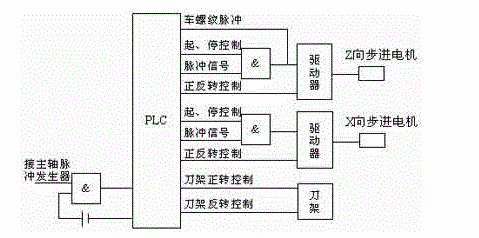
数控车床的组成
数控车床的基本构成
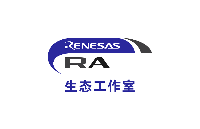
瑞萨RA8系列教程 | 基于 RASC 生成 Keil 工程
对于不习惯用 e2 studio 进行开发的同学,可以借助 RASC 生成 Keil 工程,然后在 Keil 环境下愉快的完成开发任务。
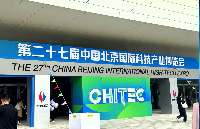
共赴之约 | 第二十七届中国北京国际科技产业博览会圆满落幕
作为第二十七届北京科博会的参展方,芯佰微有幸与800余家全球科技同仁共赴「科技引领创享未来」之约!文章来源:北京贸促5月11日下午,第二十七届中国北京国际科技产业博览会圆满落幕。本届北京科博会主题为“科技引领创享未来”,由北京市人民政府主办,北京市贸促会,北京市科委、中关村管委会,北京市经济和信息化局,北京市知识产权局和北辰集团共同承办。5万平方米的展览云集
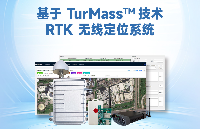
道生物联与巍泰技术联合发布 RTK 无线定位系统:TurMass™ 技术与厘米级高精度定位的深度融合
道生物联与巍泰技术联合推出全新一代 RTK 无线定位系统——WTS-100(V3.0 RTK)。该系统以巍泰技术自主研发的 RTK(实时动态载波相位差分)高精度定位技术为核心,深度融合道生物联国产新兴窄带高并发 TurMass™ 无线通信技术,为室外大规模定位场景提供厘米级高精度、广覆盖、高并发、低功耗、低成本的一站式解决方案,助力行业智能化升级。
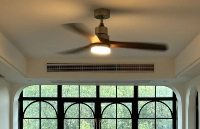
智能家居中的清凉“智”选,310V无刷吊扇驱动方案--其利天下
炎炎夏日,如何营造出清凉、舒适且节能的室内环境成为了大众关注的焦点。吊扇作为一种经典的家用电器,以其大风量、长寿命、低能耗等优势,依然是众多家庭的首选。而随着智能控制技术与无刷电机技术的不断进步,吊扇正朝着智能化、高效化、低噪化的方向发展。那么接下来小编将结合目前市面上的指标,详细为大家讲解其利天下有限公司推出的无刷吊扇驱动方案。▲其利天下无刷吊扇驱动方案一
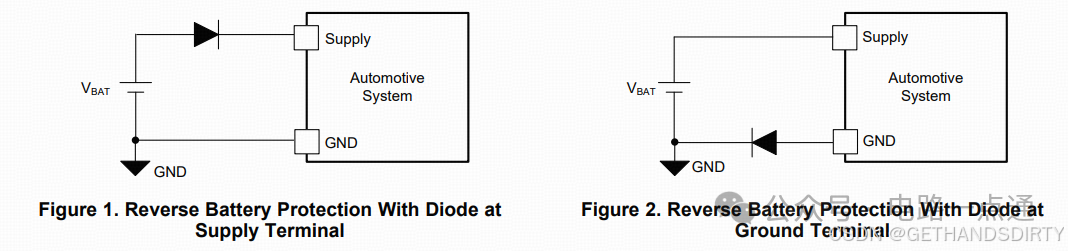
电源入口处防反接电路-汽车电子硬件电路设计
一、为什么要设计防反接电路电源入口处接线及线束制作一般人为操作,有正极和负极接反的可能性,可能会损坏电源和负载电路;汽车电子产品电性能测试标准ISO16750-2的4.7节包含了电压极性反接测试,汽车电子产品须通过该项测试。二、防反接电路设计1.基础版:二极管串联二极管是最简单的防反接电路,因为电源有电源路径(即正极)和返回路径(即负极,GND),那么用二极
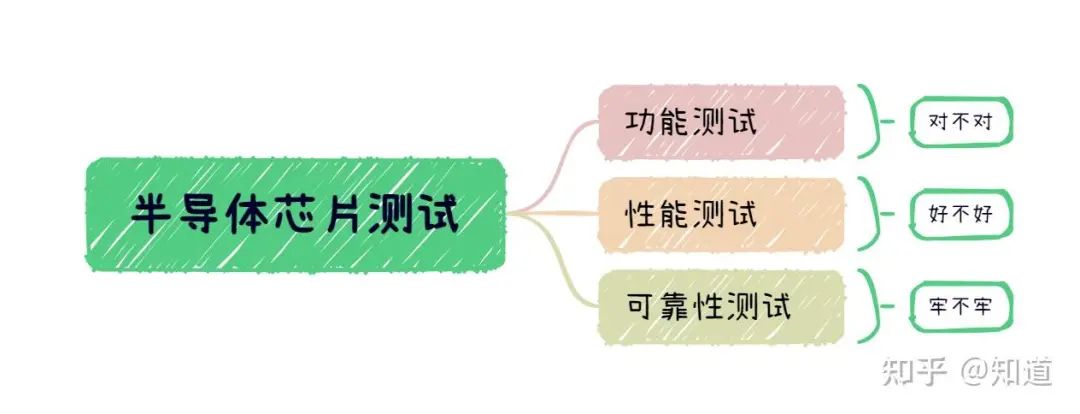
半导体芯片需要做哪些测试
首先我们需要了解芯片制造环节做⼀款芯片最基本的环节是设计->流片->封装->测试,芯片成本构成⼀般为人力成本20%,流片40%,封装35%,测试5%(对于先进工艺,流片成本可能超过60%)。测试其实是芯片各个环节中最“便宜”的一步,在这个每家公司都喊着“CostDown”的激烈市场中,人力成本逐年攀升,晶圆厂和封装厂都在乙方市场中“叱咤风云”,唯独只有测试显
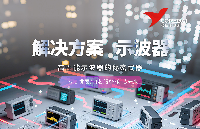
解决方案 | 芯佰微赋能示波器:高速ADC、USB控制器和RS232芯片——高性能示波器的秘密武器!
示波器解决方案总述:示波器是电子技术领域中不可或缺的精密测量仪器,通过直观的波形显示,将电信号随时间的变化转化为可视化图形,使复杂的电子现象变得清晰易懂。无论是在科研探索、工业检测还是通信领域,示波器都发挥着不可替代的作用,帮助工程师和技术人员深入剖析电信号的细节,精准定位问题所在,为创新与发展提供坚实的技术支撑。一、技术瓶颈亟待突破性能指标受限:受模拟前端
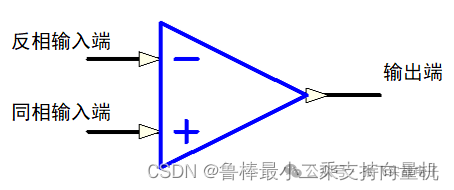
硬件设计基础----运算放大器
1什么是运算放大器运算放大器(运放)用于调节和放大模拟信号,运放是一个内含多级放大电路的集成器件,如图所示:左图为同相位,Vn端接地或稳定的电平,Vp端电平上升,则输出端Vo电平上升,Vp端电平下降,则输出端Vo电平下降;右图为反相位,Vp端接地或稳定的电平,Vn端电平上升,则输出端Vo电平下降,Vn端电平下降,则输出端Vo电平上升2运算放大器的性质理想运算
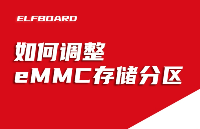
ElfBoard技术贴|如何调整eMMC存储分区
ELF 2开发板基于瑞芯微RK3588高性能处理器设计,拥有四核ARM Cortex-A76与四核ARM Cortex-A55的CPU架构,主频高达2.4GHz,内置6TOPS算力的NPU,这一设计让它能够轻松驾驭多种深度学习框架,高效处理各类复杂的AI任务。
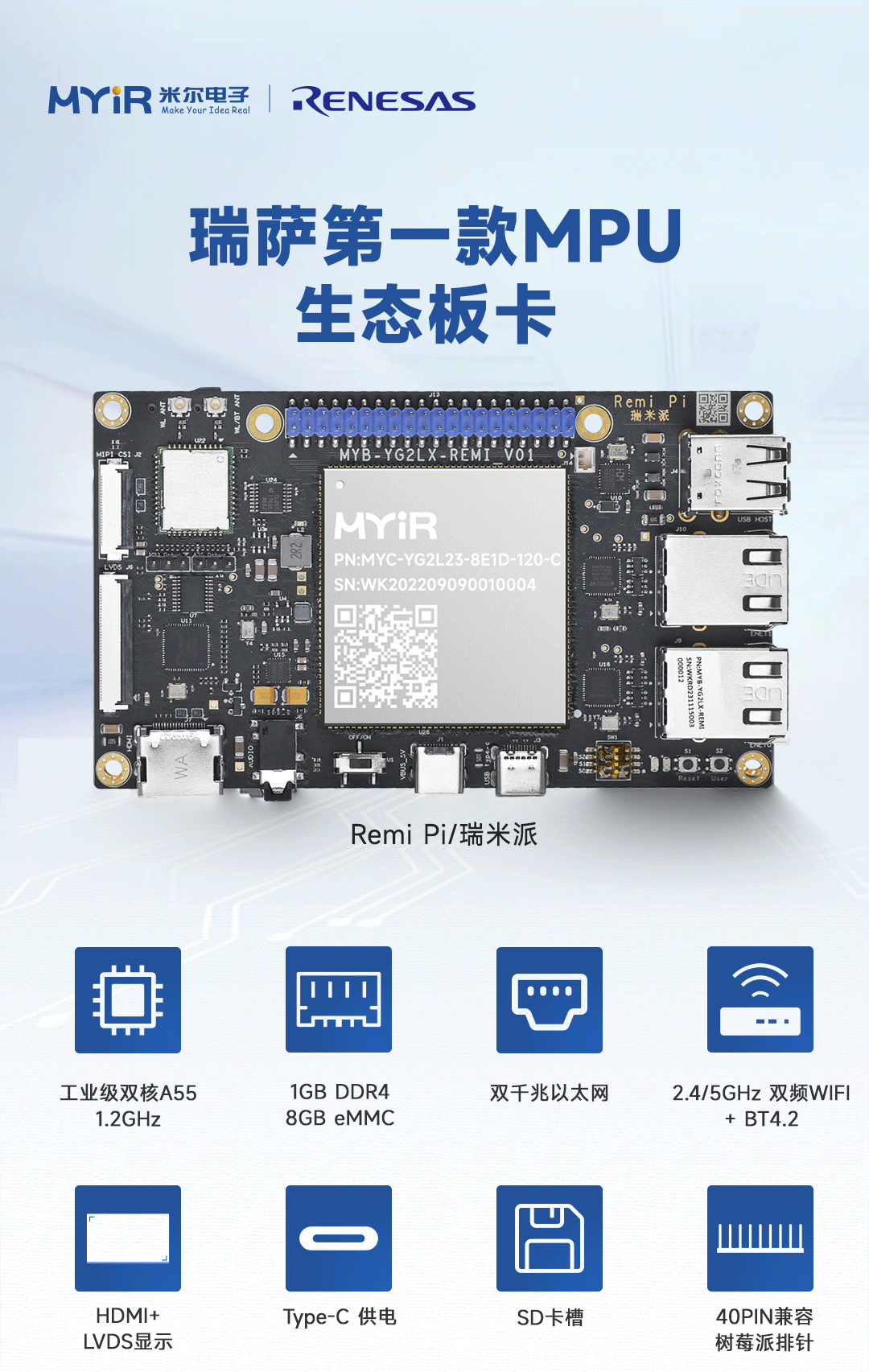
米尔基于MYD-YG2LX系统启动时间优化应用笔记
1.概述MYD-YG2LX采用瑞萨RZ/G2L作为核心处理器,该处理器搭载双核Cortex-A55@1.2GHz+Cortex-M33@200MHz处理器,其内部集成高性能3D加速引擎Mail-G31GPU(500MHz)和视频处理单元(支持H.264硬件编解码),16位的DDR4-1600/DDR3L-1333内存控制器、千兆以太网控制器、USB、CAN、
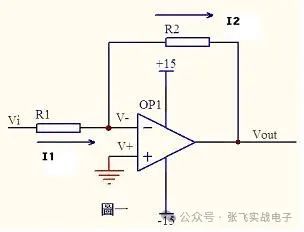
运放技术——基本电路分析
虚短和虚断的概念由于运放的电压放大倍数很大,一般通用型运算放大器的开环电压放大倍数都在80dB以上。而运放的输出电压是有限的,一般在10V~14V。因此运放的差模输入电压不足1mV,两输入端近似等电位,相当于“短路”。开环电压放大倍数越大,两输入端的电位越接近相等。“虚短”是指在分析运算放大器处于线性状态时,可把两输入端视为等电位,这一特性称为虚假短路,简称
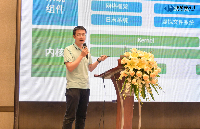
飞凌嵌入式携手中移物联,谱写全国产化方案新生态
4月22日,飞凌嵌入式“2025嵌入式及边缘AI技术论坛”在深圳成功举办。中移物联网有限公司(以下简称“中移物联”)携OneOS操作系统与飞凌嵌入式共同推出的工业级核心板亮相会议展区,操作系统产品部高级专家严镭受邀作《OneOS工业操作系统——助力国产化智能制造》主题演讲。
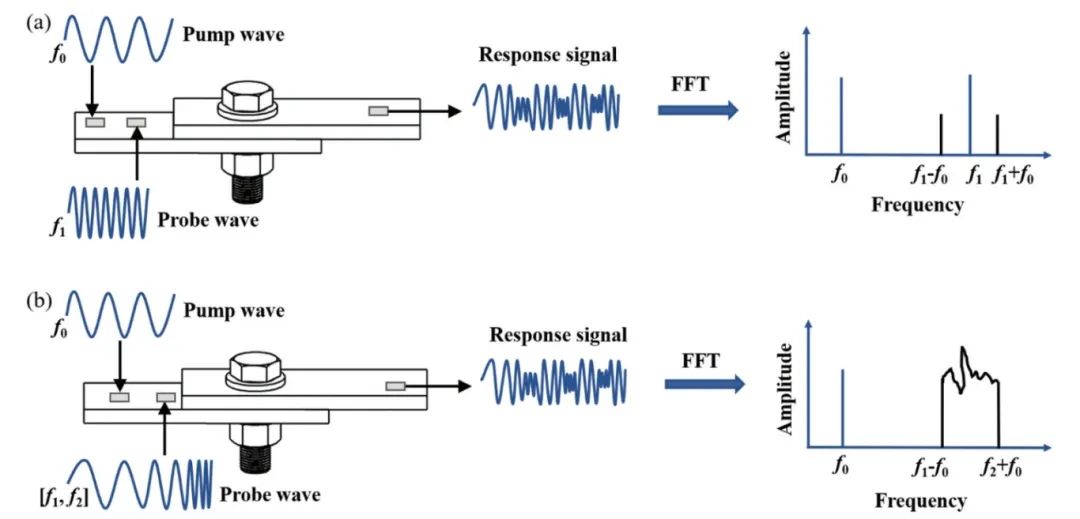
ATA-2022B高压放大器在螺栓松动检测中的应用
实验名称:ATA-2022B高压放大器在螺栓松动检测中的应用实验方向:超声检测实验设备:ATA-2022B高压放大器、函数信号发生器,压电陶瓷片,数据采集卡,示波器,PC等实验内容:本研究基于振动声调制的螺栓松动检测方法,其中低频泵浦波采用单频信号,而高频探测波采用扫频信号,利用泵浦波和探测波在接触面的振动声调制响应对螺栓的松动程度进行检测。通过螺栓松动检测
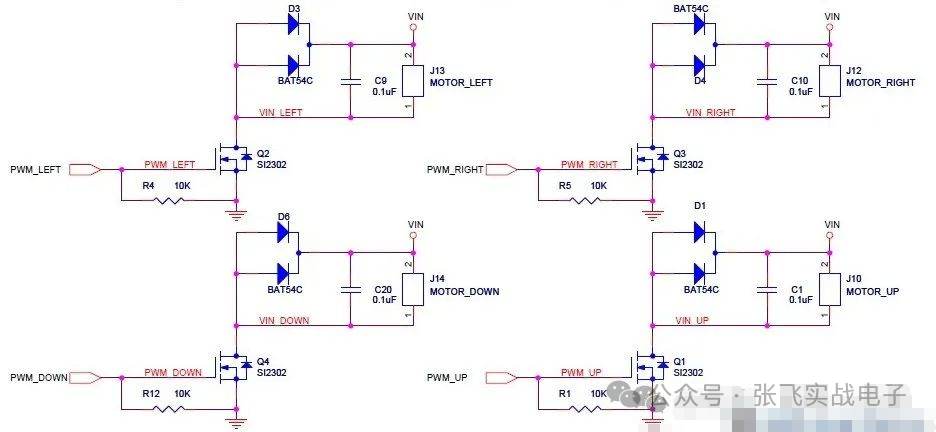
MOS管驱动电路——电机干扰与防护处理
此电路分主电路(完成功能)和保护功能电路。MOS管驱动相关知识:1、跟双极性晶体管相比,一般认为使MOS管导通不需要电流,只要GS电压(Vbe类似)高于一定的值,就可以了。MOS管和晶体管向比较c,b,e—–>d(漏),g(栅),s(源)。2、NMOS的特性,Vgs大于一定的值就会导通,适合用于源极接地时的情况(低端驱动),只要栅极电压达到4V或10V就可以
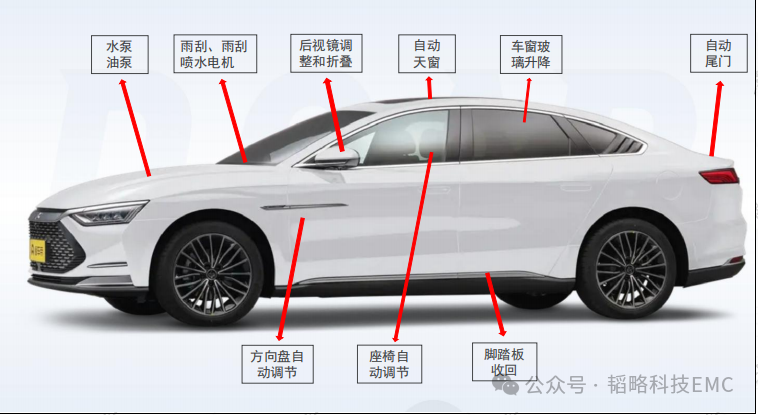
压敏(MOV)在电机上的应用剖析
一前言有刷直流电机是一种较为常见的直流电机。它的主要特点包括:1.结构相对简单,由定子、转子、电刷和换向器等组成;2.通过电刷与换向器的接触来实现电流的换向,从而使电枢绕组中的电流方向周期性改变,保证电机持续运转;3.具有调速性能较好等优点,可以通过改变电压等方式较为方便地调节转速。有刷直流电机在许多领域都有应用,比如一些电动工具、玩具、小型机械等。但它也存
评论